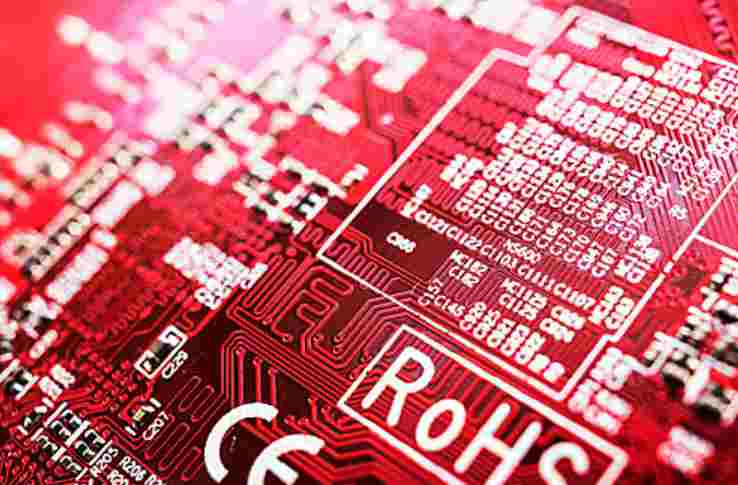
Anyone who has participated in ERP project implementation should know that the success of ERP project implementation lies in the details. Some people say that ERP is not difficult, just complicated. The complexity mentioned here refers to the process of sorting out ERP basic data. Sorting out ERP basic data is indeed very tedious, this process is not easier than ERP online, but it is not difficult, as long as insist, will be able to achieve. ERP project implementation success depends on three points of technology, seven points of management, twelve points of data. Visible, ERP system in the importance of basic data collation.
There are three data sources in ERP system, which are engineering data source, inventory data source and other parameter Settings. Among them, engineering data sources and inventory data sources account for 90% of the database of the whole ERP system. They are also the most difficult to sort out and have the longest sorting cycle, which requires more energy to deal with and must be completed in the early preparation of project implementation. The parameter setting is a gradual process, including the daily maintenance of the system after the successful implementation of the project.
Engineering data sources mainly include the establishment of scientific coding system, the establishment of material master file (ITMB), the collection and arrangement of BOM (Bill of materials), the determination of product process route, etc. In view of the large workload of the establishment of the engineering database and the long-term work, it must be completed with organizational guarantee, and the collation and entry of engineering data involves many business departments, so it is necessary to set up an engineering data team composed of business personnel from several departments. The team is generally led directly by the ERP project leader and requires members of the enterprise standardization team and information department to join.
The main responsibility of the data team is to establish and maintain the coding system of ERP system, sort out and standardize the engineering data of the enterprise, and ensure the standardization and accuracy of the engineering data of the enterprise. The establishment of a scientific coding system involves a lot of departments, because a complete coding system includes material coding, supplier coding, customer coding, warehouse coding, planner/buyer coding, etc. Among them, the workload of material coding is the largest. The finished products at different levels between different processes should have their own coding, including raw materials, purchased parts, blanks, parts, components, products, etc. The coding system must be completed before the BOM data collation, and then it is required to go deep into the design department. On the one hand, the material referenced by the design drawing should be coded, which is easy to import into the ERP system through the interface program. On the other hand, during product design, materials codes in ERP system can be directly queried and referenced by relevant query tools of ERP system, so as to facilitate the promotion and application of materials codes and check the accuracy of codes in application.
In the process of material coding, it is necessary to avoid the situation of "repeated coding" and "multiple codes of one thing", if any, it should be corrected in time. With the development of digitization, material coding should not be given too much meaning. At present, most of the material coding is "pure digital coding", the simpler the better. From the broad category can distinguish, such as "0" the beginning of the finished product, "1" the beginning of the hardware, "2" the beginning of the plastic parts, "3" the beginning of the paint class. Material coding must be scalable and extensible to facilitate the future development of the enterprise.
Product BOM structure, in fact, exists in any manufacturing enterprise, even without ERP system, the research and development department should also have a set of relevant product BOM, but it is not standardized. The key to BOM data collection is to collect the ready-made BOM and modify it, including format modification, error correction, and material code matching, etc. When sorting out BOM, material description must be standardized and reasonable, try to adopt some international and domestic standardized description, BOM structure level must be clear, those are the parent items, those are children, those are virtual items, those are byproducts. What kind of work center should be set up, and the capacity setting of the related work center, etc. After a set of BOM forms is completed, a strict audit mechanism should be established to carefully check and audit the BOM forms to ensure their accuracy.
BOM entry system has a lot of work, a set of good ERP products, should have the function of importing BOM in batches directly, which can bring great convenience to BOM entry system. The material code can also be directly imported into the system in batches. The material code imported into the system is not a simple code, but also includes the corresponding material description, classification, unit of measurement, purchase code and so on, which forms the so-called material master file (ITMB). In general ERP system, each material data provides a lot of descriptive parameters about the material. Users do not have to set each parameter, but only those parameters that are necessary for system operation and useful for material management. When material data is set, the contents of some fields must be defined and then selected by the user. Other fields can be selected from the options provided by the system. For fields without optional values, users can enter the actual values when creating material records.