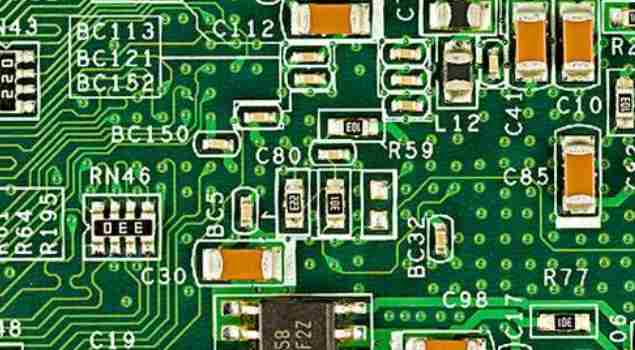
1. Through hole and pad:
Do not replace the hole with a pad, and vice versa.
2. Single side pad:
Do not use filler blocks to act as pads for surface mount components. Single side pads should be used. Normally, single side pads are not drilled, so the aperture should be set to 0.
3. Text requirements:
Character marks should be avoided as far as possible on the pad, especially on the pad of surface mounted components and on the Bottem layer, let alone printed characters and marks. If the space is too small to put the characters and need to be placed on the pad, and there is no special declaration whether to retain the characters, we will cut the character part of any upper pad on the Bottem layer (not the whole character cut) and the character part of the TOP layer of the surface sticker element on the pad when making the plate, in order to ensure the reliability of welding. Printing characters on large copper, first spray tin after printing characters, characters do not cut. The characters outside the board should be deleted.
4. Welding resistance green oil requirements:
A. In general, according to the specification design, the welding points of the components are represented by pads, these pads (including through holes) will automatically not solder, but if the filler block is used as the table to stick the pad or the line segment as the finger plug, and no special treatment, the solder oil will cover up these pads and fingers, easy to cause misunderstanding errors.
B. In addition to the Solder plate on the circuit board, if you need to avoid Solder solder ink in some areas (that is, special solder solder), you should use solid graphics on the corresponding layer (Top Solder Mark layer, Bottom Solder Mask layer) to express the area where do not solder ink. For example, if you want to expose a rectangular area of lead tin on the Top copper surface, you can directly draw this solid rectangle on the Top Solder Mask layer, instead of editing a single-side solder plate to express solder resistance ink.
C. For plates with BGA, the through-hole pad beside the BGA pad shall be covered with green oil on the component surface.
5. Requirements for copper paving area:
Whether it is made of grid or solid copper, the distance from the plate edge is greater than 0.5mm. The size of copper-free grid points must be larger than 15mil x 15mil, that is, in Plane Settings of the grid parameter setting window
(Grid Size value)-(Track Width value)≥15mil, Track Width value ≥10, if the grid copper free grid point is less than 15mil×15mil, other parts of the circuit board are likely to be open in production, then copper should be laid, set:
(Grid Size value)-(Track Width value)≤-1 Mil.
6. Expression of appearance:
Contour machining diagram should be drawn in the Mech1 layer, such as the plate with special-shaped holes, square slots, square holes and so on are also painted on the Mech1 layer, it is best to write CUT words and size in the slot, in the drawing of square holes, square slots and other contours to consider the processing turning point and end point of the arc, because the CNC milling machine processing, milling cutter diameter is generally φ2.4mm, The minimum is not less than φ1.2mm. If a quarter arc is not used to represent the turning point and the end fillet, it should be marked with an arrow on the Mech1 layer, and please indicate the tolerance range of the final shape.
7. The expression of the long hole on the pad:
The hole diameter of the welding pad should be set as the width of the long hole, and the outline of the long hole should be drawn on the Mech1 layer. Pay attention to the circular arc at both ends and consider the installation size.
8. Expression of metallized and nonmetallic holes:
Generally, the Multilayer pad holes without any explanation will be metallized. If not, please mark them on the Mech1 layer with arrows and words. For the special-shaped holes in the plate, square slots, square holes, etc., if the edge is surrounded by copper foil, please indicate whether the holes are metallized. Conventional hole and pad size or no pad and no electrical performance of the hole is considered as nonmetallic holes.
plated
No plated
9. How to set the hole size when the component foot is square:
Generally, when the side length of the square pin is less than 3mm, it can be assembled with a round hole. The aperture should be set to slightly larger than the diagonal value of the square (considering dynamic fit). Do not set it to the side length value, otherwise it cannot be assembled. For larger square feet, outline of square holes should be drawn on Mech1.
10. When multiple different boards are drawn in one file and want to split the delivery, please draw a border for each board in layer Mech1 with a space of 100mil between the boards.
11. The relationship between the setting of the hole aperture and the minimum value of the pad:
In general wiring, when placing components at the early stage, we should consider the foot diameter of components, pad diameter, hole diameter and hole diameter, so as to avoid the inconvenience caused by the wiring and then modification. If the component pad finished hole diameter is set to X mil, the pad diameter shall be set to ≥X+18mil.
X: Set welding aperture (our company's technological level, minimum value 0.3mm).
d: Hole diameter at production (generally equal to X+6mil)
D: Outer diameter of pad
δ : (d-X) /2: thickness of metallized pore wall
The hole setting is similar to the welding pad: generally, the hole aperture is ≥0.3mm, and the hole plate is ≥X+16mil.
12. The relationship between the diameter of the finished hole (X) and the diameter of the electrical and ground isolation disk (Y) : Y≥X+42mil, isolation bandwidth 12mil