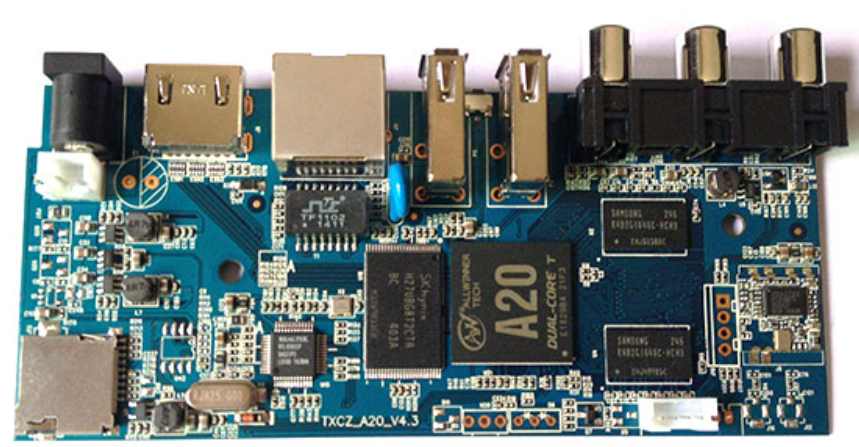
1. Accuracy of electrical connection
The wiring shall conform to the electrical schematic diagram, and the wiring that fails to be laid shall be described in the relevant technical documents.
2. The manufacturability of printed circuit boards.
PCB manufacturing plant equipment processing capacity, technology level should meet the PCB processing requirements.
Under the premise of satisfying the use, less use of fine wire, small holes, special-shaped holes, slots and blind holes, buried holes.
The number of layers on the printed circuit board should be minimized.
The dimensions shall conform to GB/T9315.
3, the reliability of printed circuit boards.
Try to use common materials and mature processing techniques.
The design should strive to be simple, symmetrical structure, uniform layout.
The number of layers of the printed circuit board should be as little as possible, and the diameter and aperture of the pad, the width and spacing of the wire should be as large as possible.
Plate thickness aperture ratio can be adjusted according to the existing technological level and product demand, the recommended use is 3:1~5:14
4. Maintainability of printed circuit board components.
Sufficient distance should be left between components to facilitate maintenance and replacement of components.
Easy to test.
5. The cleanability of printed circuit board components.
Highly reliable PCBA assembly must be thoroughly cleaned after welding; When designing and installing components, sufficient space must be left between the component body and the PCB to ensure adequate cleaning and cleanliness testing.
6. PCB substrate selection
The design should be based on the use of PCB conditions and mechanical, electrical performance requirements of the selection of substrate.
According to the size of the printed circuit board, unit area bearing component quality, determine the thickness of the substrate board.
Electrical performance requirements, Tg and CTE, flatness and the ability to metallize holes should also be considered in selection
Unless otherwise specified in the design, the substrate used for the printed board is a flame retardant epoxy textile glass fabric substrate (FR-4).
Lead and lead-free components mixed PCB should choose FR-4 plate substrate with higher glass conversion temperature, its performance should conform to the provisions of GJB2142.
7. Selection of electronic components
Electronic components should be selected according to the electrical performance, reliability and manufacturability requirements of the product, the type, size and packaging form of components, as far as possible use conventional components.
The selected electronic components shall be consistent with the design standards, suitable for the process and equipment standards, and meet the requirements for the selection of electronic components of military electronic equipment.
The designer shall consider the component's assemblability, testability (including visual inspection) and maintainability; SMD/SMC not suitable for heat resistance requirements of wave soldering and reflow welding should not be used in principle; If necessary, the SMD/SMC welding temperature below 250℃ shall be stated on the circuit design document; Careful consideration should be given to QFPS with pin spacing less than 0.5mm.
The designer should consider the completeness and availability of information related to the manufacture (e.g. integrity of components, detailed dimensions, and pin materials, process temperature limits, etc.).
8. Welding mode determines PCBA component layout design and welding pad graphic design
The PCBA welding process has three forms: reflow welding, wave soldering and hand welding. Different welding methods, component layout design, printed circuit board and pad graphic design and hole design are also different.
The application of wave-crest welding technology and reflow welding technology are completely different in component layout design, PCB and pad graphic design and hole design.