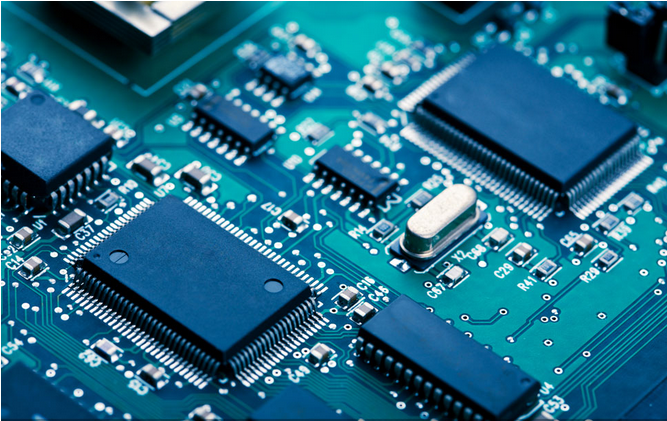
PCB manufacturer explains the first half of PCB maintenance skills
1、 Fault Characteristics and Maintenance of Capacitance Damage of Industrial Control Circuit Board
The failure caused by capacitor damage is the highest in electronic equipment, especially the damage of electrolytic capacitor.
The capacitance is damaged as follows: 1. The capacity becomes smaller; 2. Total loss of capacity; 3. Electric leakage; 4. Short circuit.
Capacitors play different roles in the circuit, and the faults caused by them have their own characteristics. In the industrial control circuit board, digital circuits account for the vast majority. Capacitors are mostly used as power filter, and less capacitors are used as signal coupling and oscillation circuits. If the electrolytic capacitor used in the switching power supply is damaged, the switching power supply may not vibrate and have no voltage output; Or the output voltage filtering is not good, and the circuit logic is confused due to unstable voltage, which means that the machine is good or bad or cannot be started when it is working. If the capacitor is between the positive and negative poles of the power supply of the digital circuit, the fault performance is the same as above. This is particularly evident on the computer motherboard. Many computers can not be started or can be started after several years of use. When the chassis is opened, the phenomenon of electrolytic capacitor bulging can often be seen. If the capacitor is removed to measure the capacity, it is found that it is much lower than the actual value.
The life of capacitor is directly related to the ambient temperature. The higher the ambient temperature is, the shorter the life of capacitor is. This rule applies not only to electrolytic capacitors, but also to other capacitors. Therefore, when looking for fault capacitors, we should focus on the capacitors close to the heat source, such as those near the radiator and high-power components. The closer they are, the more likely they are to be damaged. The user once repaired the power supply of an X-ray flaw detector. The user reported that smoke came out of the power supply. After removing the chassis, he found that a 1000uF/350V large capacitor had oil like flow out. The removed capacity was only dozens of uF. He also found that only this capacitor was closest to the radiator of the rectifier bridge, and the other capacitors far away were intact and normal in capacity. In addition, there is a short circuit in the ceramic capacitor, and it is also found that the capacitor is close to the heating component. Therefore, emphasis should be placed on maintenance and search.
Some capacitors have serious electric leakage, which can even be hot when touched by fingers. Such capacitors must be replaced.
In the maintenance of good and bad faults, except for the possibility of poor contact, most faults are caused by capacitor damage. Therefore, when encountering such faults, we can focus on checking the capacitor. It is often surprising to replace the capacitor (of course, we should also pay attention to the quality of the capacitor, and choose a better brand, such as Ruby, Black Diamond, etc.).
2、 Characteristics and discrimination of resistance damage
It is often seen that many beginners toss and turn on the resistance when repairing the circuit, which is both disassembled and welded. In fact, it is much more repaired. As long as you understand the damage characteristics of the resistance, you don't need to spend much time.
Resistance is the most numerous component in electrical equipment, but it is not the component with the highest damage rate. Open circuit is the most common resistance damage. It is rare for the resistance value to become larger, and it is rare for the resistance value to become smaller. Common types include carbon film resistor, metal film resistor, wire wound resistor and fuse resistor. The first two types of resistors are the most widely used, and their damage characteristics are: first, the damage rate of low resistance (below 100 Ω) and high resistance (above 100k Ω) is high, and the damage rate of intermediate resistance (such as hundreds of ohms to tens of kiloohms) is rare; Second, when the low resistance resistance is damaged, it is often burnt and blackened, which is easy to find, while when the high resistance resistance is damaged, there is little trace. Wire wound resistance is generally used for large current limiting, and the resistance value is not large. When the cylindrical wire wound resistance is burnt out, some will be blackened, or the surface will be cracked, and some will have no trace. Cement resistance is a kind of wire wound resistance, which may break when burned out, otherwise there is no visible trace. When the fuse resistor is burnt out, some surfaces will blow off a piece of skin, and some have no traces, but they will never be burnt and blackened. According to the above characteristics, we can focus on checking the resistance and quickly find out the damaged resistance.
