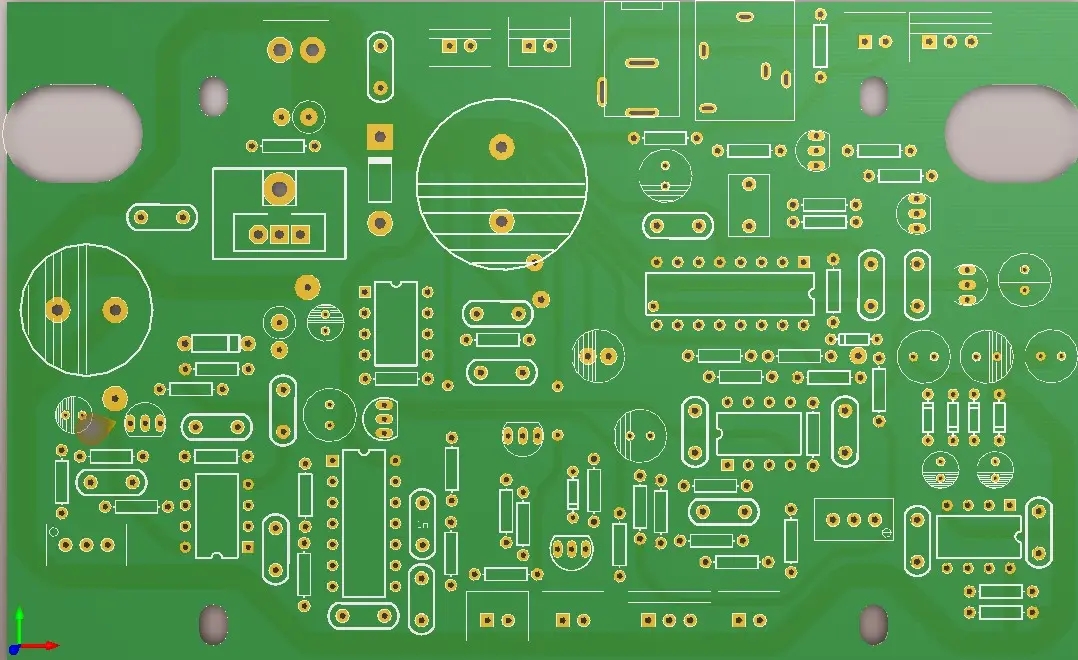
Sorting out the influencing factors of steel mesh
The circuit board manufacturer and circuit board designer explain the factors affecting the steel mesh
PCBA processing is to connect various electronic components on PCB board through surface mount (SMT), plug-in (DIP) and other electronic assemblies. PCBA process flow mainly includes SMT, AOI, DIP, FCT testing and other processes. Due to the size difference of electronic components, there will be different processes and requirements in assembly and insertion. The assembly density of PCBA is relatively high, and the small size and light weight of electronic products also have certain changes and requirements in mounting. The reliability, seismic resistance and excellent weldability of the products have high requirements for the hardware and software facilities of PCBA processing.
According to the introduction of the director of the PCB factory of PCB Electronics Co., Ltd., the editor learned that the following factors will affect the quality of the steel mesh:
1. Manufacturing process
The previous article has a brief analysis of the production process of the steel mesh. Through this article, we know that the best process should be electropolishing after laser cutting. Both chemical etching and electroforming have processes that are prone to errors such as film, exposure and development, and electroforming is also affected by uneven substrate.
2. Selection of materials
Materials required for steel mesh manufacturing include mesh frame, wire mesh, steel sheet, adhesive, etc. The mesh frame must be able to withstand the relay of certain procedures and have good levelness; Polyester mesh is best used for wire mesh, because it can keep tension stable for a long time; The steel sheet should preferably be 304, and the matte one is more conducive to solder paste rolling than the mirror one.
3. Design of openings
This point has been emphasized by the factory director that the quality of the steel mesh is most affected by the quality of the steel mesh opening design. The opening design must take into account the manufacturing process, width thickness ratio, area ratio, experience value, etc.
4. Completeness of production materials
As we all know, it is very important to make materials. The integrity of the production data will also affect the quality of the steel mesh. Of course, the more complete the information, the better. At the same time, when there are several kinds of data coexisting, we should highlight which one should prevail. In addition, the steel mesh made of data file can reduce the error as much as possible.
5. Use of printing methods
Of course, the correct printing method can maintain the quality of the stencil and increase its service life. On the contrary, incorrect printing methods, such as too much pressure, and uneven stencil or PCB during printing, will damage the stencil to varying degrees.
6. Cleaning method
Solder paste is particularly easy to solidify. If you do not clean the solder paste or tin powder on the steel mesh in time, the opening of the steel mesh will be blocked, and it will be difficult and error to print again. Therefore, the stencil must be cleaned in time after it is removed from the machine or not printed on the printing machine for 1 hour.
7. Storage conditions
Different materials will have different storage environments. The steel mesh shall also be stored in a specific storage place, and shall not be placed randomly, so as to avoid accidental injury to the steel mesh. At the same time, the steel mesh must not be stacked together at will, which is not beautiful and bad, and may crush the mesh frame.