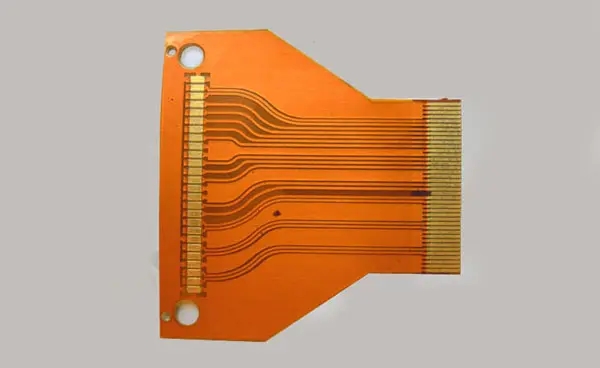
New energy vehicle power battery - FPC reinforcement overall solution
Circuit board manufacturing, circuit board design and PCBA processing manufacturers will explain to you the new energy vehicle power battery - FPC reinforcement overall solution
Adhesives, adhesive tapes and films are very critical and indispensable supporting materials for automobile manufacturing. In new energy vehicles, if the power battery is compared to the heart of new energy vehicles, the adhesive is the sarcolemma tissue that realizes the lasting power of the heart: the increase of three electric systems (battery, motor, electronic control) makes the consumption of new energy vehicles increase by 200%~300% compared with traditional vehicles.
The high-precision and intelligent BMS solution can intelligently manage the battery pack of electric vehicles, improve the performance and service life of the battery, ensure the safety, durability and power of the battery, and prevent safety accidents of electric vehicles.
New energy vehicles will certainly use FPC to replace wire harnesses in a large number, which will be implemented in multiple parts of the vehicle. Therefore, FPC technology is a very important trend in automotive electronics, especially in intelligent vehicles, especially in battery BMS, vehicle lighting systems, door control systems, camera modules, etc.
According to the industry development report in recent years, the new energy industry has become a global focus, not only including body manufacturing, but also power batteries; At present, FPC applications cover relevant scenarios such as lamps, display modules, BMS (battery management system)/VCU (vehicle controller)/MCU (core power electronic unit) three power control systems, sensors, and advanced auxiliary systems. The single vehicle FPC consumption will exceed 100 pieces. The demand for power battery FPC is also growing rapidly. The latest data shows that the proportion of FPC in automobile PCB has increased from 12% to 15%, and will continue to grow in the future.
The power battery FPC is mainly used on lithium batteries to replace the traditional copper wire harness. Previously, the traditional copper wire harness scheme was adopted for the power battery acquisition line of new energy vehicles. The conventional wire harness is made of plastic surrounded by copper wire, which occupies a large space. Compared with copper wire harness, FPC has outstanding advantages in terms of safety, lightweight, and regular layout due to its high integration, ultra-thin thickness, super flexibility and other characteristics.
FPC is light and short, so it is easy to produce discounts, scars, etc. during use; Low mechanical strength, easy to crack.
UV glue is a kind of fast curing glue that can be cured by ultraviolet light. It is widely used in the industrial electronics field and is specially used for FPC reinforcement and solder joint protection.
1. UV glue has the characteristics of high viscosity, high toughness and good ductility;
2. Under ultraviolet light, it can be cured in a few seconds to produce a strong adhesive property;
3. After curing, the adhesive layer is tough, anti vibration, high strength, aging resistance, impact resistance and good weather resistance;
4. It can protect the solder joints on the circuit board to prevent short circuit;
5. Enhance the tensile strength of the tin spot, enhance the bonding strength of the tin spot and the substrate, and effectively improve the performance of the electrical appliance.
As the form and quantity of battery modules of each new energy vehicle are different, the specification and usage of power battery FPC are also different, so customization design and development are required in the early stage. Generally speaking, the larger the capacity of the battery module, the longer the FPC length required, and the higher the process difficulty and cost of FPC products. In addition, the current industry is dominated by single panel products. In the future, with the further improvement of power battery density, FPC product materials and processes are also facing further upgrading.
PCB manufacturers, PCB designers and PCBA manufacturers will explain the overall solution of FPC reinforcement for new energy vehicle power batteries.