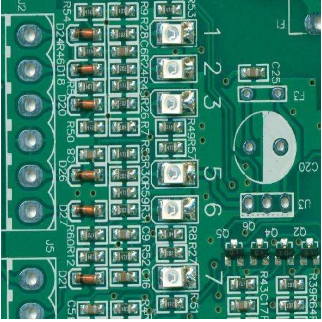
In SMT production, we call paster, solder paste and stencil as auxiliary materials, but its importance cannot be ignored. Template is the first link of the whole process, and its quality directly affects the printing quality. According to statistics, in the SMT process, more than 60% of SMT defects are caused by printing, of which 35% are caused by defective templates. In addition, 60% of assembly defects and 87% of reflow welding defects are also caused by defective templates. Therefore, the template plays a crucial role in the quality and production efficiency of SMT, and selecting a high-quality template can improve the quality of SMT process.
The factors affecting the quality of formwork are mainly reflected in three aspects. First, the quality of materials, that is, the quality, hardness and elasticity of the steel sheet itself. Secondly, the design of formwork includes the selection of steel sheet thickness, opening size and opening shape of holes. The thickness and opening size determine the coating amount and accuracy of PCB solder paste, which is a very important link in the entire production process. The opening shape has an impact on the quality of tin applied. The third is the manufacturing method of the template, including dimensional accuracy, trimming flatness, roughness and shape of the opening hole wall. Dimensional accuracy is the basic requirement for use, and the roughness and shape of the opening hole wall determine the tin coating quality. The first two factors are stable after the steel sheet is selected and the PCB design is completed, but the manufacturing method of the template is variable, which is the biggest factor affecting the quality of the template.
At present, there are three manufacturing methods of templates, namely chemical etching, laser cutting and electroforming. Each of the three methods has its advantages and disadvantages. By comparing the production process, template quality and other aspects, the laser template is usually used, which has the following advantages,
Good quality: non-contact processing, no stress, no deformation, and even tension distribution after wire tensioning.
By adjusting the laser focusing position, the opening automatically forms a cone, which is conducive to solder paste demoulding.
The cutting edge is smooth, which is comparable to the electroforming template.
Fast speed: fewer production processes, simple operation, fast production speed, and short delivery date.
Low cost: there are fewer processes, so there are fewer consumables, and the reuse rate of formwork is high, reaching more than 300000 times.
Realize automatic control of the machine, easy to operate and save human resources.
High precision: directly use design documents without photography steps, eliminating the factors of incorrect position.
The size accuracy of the hole is small and the position accuracy is high, which is very suitable for high-density design.
Strong function: the only process to rework the existing template, such as hole adding, hole patching and hole enlarging.
No pollution: there is no chemical solution in the production process, no pollution to the environment, and no harm to the health of operators.
Based on the importance of the template to the SMT process and the advantages of the laser template, we will make a deep and detailed discussion on the cutting quality of the SMT laser template, which has a positive and important significance for the improvement of the process and overcoming some problems in the actual PCB application.
1. SMT laser template cutting
After focusing, the laser shines on the material, and the light energy is converted into heat energy, which makes the temperature of the cut material rise rapidly, and then melts or vaporizes it. At the same time, the airflow coaxial with the beam is ejected from the nozzle to cut the melted or vaporized PCB material