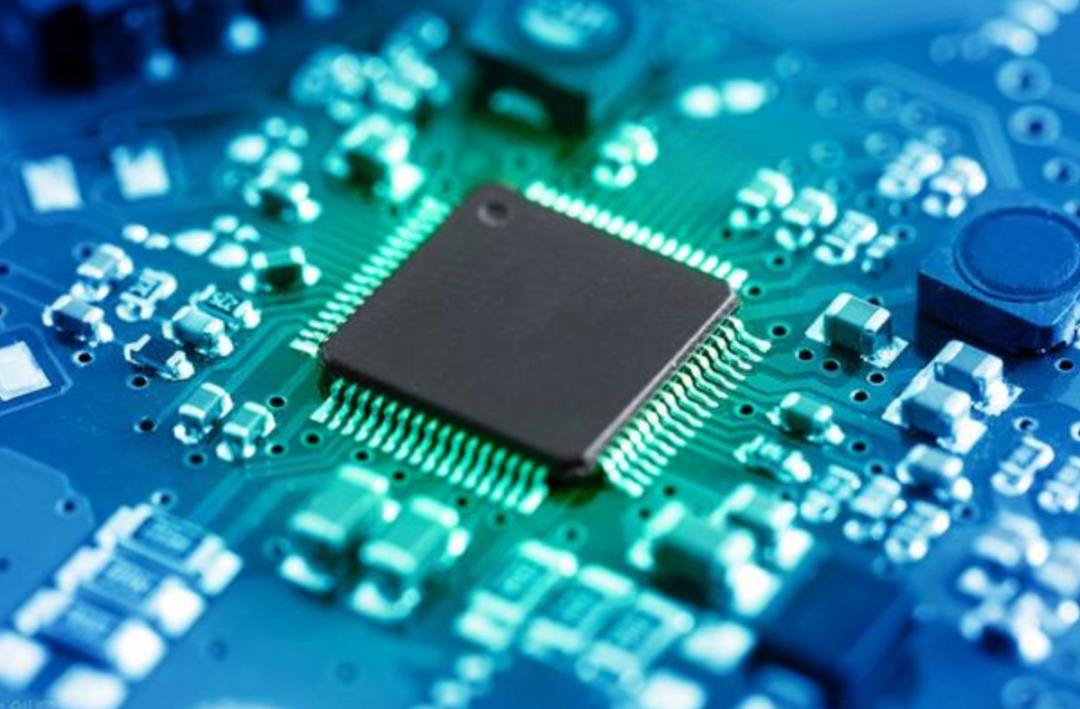
SMT manufacturing
SMT is Surface Mount Technology (Surface Mount Technology) (abbreviation of Surface Mount Technology), known as surface mount or surface mount technology. It is currently the most popular technology and process in the electronic processing industry. Generally speaking, the temperature specified in the SMT workshop is 25±3°C.
Solder paste: when printing solder paste, the materials and tools required are solder paste, steel plate, scraper, wiping paper, dust-free paper, cleaning agent, and mixing knife.
The ingredients of solder paste include: metal powder, solvent, flux, anti-sagging agent, and active agent. The main components are tin powder and flux, and the ratio of volume to weight is about 9:1. The flux begins to volatilize in the constant temperature zone for chemical cleaning; the main function of the flux in soldering is to remove oxides, destroy the surface tension of molten tin, and prevent re-oxidation. Rosin-based fluxes can be divided into four types: R﹑RA﹑RSA﹑RMA; the ratio of lead solder Sn/Pb is 63/37, and the melting point is 217℃. The lead-free solder Sn/Ag/Cu is 96.5/3.0/0.5, and the melting point is 217°C.
When the solder paste is taken out of the refrigerator and used after opening, it must go through two important processes of warming and stirring. The purpose of warming up is to restore the temperature of the refrigerated solder paste to normal temperature for printing. If the temperature is not returned, tin balls will be easily produced after the PCB circuit board enters reflow soldering. The principle of taking solder paste is first in first out. The solder paste currently on the market actually only has a tack time of 4 hours.
Steel mesh and PCB circuit board: The common production methods of steel mesh are: etching, laser, and electroforming. The commonly used SMT chip processing steel mesh is made of stainless steel. The thickness is 0.15mm (or 0.12mm). SMT chip processing generally has stencil openings that are 4um smaller than PCB circuit board PADs to prevent solder balls from being defective.
