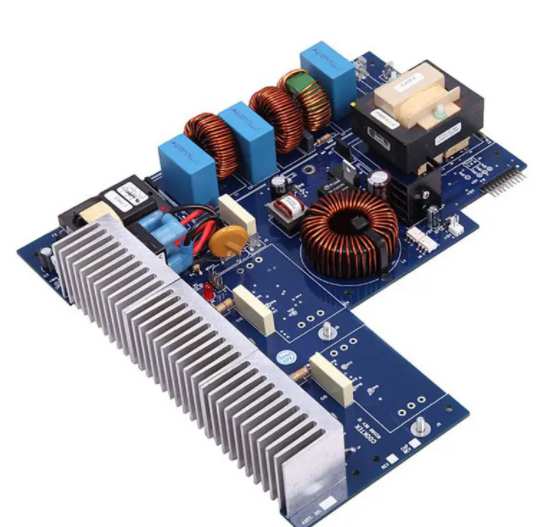
1.SMT reflow soldering is a welding method that forms solder joints by melting a pre-placed solder surface without adding any additional solder during the welding process. The advantages of this process are easy to control, oxidation can be prevented during welding, and production costs are relatively easy to control.
Circuit board
Reflow welding has become the mainstream process of surface mounting, it depends on the influence of hot gas flow on the solder joint, colloidal flux in a certain high temperature air flow for physical reaction, achieve SMD welding, the quality of PCBA solder joint completely depends on the performance of reflow welding equipment and the setting of temperature curve. The requirement for reflow welding cooling process is put forward, which also promotes the development of cooling zone of reflow welding equipment.
Due to the production and processing of reflow welding equipment, higher temperature control accuracy, temperature uniformity in temperature zone and transmission speed are required. Different welding systems have been developed from the initial three temperature zones, such as eight temperature zones and ten temperature zones, and the welding process and results are getting better and better.
2.SMT patch component disassembly trick
Generally speaking, disassembly SMT patch processing components is not a simple thing, only we strengthen the practice, can master the skills, otherwise forcibly disassembly SMD components, they will cause some damage, for you to introduce SMT patch components disassembly tips:
SMT patch
1. The disassembly method of SMT patch components is related to the characteristics of the components themselves. For components with fewer pins, such as resistors, capacitors, diodes or triodes, first weld one of the pads to the PCB circuit board. Use the tweezers in the left hand to clamp the mounting position and close to the circuit board. Then, use the soldering iron in the right hand to weld the pins to the tinned pad. The left tweezers can be loosened and the remaining feet can be welded with tin wire. If you want to disassemble these parts, it is easy to heat both ends of the parts with a soldering iron. Once the tin has melted, gently lift the piece to remove it.
2. A similar approach is used for SMT patch components with multiple pins and wide spacing. First, the pad is tinned, then one foot is welded with a tweezer holding the piece in the left hand, then the other foot is welded with a tin wire. It is usually best to remove such components using a heat gun. Hold a heat gun in one hand to blow the solder, and use a clamp such as tweezers to remove the parts while the solder melts with the other hand.
3. For components with high pin density, the welding procedure is similar, that is, one pin is welded first, and then other pins are welded with tin wire. The number of pins is large and dense, and the alignment of pins and pads is the key. Usually, a small amount of tin is selected for the pad at the corner. Align the component with the pad with SMT patchtweezers or hands, align the edges with the pins, press the component firmly against the PCB, and weld the corresponding pins of the pad with the soldering iron.
The above is about the introduction of " components dismantling tips", I hope to be helpful to you, more PCBA information please pay attention to kingford,kigford is a professional PCBA processing enterprise, with automatic SMT production line and wave soldering, for you to open the whole production and quality testing process, contact us, You belong to have their own electronic processing plant!