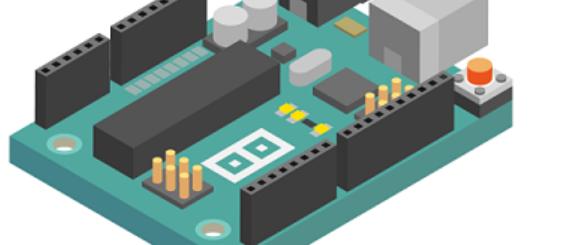
Electrostatic discharge may damage the device. But by taking correct and appropriate electrostatic protection and control measures, the establishment of electrostatic protection system, then you can eliminate or control the occurrence of electrostatic discharge, so that its damage to the components to the minimum. The basic ideas for electrostatic protection and control of electrostatic sensitive devices are as follows:
1. To prevent electrostatic accumulation in the place that may be grounded, take certain measures to avoid or reduce the generation of electrostatic discharge, or adopt the method of "generating while leaking" to eliminate the purpose of charge accumulation, and control the electrostatic charge in a way that does not cause harm;
2. Quickly and reliably eliminate existing charge buildup.
Electrical PCB boardelectrostatic protection design
In the production process, the core of electrostatic protection is "electrostatic elimination". To this end, a complete electrostatic working area can be established, that is, by using a variety of anti-static products and equipment, take various anti-static measures, so that the possible electrostatic voltage in the area is kept under the safe threshold for the most sensitive devices. The basic ways are:
1. Process control method. Process control method is designed to minimize electrostatic charge generation in trial production. Therefore, measures should be taken from the aspects of process flow, material selection, equipment installation and operation management to control the generation and accumulation of static electricity, inhibit the ability of electrostatic potential and electrostatic discharge, so that it does not exceed the degree of harm. For example, in the semiconductor manufacturing process, when the shallow junction formation of high-speed devices is completed, the resistivity of the deionized water for washing must be controlled. Although the higher the resistivity, the better the cleaning effect, but the higher the resistivity, the better the insulation, the higher the static electricity generated on the chip. Therefore, it is generally controlled at a level slightly higher than eight MΩ, not the 16-17 Mω used in the initial process. And in the choice of materials, packaging materials to use anti-static materials, as far as possible to avoid untreated polymer materials.
2. Leakage method. Leakage method aims to eliminate static electricity through leakage. Usually electrostatic grounding is the leakage of charge to the earth, there is also the use of increasing the object conductance method to make the earth along the surface of the object or through the internal leakage, such as adding electrostatic agent or humidification. The most common are anti-static wristbands worn by staff and electrostatic grounding posts.
3. Electrostatic shielding method. According to the principle of electrostatic shielding, it can be divided into internal field shielding and external field shielding. Specific measures are to use a grounded shield to isolate the charged body from other objects, so that the electric field of the charged body will not affect other objects around (internal field shield); Sometimes, the isolated object is surrounded by a shield to protect it from the influence of external electric field (external field shield). For example, GaAs devices are usually packaged with metal boxes or metal films.
4. Compound neutralization. The purpose of compound neutralization is to eliminate static charge by means of compound neutralization. Usually a ground eliminator is used to produce ions with different sign charges and charge on the charged body compound to achieve the purpose of neutralization. Generally speaking, when the charged body is an insulator, because the charge cannot flow on the insulator, it can not be used to leak the charge by grounding. At this time, it is necessary to use electrostatic eliminator to produce different ions to neutralize. For example, the static charge generated on the conveyor belt of the production line is eliminated by this method.
5. Cleaning measures. The cleaning measures are designed to avoid the phenomenon of tip discharge. To this end, the surface of the charged body and surrounding objects should be kept as smooth and clean as possible in order to reduce the possibility of tip discharge
SMT in the production process of PCB design requirements
In SMT patch processing technology, there are certain requirements for PCB design. Here, Pate Technology gives you an example:
1. PCB size and deformation:
A. PCB width (including board edge) : 50~250mm;
B. PCB length (including board edge) : 50~330mm;
C. Board edge width: > 5mm;
D. Plate spacing: < 8mm;
E. Distance between PAD and plate edge: > 5mm;
F. Upward bending degree: < 1.2mm;
G. Downward bending degree: < 0.5mm;
H. PCB distortion degree: maximum deformation height ÷ diagonal length < 0.25
2. Requirements of Mark:
A. Mark shape: standard circle, square, triangle;
B. The size of Mark; 0.8~1.5mm;
C. Mark material: gold plating, tin plating, copper platinum;
D. Mark surface requirements: smooth surface, no oxidation, no dirt;
E. Mark's surrounding requirements: there should be no green oil or other obstacles within 1mm around, which is obviously different from Mark's color;
F. Position of Mark: the distance from the edge of the plate is more than 5mm, and there can't be similar Mark holes and test points in the surrounding 5mm;
G. In order to avoid the wrong direction of board entry during production, the position difference between the Mark and the board edge on the left and right sides of PCB should be more than 10mm
3. Design rules for special pads
MELF column element: To prevent the element from rolling during reflow welding, a notch must be made in the pad
4, the handling of the through hole and wire
In order to avoid the flow of solder, the pilot hole should be more than 0.65 away from the surface mounting pad. No through-hole shall be provided under the chip element.
5, the handling of the through hole and wire
In order to prevent the thermal effect of a large area of copper conductor from affecting the welding quality, the width of the connecting part between the surface mounting pad and the wire should not be greater than 0.3mm
6. Layout of components
In SMT, components are arranged in the same direction as possible on the SMB.
When using wave crest welding, try to ensure that the solder joints at both ends of the chip element contact the wave crest at the same time.
If the chip elements with large size difference are arranged next to each other and the interval is very small, the smaller elements should be arranged in front of the flow direction of the on-line plate when the wave crest/backflow is passed;
When the components are interleaved, a certain interval should be left between them;
The PCB components close to the cutting slot side are easy to damage during separation.