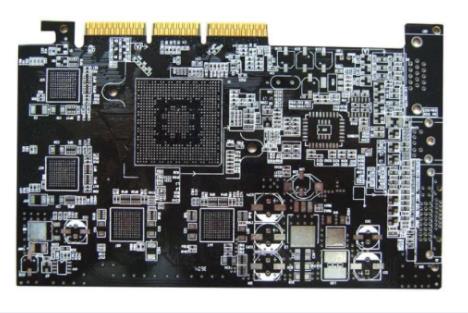
PCB short circuit idea
Content overview: The concentration of the film remover is high, the film remover takes a long time, and the anti coating film has fallen off, but the board is still immersed in strong alkaline solution. Part of the tin powder adheres to the surface of the copper foil. When the copper foil is etched, there is a thin metal tin protective layer, which plays an anti-corrosion role, causing the copper to be removed but not cleaned, resulting in a short circuit. In this regard, we need to strictly control the concentration, temperature and time of the membrane removal solution. At the same time, insert the film using a plug-in bracket when removing the film. The plates cannot be stacked together.
PCB running tin
1. Short circuit PCBrunning tin caused by fault:
1. Improper operation of the membrane stripping solution tank leads to tin run out; 2 The stacking of the film stripping plates leads to tin flow
Improvement method: Therefore, we need to strictly control the concentration, temperature and membrane removal time At the same time, insert the film with a plug-in bracket when removing the film The plates cannot be stacked together
(2) The striped plates are stacked together before being dried, so that the tin between the plates is immersed in the unbaked stripping solution, and part of the tin layer will be dissolved and attached to the copper foil surface The thin metal tin layer protects the copper surface and plays a role in corrosion prevention, which causes the copper to be removed without being cleaned, resulting in a short circuit
2. Short circuit PCB etching caused by defects:
1. The quality of etching agent parameter control directly affects the etching quality At present, our company uses alkaline etching solution The specific analysis is as follows: 1.1 PH value: controlled at 8.3 and 8.8. If the pH value is low, will the solution become viscous? The color is white, and the corrosion rate decreases This condition may cause side corrosion PH value is mainly controlled by adding ammonia 1.2 Chloride ion: controlled between 190~210g/L The content of chloride ion is mainly controlled by etching salt and consists of ammonium chloride and supplement 1.3 Specific gravity: The specific gravity is mainly controlled by controlling the content of copper ions Generally, the copper ion content shall be controlled between 145 and 155g/L, and the test shall be conducted every hour or so to ensure the stability of specific gravity 1.4 Temperature: controlled at 48~52 ℃ If the temperature is high, ammonia volatilizes quickly, which will lead to unstable pH value. The cylinder of the etcher is mostly made of PVC materials, and the temperature resistance limit of PVC is 55 ℃ Exceeding this temperature may easily lead to cylinder deformation, or even the scrapping of the etcher Therefore, an automatic thermostat must be installed to effectively monitor the temperature and ensure that it is within the control range 1.5 Speed: generally adjust the appropriate speed according to the thickness of the copper at the bottom of the plate Suggestion: In order to achieve the stability and balance of the above parameters, it is recommended to include an automatic feeder to control the chemical composition of the sub solution, so that the composition of the etching solution is in a relatively stable state 2. When the whole plate is plated with copper, the thickness of the electroplated coating is uneven, resulting in unclean etching Improvement method: (1) Try to realize automatic line production when electroplating the whole plate. At the same time, adjust the current density per unit area (1.5~2.0A/dm2) according to the size of the hole area, and keep the electroplating time as consistent as possible. Flybus ensures full load production. At the same time, add cathode and anode baffles, and formulate the use system of "electroplating edge strip" to reduce potential difference (2) If the full plate electroplating is manual line production
3. PCB visible short circuit:
1. Micro short circuit caused by scratches on the polyester film on the exposure machine; 2 Micro short circuit caused by scratch of exposure plate glass Improvement methods: (1) The Mylar film on the exposure machine has been used for a long time Scratches accumulate dust and form black or opaque "small lines" When the circuit pattern is exposed, it is black or opaque The "small lines" that block the light will form copper spots between the developed lines and cause short circuits The thinner the copper foil on the circuit board, the easier the short circuit is. The smaller the line spacing, the easier the short circuit is So when we find that the polyester film is scratched, we must immediately replace it or clean it with absolute alcohol to ensure the transparency of the polyester film and strictly control the existence of opaque scratches (2) The exposure plate glass on the exposure machine has been used for a long time Scratches accumulate dust, forming black marks or opaque "small lines" When the circuit pattern is exposed, the same is true for opaque "small wires" Coloring, forming copper dots between lines after development, resulting in short circuit Therefore, when we find glass scratches, we must immediately replace them or clean them with an anhydrous sprinkler, and strictly control the existence of opaque scratches
4、 Short circuit of the film:
1. The protective coating is too thin In the electroplating process, when the coating exceeds the film thickness, a film is formed, especially when the line spacing is smaller, the film is more likely to be short circuited 2. The pattern of the circuit board is unevenly distributed During the pattern electroplating of several isolation lines, due to the high potential, the coating exceeded the film thickness, forming a 3-Meiji film and causing a short circuit Improvement methods: (1) Increase the thickness of the anti-plating layer: choose a dry film with a suitable thickness. If the film is wet, low mesh screen printing can be used, or the film thickness can be increased by printing the wet film twice (2) The plate pattern is not uniformly distributed, and the current density (1.0~1.5A) can be appropriately reduced for electroplating. In daily production, we want to ensure the output. In retrospect, we usually control the electroplating time to be as short as possible. In retrospect, the current density used is usually between 1. 7 and 2.4 A. In this case, the current density obtained in the isolation area is 1.5 to 3. 0 times of the normal area, which usually results in the coating height of the small spacing isolation area greatly exceeding the film thickness This will cause a short circuit in the film and a thinner solder mask on the circuit
The above is the explanation given by the editor of pcb circuit board company.
If you want to know more about PCBA, you can go to our company's home page to learn about it.
In addition, our company also sells various circuit boards,
High frequency circuit board and SMT chip are waiting for your presence again.