According to the characteristics listed above, we can first observe whether the low resistance resistance on the circuit board has any signs of burning black. Then, according to the characteristics of most open circuits or large resistance values when the resistance is damaged and the high resistance resistance is easy to be damaged, we can use a multimeter to directly measure the resistance at both ends of the high resistance resistance on the circuit board. If the measured resistance value is larger than the nominal resistance value, The resistance must be damaged (it should be noted that the conclusion can be made only after the resistance value is stable, because there may be a charging and discharging process for parallel capacitor elements in the circuit). If the measured resistance value is smaller than the nominal resistance value, it is generally ignored. In this way, each resistance on the circuit board is measured once. Even if you "kill" 1000 by mistake, you will not miss one.
3、 A Method for Judging Operational Amplifiers
It is difficult for quite a number of electronic maintainers to judge whether the operational amplifier is good or not, not only because of their educational level (there are many undergraduates under my command, if they don't teach, they will certainly not, and it will take a long time to understand after teaching, and there is also a graduate student who specializes in frequency conversion control with his tutor, which is also true!), I would like to discuss with you here and hope it will be helpful to you.
The ideal operational amplifier has the characteristics of "virtual short" and "virtual break", which are very useful for analyzing the operational amplifier circuit of linear application. In order to ensure the linear application, the operational amplifier must work in a closed loop (negative feedback). If there is no negative feedback, the op amp under open-loop amplification becomes a comparator. If you want to judge whether the device is good or bad, you should first distinguish whether the device is used as an amplifier or a comparator in the circuit.
No matter what type of amplifier, there is a feedback resistance Rf, so we can check the feedback resistance from the circuit during maintenance, and use a multimeter to check the resistance between the output end and the reverse input end. If the deviation is large, such as several M Ω or more, we can probably be sure that the device is used as a comparator. If the resistance is smaller than 0 Ω to tens of k Ω, then check whether the resistance is connected between the output end and the reverse input end, If any, it must be used as an amplifier.
According to the principle of virtual short of the amplifier, if the operational amplifier works normally, the voltages at the same direction input end and the reverse input end must be equal, even if there is a difference, it is mv level. Of course, in some high input impedance circuits, the internal resistance of the multimeter will have some influence on the voltage test, but generally it will not exceed 0.2V. If there is a difference of more than 0.5V, the amplifier will definitely be damaged! (I use FLUKE179 multimeter)
If the device is used as a comparator, the same direction input terminal and reverse input terminal are allowed to be different. If the same direction voltage is greater than the reverse voltage, the output voltage is close to the maximum positive value; If the voltage in the same direction is less than the reverse voltage, the output voltage is close to the maximum value of 0V or negative (depending on dual power supply or single power supply). If the detected voltage does not conform to this rule, the device will be damaged! In this way, you do not need to use the substitution method, and you do not need to remove the chip on the circuit board to judge the quality of the operational amplifier.
4、 A Trick to Test SMT Components with Multimeter
Some SMD components are very small, which makes it inconvenient to test and repair with an ordinary multimeter probe. First, it is easy to cause short circuit. Second, it is inconvenient for the circuit board coated with insulating coating to contact the metal part of the component pin. Here is a simple method, which will bring a lot of convenience to the detection.
Take two sewing needles of the smallest size, (deep industrial control maintenance technology column) and close them to the multimeter probe, then take a thin copper wire in a multi strand cable, use the thin copper wire to bind the probe and the sewing needle together, and then solder them firmly. In this way, when measuring SMT components with a stylus with a small tip, there is no risk of short circuit. In addition, the tip can puncture the insulation coating, directly hit key parts, and no longer bother to scratch the film.
PCB manufacturers, PCB designers, and PCBA manufacturers will explain the first half of PCB maintenance techniques to you.