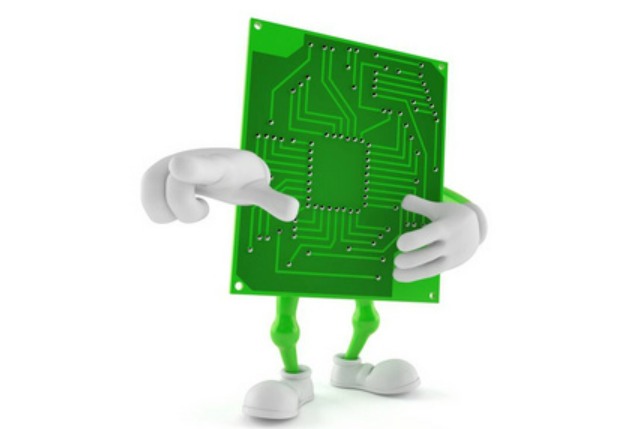
There is a limit to how many circuits you can fit on a board. PCBS themselves have a size upper limit for manufacturing equipment and standard panel size reasons. The number of transistors on a device continues to expand, while resistors and capacitors almost disappear to the naked eye. Even with all the integration and miniaturization, the complexity of circuits grows to an unmanageable scale. A PCB is not going to cut it.
Extensions beyond a single PCB come in many forms. Telecommunications and other networking equipment are often found in rack systems. The familiar 19 "wide x 1.75" high rack unit is the default housing size for smaller circuits. This is what you see when you read the term server farm or data center. From there, the reference line extends to multiple rack units. Although they come in a variety of sizes, the popular ones are seven-stand shelves. It's still 19 inches wide, but it takes up just over a foot of rack space. The shelf is fitted with a vertically placed PCB and is connected using a 19 "x 12" backboard which is mounted on the back of the shelf.
Backplanes are usually just connectors and wiring. The number of layers may be high to support a large number of connections. The thickness of this plate provides the stiffness required to engage the 640-pin connector while resisting anyone attempting to preheat the bottom plate before welding. Therefore, pressure fit connectors are standard on these types of printed circuit boards.
Treated plate
In addition to connectors, we usually need some sort of housekeeping circuit. These components will need to be surface-mounted, especially if the backplane is on the thicker side. The standard pins on the through-hole parts do not reach the required length for the far end of the backplane, so they are not weldable or reworkable. Then the aforementioned pound of copper for the ground plane to raise the reflux temperature. It's not pretty.
Another consideration related to board thickness is the through hole in the z-axis. If wiring is to be done from the top to the fourth layer of the 24-layer board, the other 20 layers will form the hanging line. This discontinuity can be eliminated if we return after all plating is done and drill a new slightly larger hole where the 20 short piles are. Reverse drilling requires additional effort, but the results of the signal integrity ophthalmogram can be measured.
This brings us into all the other PCBS in the system. In the data center, server blades will occupy most of the slots, so you can expect some uniformity. The system is scalable and each new board improves overall performance.
Other network devices may be more diverse. Each card slot serves a different purpose, and each card slot must be filled for the entire group to work properly. Because of all the large parts and the extreme voltage swings that come with them, the power supply is usually a separate board. The most power-hungry cards find a spot next to a power source, while the most sensitive victims hide in their own little boxes away from heat and noise. Think of all the gadgets that flow down from wall warts. The power supply is placed into the electrical outlet and the juice is fed to the rest of the system via ferrite beads and/or shielded wires. Same principle.
Good neighbor policy
Subdividing the rest of the schematic into circuit boards is usually based on block diagrams. How these modules are combined should depend on the technology involved. Some circuits will require higher layers or aggressive HDI techniques. Others can live with vanilla-flavored four-ply boards. Fine-tuning in terms of functionality and technology depends on power range, co-storage, heat path, weight distribution, and ultimately aesthetics. I remember a board in a system called a "tROtS board". It stands for "rest of the story." Sometimes, another word takes the place of "story."
Not all systems need 7-foot-tall racks of electronics to qualify. Just a few PCIe or SATA connectors. The example that comes to mind is a prototype version of Google's "Home" mesh router. Use another Qualcomm chipset, which is larger in size. Three additional PCIe card slots enable it to test the functionality of multiple router configurations. The air interface is another thing. The only real way to test the wireless portion of a link is to set up a test chamber. We enabled baseband level testing in the lab using a four-board system. Prototypes are one of those 20% of the time cool things you've ever heard of.
These micro-systems may give you more freedom. Typically, the backboard is more of a motherboard carrying some computing load. In this case, the suspect you normally need must be present at the meeting. Memory and various drivers may find a home next to the microprocessor. Of course, the memory usually resides on the SIM module, which boils down to a circuit board with connectors and a line of memory chips. In this regard, you can think of it as another board in the system. Any indicators, buttons, displays, or other controls that have been used in the product will eventually appear on this layout. Then, when we want to add more functionality, the plug-in acts as an expansion slot. That's the model we used for the Google Home test car.
This type of healthy multi-board system will require some degree of standardization. In particular, the child card will want to adhere to the protocol, perhaps even off-the-shelf child components. In this case, the content of the line card (or any other content) is predetermined.
As the world moves toward 5G mesh networks, subsystems will have to have cellular level replaceable and upgradeable equipment, as well as some serious bandwidth for substations. Radios must be cheap, durable and ubiquitous. Centralized blocks will require unlimited throughput to ensure bulletproof reliability. All of this data will not be aggregated on a single board. The big web is coming. Be prepared.