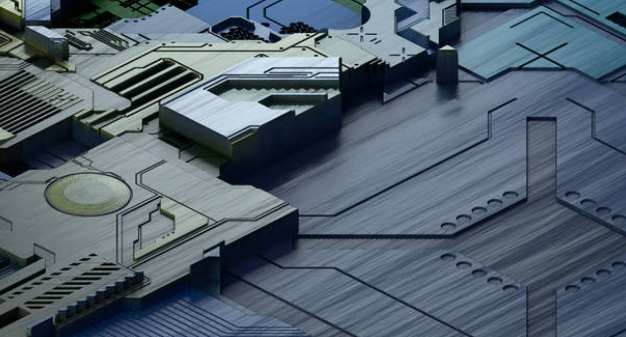
Paying attention to these requirements in PCB layout can avoid a lot of unnecessary trouble.
1. Minimum LAYOUT spacing of SMD components. When SMD LAYOUT is used to ensure a certain distance between components, the probability of virtual welding, bridge and shadow effect can be reduced.
2. SMD PCB two panel edge calculated from 3mm, should not LAYOUT SMD components. This is mainly because the guide groove of the SMT machine requires that no components are allowed within 3 ~ 5mm of the PCB board edge. 3mm is the minimum requirement. If you cannot guarantee this size, you can consider using V-shaped slots or stamp holes to extend the board. After welding, you can skim off the excess board.
3. Alignment of SMDS.
(a) Identical components, arranged in the same direction as far as possible.
(b) A test point of 30mil in diameter must be left on the same gold track.
4. When SMD and PTH devices are mixed and welded by wave crest welding,
(a) The orientation of CHIP, SOT and SOIC components should be perpendicular to the passing direction to avoid shadow effect.
(b) Components that differ too much in body height should not be arranged close together to avoid shadow effects.
(c) Any element should preferably be arranged in parallel and perpendicular to the direction of passing tin.
The shadow effect is a consideration of PCB layout when soldering SMD components by wave soldering, but it is not a problem when reflow soldering is used. The so-called shadow effect, for example, when two SMDS with very different components are close together, if the taller component passes through tin first, it may be because of the resistance of the taller component that the lower component passes through tin later, which is the shadow effect of the taller component.
(d) Adequate tin eating space shall be reserved when right-angled (vertical) alignment is required, and the space distance shall be 0.635mm.
5. Solder dead Angle caused by SMT LAYOUT (air welding)
The following diagram shows the possible conditions for air welding. Specific LAYOUT, need to consider whether the layout in welding may cause air welding, in a word, need flexible application, can not be copied.
6. V-CUT reference data
(1) FR-2, CME-1, OAK910 (semi-glass fiber) PCB thickness 1.6mmV-CUT The depth of the cutter is 0.4mm×2 sides.
FR-4 PCB thickness 1.6mm V-CUT cutter depth 0.5mm x 2 sides.
We always insist on delivering the most suitable technical requirements and the most cost-effective products to our customers
---- Shenzhen Princetum Corporation
This section describes the problems that should be paid attention to during PCB board etching
A large number of quality problems related to etched surfaces are concentrated on the etched part of the upper plate surface, and these problems come from the effect of the adhesive plate produced by the etching agent. It is important to know this because colloidal slabs accumulate on copper surfaces. On the one hand, the injection force will be affected, and on the other hand, the refill of fresh etching liquid will be blocked, so that the etching speed will be reduced. Because of the formation and accumulation of colloid-like plates, the etching degree of the upper and lower surfaces of the substrate is different. Because the accumulation has not yet formed, the etching speed is faster, so it is easy to be completely etched or overcorroded. The accumulation of the later substrate slows down the etching speed.
PCB board etching process should pay attention to what problems
Maintenance of etching equipment
The most critical factor in maintaining etching equipment is to ensure the high cleanliness of the nozzle and no obstruction, so that the nozzle can spray smoothly. Blockages or slagging can cause pressure to impact the surface when spraying. The nozzle is not clean, it will cause uneven etching and make the whole circuit board scrapped.
Obviously, the maintenance of equipment is to replace damaged parts and worn parts, because the nozzle also has the problem of wear, so the replacement should include the nozzle. In addition, the more critical problem is to keep the etching machine without slagging, because in many cases too much slagging accumulation will affect the chemical balance of the etching fluid. Similarly, if there is a chemical imbalance in the etching solution, the slagging will become more serious. When a large amount of slagging occurs suddenly in the etching solution, it is usually a signal that there is a problem in the balance of the solution. At this time, strong hydrochloric acid should be used for appropriate cleaning or replenishing of the solution.
Problems to be paid attention to in etching process
Reduce side erosion and edge, improve the etching coefficient
Lateral erosion will produce a sharp edge. Usually, the longer the printed board in the etching solution, the more serious the situation of side erosion. Side erosion will seriously affect the precision of printed wire. Serious side erosion will make it impossible to make fine wire. When the side erosion and the edge decrease, the etching coefficient will increase. A high etching coefficient indicates the ability to maintain a thin wire, so that the etched wire can be close to the original size. Whether it is tin - lead alloy, tin, tin - nickel alloy or nickel plating etching agent, excessive edge will cause wire short circuit. Because the edge tends to tear off, an electrical splice is formed between the two points of the wire.
There are many factors affecting lateral erosion, some of which are summarized below:
1. Etching method:
Soaking and bubbling etching will cause large side erosion, splash and spray etching side erosion is small, especially spray etching effect is the best.
2. Types of etching fluid:
Different etching fluid, its chemical composition is different, the etching rate is not the same, the etching coefficient is not the same.
For example, the etching coefficient of acidic copper chloride etching solution is usually 3, while the etching coefficient of alkaline copper chloride can reach 4.
3. Etching rate:
Slow etching can cause serious side erosion. There is a great relationship between improving the etching quality and accelerating the etching rate. The faster the etching speed, the shorter the stay time of the substrate in etching, the smaller the amount of side etching, and the more clear and tidy the etched pattern.
4. PH value of etching fluid:
When the PH value of alkaline etching solution is higher, the lateral erosion will increase. In order to reduce lateral erosion, the PH value should generally be controlled below 8.5.
Density of etching solution:
Too low density of alkaline etching solution will aggravate side erosion, choosing etching solution with high copper concentration is very beneficial to reduce side erosion.
To achieve minimal lateral etching of fine wire, it is best to use (ultra) thin copper foil. And the thinner the wire width, the thinner the copper foil thickness should be. Because the thinner the copper foil, the shorter the time in the etching solution, the smaller the amount of side erosion.