The commonly used PCB circuit board material is FR-4; the purpose of PCB circuit board vacuum packaging is to prevent dust and moisture. The PCB circuit board warpage specification does not exceed 0.7% of its diagonal.
Components: Commonly used passive components (Passive Devices) include: resistors, capacitors, inductors, diodes, etc., and these components are sucked by the nozzle of the placement machine, referred to as the nozzle or nozzle; active components (Active Devices) include: transistors, ICs, etc. The control relative temperature and humidity of the component drying oven is <10%. After the IC is unpacked, the humidity on the display card is greater than 30%, which means that the IC is damp and absorbs moisture.
Constant temperature reflow soldering: The maximum temperature of the reflow furnace temperature curve is 215°C, and the temperature of the tin furnace is 245°C when the tin furnace is inspected. The RSS curve is heating→constant temperature→reflux→cooling curve; ideal cooling zone curve and reflow zone curve mirror image relationship.
Patch red glue: SMT patch red glue is a kind of polydilute compound, which is different from solder paste in that it solidifies after being heated, and its freezing point temperature is 150°C. At this time, the red glue starts to change from paste directly to into a solid. SMT patch red glue has viscosity fluidity, temperature characteristics, wetting characteristics and so on. According to this characteristic of red glue, the purpose of using red glue in production is to make the parts firmly stick to the surface of the PCB circuit board and prevent it from falling. (This process needs red glue patch welding process according to customer requirements)
Use on printing machines or dispensing machines: In order to maintain the quality of patch adhesive, please store it in the refrigerator (5±3°C); before taking it out of the refrigerator for use, it should be warmed at room temperature for 2 to 3 hours; it can be used Use toluene or ethyl acetate to clean the hose.
Dispensing and squeegee: add a back plug to the dispensing tube to obtain a more stable dispensing amount; the recommended dispensing temperature is 30-35°C; when dispensing the dispensing tube, please use a special glue dispenser for dispensing to prevent Mix air bubbles in the glue. The recommended squeegee temperature is 30-35°C. Note: After the red glue is removed from the refrigerated environment, it cannot be opened before it reaches room temperature. To avoid contaminating the original product, do not return any used adhesive to its original packaging.
SMT patch features: high mounting density, small size and light weight of electronic products, the volume and weight of patch components are only 1/10 of traditional plug-in components, and with the advancement of technology, components will become smaller and smaller, generally After adopting SMT, the volume of electronic products is greatly reduced, and the weight is reduced by more than 60% to 80%. High reliability and strong earthquake resistance. Solder joint defect rate is low. Good high frequency characteristics. Reduced electromagnetic and radio frequency interference. Easy to automate and improve production efficiency. Reduce costs by 30% to 50%. Save material, energy, equipment, manpower, time, etc.
Smaller size, faster production and reduced weight are the main attractions of SMT, which make the design and production of electronic circuits easier, especially in complex circuits. This higher level of automation saves time and resources throughout the electronics manufacturing industry. So while there are always opportunities to develop new technologies, SMT has certainly ensured its relevance.
FPC cleaning agent, cleaning agent after BGA ball planting, ball solder paste cleaning agent, FPC circuit board water-based cleaning agent, stack assembly POP chip cleaning agent, ink screen printing screen water-based cleaning full process solution, BMS new energy vehicle battery management System circuit board manufacturing process water-based cleaning solution, energy storage BMS circuit board water-based cleaning agent, PCBA post-soldering flux cleaning agent, component and substrate flux removal neutral water-based cleaning agent, power electronics flux removal water-based cleaning agent Water-based cleaning agent for power module/DCB, lead frame and discrete device flux removal, water-based cleaning agent for packaging and wafer cleaning, water-based cleaning agent for flip chip, post-soldering cleaning agent for SIP and CMOS chip packaging, SMT stencil , screen and misprinted board cleaning to remove solder paste, silver paste, red glue, SMT printing machine screen bottom wipe water-based cleaning agent, soldering fixture, reflow soldering condenser, filter, tool cleaning to remove baked aids Flux and heavy oil dirt cleaning agent, electronic component manufacturing water-based cleaning full-process solution.