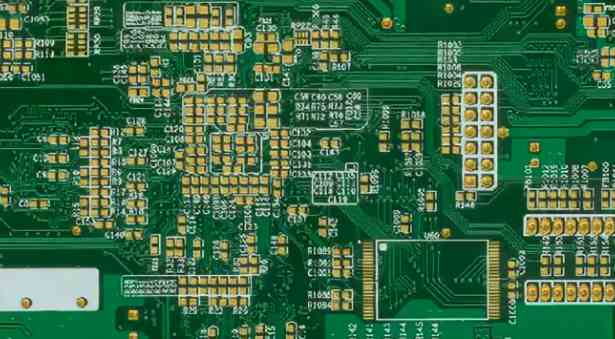
It is well known that copper has been poor in work hardening and stress fatigue. If the final application of the flexible circuit requires repeated folding or displacement, then high grade rolled toughened copper foil (RA) is a better choice. Obviously, the additional rolling toughening step is bound to increase the cost, but the rolled toughened copper foil can be bent and folded more times before fatigue fracture. And it has increased elasticity in the Z deflection direction, which is what we need, and in applications that bend and roll a lot, it gives us a longer life. Because the rolling toughening process elongates the grain structure in the plane direction.
Exaggerated version of the rolling toughening process illustration, non-proportional composition. After passing through the high-pressure roller, the copper foil can extend its grain structure in the plane direction, making the copper softer and increasing the elasticity of the z axis.
Typical examples are the link between a bench and a milling cutter head, or the laser head in a Blu-ray drive (as shown below).
In blu-ray machines, flexible circuits are used to connect the laser to the main circuit board. Please note that the flexible circuit on the laser head circuit board needs to be bent at right angles. A rubber bead is used here to strengthen the connection of the flexible circuit.
adhesive
Usually, we need an adhesive to bond copper foil to PI film (or other film), because unlike traditional FR-4 rigid plates, rolled and toughened copper foil surface does not have many burrs, so high temperature, high pressure does not achieve good bonding. Manufacturers such as DuPont offer single - and double-sided, corrodable copper-coated foil laminates. It uses an acrylic or epoxy adhesive ½ mil or 1 mil thick. This adhesive was specially developed for flexible circuit boards.
"Glue-free" laminates are becoming more common due to the introduction of new processes such as plating and depositing copper skin directly onto PI films. In HDI circuits where finer spacing and smaller through-holes are required, this film can be useful.
Silicone, hot melt, or epoxy resins are used when protective beads need to be added to the soft and hard joints. This increases the mechanical strength of the soft and hard joints and ensures that no stress fatigue or tearing occurs during repeated use. Is the best example.
summarize
It is important to have a clear understanding of the materials used in flexible circuit boards or BDS. We can also leave this to the manufacturers, who are free to choose the materials according to the application, but this sets the stage for the failure of the final product.
Understanding the properties of materials can also help us design, evaluate and test the mechanical parts of products. If the product is developed for automotive applications, then heat dissipation, moisture resistance, chemical corrosion, impact, etc. need to be carefully simulated to use the correct materials to achieve high reliability and minimum allowable bending radius of the product. Ironically, driving us to choose the flexible latter hard and soft combined with the practical application of the board, often will be exposed to harsh conditions. For example, low-cost consumer personal electronic devices are often plagued by vibrations, drops, sweat, and more.
Construction flexible plate
At first glance, a typical flexible board or a combination of soft and hard panels looks unimpressive. However, making them requires a few extra steps. The manufacture of any combination of soft and hard plates begins with the manufacture of one - or two-sided flexible plates. As mentioned last week, manufacturing can start with pre-pressed soft plates, or possibly with PI film, and then copper plate is pressed on top of the original bare plate, or copper coated. The laminating process requires a thin layer of adhesive to be brushed on the film, while the glue-free process requires a copper-plated "seed" to be planted on the film. The "seeds" are often planted using vapor deposition techniques such as sputtering to plant condensation nuclei for the chemical precipitation process that follows. The subsequent drilling, plating, and etching of a single - or double-sided flexible plate is generally similar to that of a double-sided rigid plate.