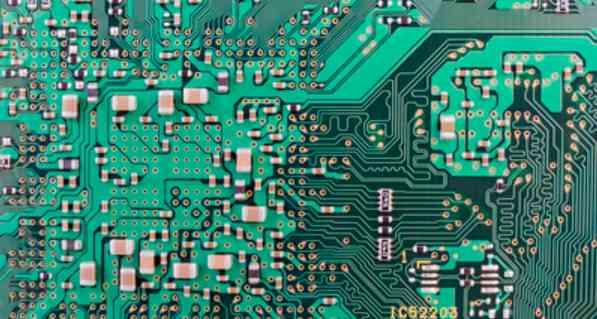
I. Preface
Copper hole is a functional problem of pcb. With the development of science and technology, PCB precision (aspect ratio) requirements are becoming higher and higher. It not only brings trouble to PCB makers (contradiction between cost and quality), but also lays a serious quality hazard for downstream customers! Following this simple analysis, I hope to be able to enlighten and help relevant colleagues!
Ii. Classification and characteristics of pore without copper
1. No copper in the PTH hole: the electrical layer of the surface copper plate is uniform and normal, and the electrical layer of the plate in the hole is evenly distributed from the orifice to the fracture, and the fracture is covered by the electrical layer after electrogram.
2. Plate electric copper thin hole without copper:
(1) the whole plate plate copper thin hole without copper -- surface copper and hole copper plate electrical layer is very thin, after electroelectropretreatment of micro corrosion hole after most of the plate copper is eroded, electroelectrogram is covered by electroelectrogram layer;
(2) The electric copper in the hole plate thin hole without copper -- the electrical layer of the copper plate is uniform and normal, the electrical layer of the hole plate shows a decreasing trend from the hole to the fracture, and the fracture is generally in the middle of the hole, the copper layer at the fracture left
The right side has good uniformity and symmetry, and the fracture is enclosed by the electrograph layer.
3. Repair holes:
(1) Copper repair bad hole -- table copper plate electrical layer uniform normal, hole copper plate electrical layer without the trend of pulling tip, irregular fracture, may appear in the hole may also appear in the middle of the hole, in the hole wall often appear rough convex and other bad, the fracture is covered by the electrogram layer.
(2) corrosion maintenance of the hole - surface copper plate electrical layer is uniform and normal, hole copper plate electrical layer without the trend of pulling tip, irregular fracture, may appear in the hole may also appear in the middle of the hole, in the hole wall often appear rough convex and other bad, the electrical layer at the fracture did not cover the plate electrical layer.
4. No copper in the plug hole: after electrographic etching, there are obvious substances stuck in the hole, most of the hole wall is eroded, and the electrographic layer is not covered by the electrical layer of the plate at the fracture.
5. No copper in the electrical hole: the electrical layer at the fracture is not covered by the electrical layer of the plate -- the thickness of the electrical layer and the electrical layer of the plate is uniform, and the fracture is broken together; The electrographic layer tends to peak until it disappears, and the plate electrographic layer continues to extend some distance beyond the electrographic layer and then disconnects.
Iii. Direction of Improvement:
1. Operation (upper and lower plates, parameter setting, maintenance, abnormal handling);
2. Equipment (crane, feeder, heating pen, vibration, pump, filter cycle);
3. Materials (plate, potion);
4. Methods (parameters, procedures, processes and quality control);
5. Environment (variation caused by dirty, messy and miscellaneous).
6. Measurement (potion test, copper visual inspection).
7, more sensitive to the temperature of the device is best placed in the lowest temperature area (such as the bottom of the equipment), do not put it above the heating device, multiple devices are best in the horizontal staggered layout.
8, the heat dissipation of the printed board in the equipment mainly depends on the air flow, so in the design to study the air flow path, reasonable configuration of devices or printed circuit boards. Air flow always tends to flow where the resistance is low, so when configuring components on the printed circuit board, avoid leaving a large area of airspace. The configuration of multiple printed circuit boards in the whole machine should also pay attention to the same problem.
9. Avoid the concentration of hot spots on the PCB, distribute the power evenly on the PCB board as far as possible, and maintain the uniform and consistent temperature performance of the PCB surface. Often in the design process to achieve strict uniform distribution is more difficult, but we must avoid the power density is too high in the area, so as to avoid the occurrence of hot spots affect the normal operation of the entire circuit. If conditions are available, it is necessary to carry out thermal performance analysis of printed circuits. For example, the thermal performance index analysis software module added in some professional PCB design software can help designers optimize circuit design.
10. Arrange the devices with the highest power consumption and maximum heat dissipation near the optimal location for heat dissipation. Do not place hot components at the corners and edges of the printed board unless a cooling device is arranged near it. Choose as large a component as possible when designing the power resistance, and adjust the layout of the printed board to allow enough space for heat dissipation.
11, high heat dissipation devices in connection with the substrate should be able to reduce the thermal resistance between them. To better meet the requirements of thermal characteristics, use some thermal conductive materials (such as a layer of heat-conducting silicone) on the bottom surface of the chip, and keep a certain contact area for heat dissipation.
12, device and substrate connection:
(1) Shorten the lead length of the device as far as possible;
(2) When choosing high-power devices, the thermal conductivity of the lead material should be considered. If possible, try to choose the maximum lead transverse surface;
(3) Select devices with more pins.
13. Package selection of devices:
(1) When considering thermal design, attention should be paid to the package description of the device and its thermal conductivity;
(2) Consideration should be given to providing a good heat conduction path between the substrate and the device package;
(3) In the heat conduction path should avoid air partition, if there is such a case can be filled with thermal conductive materials.
Tags: PCB circuit board cooling tips