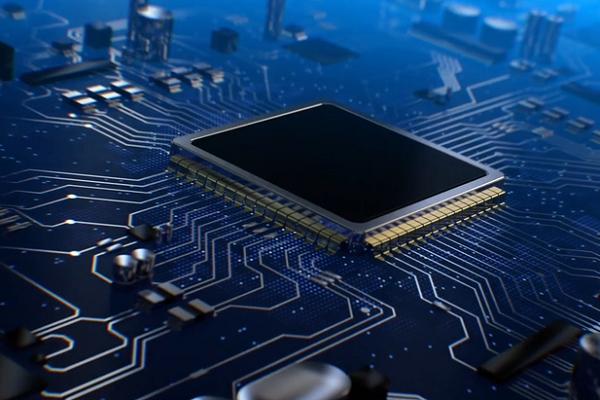
Analysis of Ink Spraying Technology for PCB Soldering Resistance
The basic components of PCB we see in our daily life are generally solder mask, silk screen layer, copper wire, etc. In other words, the part printed with green paint on the PCB surface is called solder mask; The solder mask layer uses negative output in the production process, so after the shape of the solder mask layer is mapped to the PCB, the copper skin is exposed instead of green oil solder mask. The role of the solder mask in controlling the reflow process is very important.
The soldering process in PCB printing is to screen print printed boards with soldering resistance. Use the exposure plate to cover the bonding pad on the printed circuit board, so that it will not be exposed to ultraviolet radiation during exposure. The solder mask will be more firmly attached to the printed circuit board surface after ultraviolet radiation. The bonding pad will not be exposed to ultraviolet radiation, so that the copper bonding pad can be exposed, so as to apply lead and tin during hot air leveling. Today, Mr. Chen wants to focus on the process of the solder mask.
1. Prebake
Pre drying is to evaporate the solvent contained in the ink, so that the solder mask becomes non stick. The type of ink is different, and its pre drying temperature and time are also different. Too long drying time or too high pre drying temperature will reduce the resolution and cause poor development; If the pre drying time is too short or the temperature is too low, the negative film will stick when exposed, and the solder mask will be eroded by sodium carbonate solution during development, causing the surface to lose luster or the solder mask to expand and fall off.
2. Exposure
Exposure is the key to the whole process. If the exposure is excessive, due to light scattering, the solder mask at the edge of the pattern or line reacts with the light (mainly the photosensitive polymer contained in the solder mask reacts with the light) to generate a residual film, which reduces the resolution, resulting in smaller developed patterns and thinner lines; If the exposure is insufficient, the result is contrary to the above, and the developed figure becomes larger and the lines become thicker. This situation can be reflected by the test: if the exposure time is long, the measured line width is negative tolerance; If the exposure time is short, the measured line width is a positive tolerance. In the actual process, the "light energy integrator" can be selected to determine the optimal exposure time.
3. Ink viscosity adjustment
The viscosity of dynamic photosensitive solder resist ink is mainly controlled by the ratio of hardener and main agent and the addition amount of thinner. If the addition of hardener is not enough, it may cause imbalance of ink characteristics.
In contrast, 2020 is the year when the development of 5G communication in the world is booming. In daily design and use, the performance of low Dk/Df materials for 5G communication is mainly determined by plates, followed by solder resist inks. However, we can not ignore that the domestic PCB ink production and manufacturing, especially the IC packaging substrate solder mask ink, automotive electronic PCB solder mask oil, solder mask dry film and other technologies still have a large gap with the world's advanced level. As for the final process treatment of solder mask - paint spraying, we adopt the following methods:
The spraying technology of solder resist ink, which has been applied maturely at present, includes screen printing, electrostatic spraying, low-voltage spraying and other technologies. Now Lao Chen will show you the advantages and disadvantages of these methods. Screen printing requires a large number of skilled screen printing personnel (note that the quality and experience of screen printing personnel must be ensured here). It is precisely because of the greatest demand for human resources, which is generally the most oil saving and ink saving coating method. As for screen printing, if automatic screen printing machine is used, it is suitable for large batches of plates; But expensive is not his shortcoming, but mine; In addition, this batch production machine is very unfriendly to small batch PCBs. Electrostatic spraying technology is very mature, which can save a lot of labor. Template and batch plate are applicable, but ink consumption is large, equipment is relatively expensive, and maintenance costs are high; Low pressure spraying technology still needs to be optimized and improved in many places, and the ink consumption is large, but the advantages are that the equipment is relatively cheap and the maintenance cost is low. Whether low pressure spraying technology can become the mainstream coating technology remains to be seen, and the number of people currently using it is also small.
Ink jet printing solder mask ink is a relatively gradual development process. The research results of a large number of enterprises in the past few years show that a considerable number of enterprises have not continued to develop new ink-jet processes. The current application depends on the development of ink raw materials and equipment. At present, there are very few kinds of materials for ink-jet printing and solder resist ink, and the accuracy and efficiency of the equipment need to be improved. These are the shortcomings of ink-jet printing solder mask ink at present, which is also the direction we are striving for.
PCB manufacturers, PCB designers and PCBA manufacturers will explain the ink spraying technology analysis of PCB solder resistance.