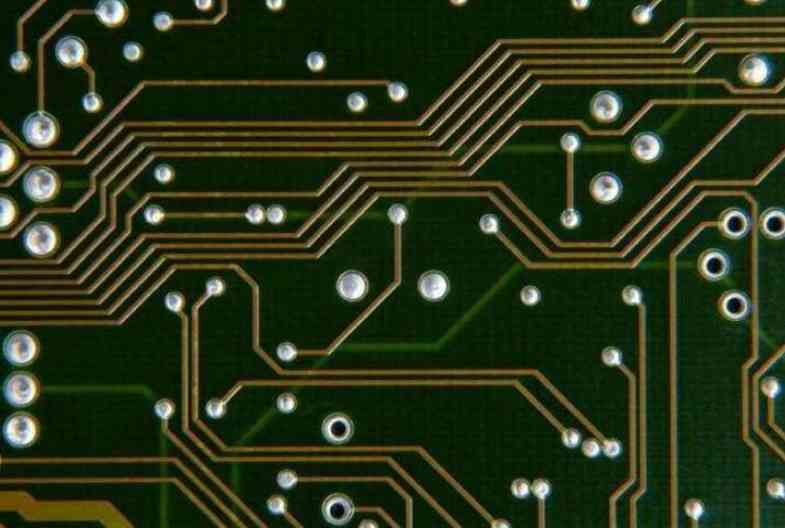
The printed circuit board is located on its schematic
Everyone knows that the most efficient way to shop for groceries is to prepare a shopping list before you go. Not only will you save money and move faster, but you'll also help you say "no" to tempting foods that may not be part of your diet. Preparing such written plans can help any project we are involved in. In the electronic field, these plans are called schematics.
The schematic details the circuits built in and mounted on the printed circuit board. Originally hand-drawn on a drawing table, it now uses computer-aided design tools to create schematics. These CAD systems are also linked to PCB layout tools, circuit simulators, and parts procurement systems for the overall design of the entire board. No matter how much automation is involved, it is still the responsibility of the electronics designer to carefully produce clean and readable schematics. To that end, here are some best practices that can help when capturing circuit board schematics.
Prepare the schematic diagram of the captured circuit board
The first step to creating an organized sketch is to become familiar with your CAD tools and use them proficiently. Spending hours trying to execute simple commands is frustrating and can have a negative impact on your work. Fortunately, there are many ways to solve this problem, including online training courses from vendors, user groups, white papers, and instructional videos. In addition, taking the time to learn your tools will greatly increase productivity.
Your CAD tools also need to be ready for the work you will be doing. Although they work right out of the box, most people customize the tools to improve ease of use and maximize productivity. Here are some CAD system customizations you should consider:
Parameters: You can adjust these parameters to change colors, grids, and many other Settings. These Settings can usually be automatically saved or read by the tool as a startup file.
Template: Most companies want their contact and legal information to be included on the schematic. These can usually be generated by CAD systems or by drawing templates that read existing information.
Design rules: Most companies will work according to an established set of design rules that can be changed for each design. As with other Settings, design rules and constraints are usually read in automatically at startup or obtained through a read me file.
Library links: These links are usually read automatically, but designers often attach to new library links manually based on the needs of unique parts.
In addition to preparing CAD tools for schematic capture, there are other steps that designers need to take before they begin. This includes working with other design team members to coordinate between the software and mechanical parts of the design. The designer should also determine the physical parameters of the PCB before beginning, as these will affect the circuit being designed. Although these parameters often change during the design process, it is still a good practice to start with the size, shape, and layer stack of the board that is as close to the final product as possible. It is also useful to involve the board manufacturer to ensure that the board can be built as designed.
With the parameters set, the next step is to prepare the library parts that will be used in the schematic.
Some schematic parameters that can be set in CAD system
A complete schematic notation and part library are essential
Creating a schematic requires that you have all the symbols at your disposal. These symbols can be imported or built into a CAD system using built-in drawing capabilities for drawing lines, circles, and polygons. The symbol building tool also allows you to create text and assign electrical properties. The key to building the correct symbol is to use the most up-to-date part information, which requires some research. Another option is to use automated tools in CAD systems to generate symbols. These symbol creation wizards use industry standards to create the appropriate size and shape.
In addition to symbols, other parts of a part can also be used to make complete components. This includes physical packaging of the PCB layout, electrical parameters connecting schematic symbols to the PCB packaging, and simulation and 3D models. All of this information should be kept in a library accessible to designers, and many companies use project and company libraries in combination for a more efficient library organization.
There is another way to collect all the library data you need, and that is to use a third-party library service. Online catalogs provided by these vendors list the thousands of parts available to them, allowing designers to select and download symbols, packages, and 3D models of the parts they need. These library providers are also typically available from your schematic capture tool, as shown in the figure below. Here you can see that EEPROM has been selected, allowing the designer to open its datasheet and image files and view part information, symbols, and packages. This section can then be pulled into the schematic, and all required data files are automatically saved in the session.
After collecting the library parts, you are ready to capture the schematics.
Unified Parts Search tool in Cadence Allegro