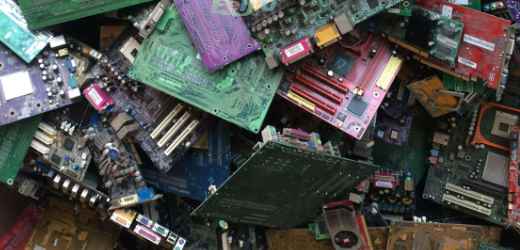
We often say that 4 layers of first-order HDI, 6 layers of second-order HDI, 8 layers of third-order HDI, so how to distinguish HDI PCB first-order and second-order and third-order
We often say that 4 layers of first-order HDI, 6 layers of second-order HDI, 8 layers of third-order HDI, so how to distinguish HDI PCB first-order and second-order and third-order
The first order is relatively simple, and the process and technology are easy to control.
Second order starts to get into trouble, one is a counterpoint problem, one is a punching and copper plating problem. There are a variety of second-order designs. One is that the staggered positions of each order are connected through wires in the middle layer when the secondary adjacent layer needs to be connected, which is equivalent to two first-order HDI. In the second, two first-order holes are overlapped, and the second order is realized by means of superposition. The processing is similar to the two first-order holes, but there are many technical points to be controlled specifically, which is mentioned above. The third is directly from the outer layer to the third layer (or N-2 layer), the process is a lot different from the previous, more difficult to punch holes.
For the third order, the second order analogy is.
The first and second order of the 6 layers are for the boards that need laser drilling, that is, HDI boards.
6-layer first-order HDI board finger blind holes :1-2,2-5,5-6, that is, 1-2,5-6 need laser drilling.
6-layer second-order HDI board finger blind hole :1-2,2-3,3-4,4-5,5-6. Two laser holes are required. First drill holes 3-4, then press 2-5, then drill laser holes 2-3,4-5 the first time, then press 1-6 the second time, then drill laser holes 1-2,5-6 the second time. It can be seen that the second-order HDI plate has been pressed and drilled twice by laser.
In addition, second-order HDI boards are divided into: second-order HDI boards with staggered holes and second-order HDI boards with overlapping holes. Second-order HDI boards with staggered holes refer to blind holes 1-2 and 2-3, while second-order HDI boards with overlapping holes refer to blind holes 1-2 and 2-3 stacked together, for example: blind :1-3,3-4,4-6.
And so on for three steps, four steps...... It's all the same.
The structure of blind buried hole HDI board is introduced
The HDI board refers to a High Density Interconnect board. This section describes several common HDI board structures.
The HDI board refers to a High Density Interconnect board. This section describes several common HDI board structures.
Our company has successfully developed 5 HDI. The HDI process is mature and the yield is more than 93%.
Three-layer mechanical blind hole structure
Opening (L2/3 or L1/2 layers), baking board, mechanical drilling of blind holes, copper sinking, full plate plating, inner graphics, plating holes, inner graphics, inner etching, inner AOI, brown, laminating, baking board, milling, degluing, drilling, normal process
Three-layer HDI structure
Opening (L2/3 or L1/2 layers), baking sheet, inner graphic, inner etching, inner AOI, Browning, laminating, baking sheet, milling, drilling, laser drilling, normal process
Four layers of mechanical blind plate
Opening (L1/2 layer and L3/4 layer), drying plate, mechanical drilling blind hole, copper sinking, full plate plating, inner graphic, plating hole plating, inner graphic, inner etching, inner AOI, brown chemical, laminating, drying plate, milling, removing glue, drilling, normal process
Four layers of mechanical blind hole plate
Opening (L2/3 layers), baking board, mechanical drilling for buried holes, copper sinking, full plate plating (negative film process, plating to the required copper thickness), inner graphics, inner etching, inner AOI, brown, laminating (pressing 3 layers of board), baking board, milling, removing glue, drilling, copper sinking, full plate plating, inner graphics, plating hole plating, inner graphics, inner etching, inner AOI, brown, laminating , drying plate, milling, removing glue, drilling, normal process
4-layer HDI board (mechanical burrow + laser drilling structure)
Opening (L2/3 layers), drying board, mechanical drilling for buried holes, copper sinking, full plate plating (negative film process, plating to required copper thickness), inner graphics, inner etching, inner AOI, brown chemical, laminating, drying board, milling, drilling, laser drilling, normal process
4-layer HDI+ mechanical blind hole plate (1+3 HDI and mechanical blind hole structure)
Opening, drying board, mechanical drilling for buried holes, copper sinking, full plate plating (negative film process, plating to the required copper thickness), inner graphics, inner etching, inner AOI, brown, laminating, drying board, milling edge, drilling (L2-4 layers), copper sinking, full plate plating, inner graphics, plating hole plating, inner graphics, inner etching, inner AOI, brown, laminating, drying board, milling edge, drilling, Laser drilling (L1-2 and L3-4), normal process
6 layers mechanical blind burials (2+2+2 mechanical blind burials)