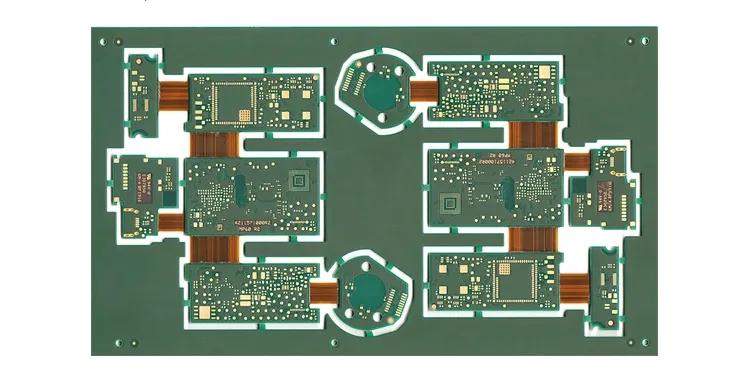
Circuit board engineer introduces circuit board design specification
1. Purpose
Standardize the PCB process design of products, specify the relevant parameters of PCB process design, make the PCB design meet the technical specification requirements of producibility, testability, safety, EMC, EMI, etc., and build the process, technology, quality, and cost advantages of products in the process of product design.
2. Scope of application
This specification is applicable to PCB process design of all electrical products, and applies to but is not limited to PCB design, PCB feeding process review, single board process review and other activities. If the contents of relevant standards and specifications before this specification conflict with the provisions of this specification, this specification shall prevail.
3. Definitions
Through hole (via): a metallized hole used for inner layer connection, but not used for inserting component leads or other reinforcement materials.
Blind via: conductive hole extending from the printed board to only one surface layer.
Buried via: a kind of through hole that does not extend to the surface of printed circuit board.
Through via: conductive hole extending from one surface layer of printed circuit board to another surface layer.
Component hole: hole used for fixing component terminals on printed boards and electrical connection of conductive graphics.
Stand off: the vertical distance from the bottom of the body of the surface mount device to the bottom of the pin.
4. References
TS-S0902010001<<Code for Safety Design of Information Technology Equipment PCB>>
TS-SOE0199001<<Code for design of forced air cooling and heating of electronic equipment>>
TS-SOE0199002<<Design Specification for Natural Cooling Heat of Electronic Equipment>>
IEC60194 (Printed Circuit Board design manufacture and assembly terms and definitions)
IPC-A-600F<<Acceptance of printed board
IEC60950
5. Specifications
5.1 PCB board requirements
5.1.1 Determine the board used for PCB and TG value
Determine the plate used for PCB, such as FR-4, aluminum substrate, ceramic substrate, paper core board, etc. If the plate with high TG value is selected, the thickness tolerance shall be indicated in the document.
5.1.2 Determine the surface treatment coating of PCB
Determine the surface treatment coating of PCB copper foil, such as tin plating, nickel plating gold or OSP, and indicate it in the document.
5.2 Thermal design requirements
5.2.1 High heat devices shall be considered to be placed at the air outlet or the position conducive to convection
In PCB layout, it is considered to place the high heat components at the air outlet or the position conducive to convection.
5.2.2 Higher elements shall be placed at the air outlet without blocking the air path
5.2.3 The radiator shall be placed to facilitate convection
5.2.4 Temperature sensitive devices shall be kept away from heat sources
For heat sources with their own temperature rise higher than 30 ℃, general requirements:
a. Under the air cooling condition, the distance from temperature sensitive devices such as electrolytic capacitors to the heat source is required to be greater than or equal to 2.5mm;
b. Under natural cold conditions, the distance from temperature sensitive devices such as electrolytic capacitors to heat source shall be greater than or equal to 4.0mm.
If the required distance cannot be reached due to space, temperature test shall be carried out to ensure that the temperature rise of temperature sensitive devices is within the derating range.
5.2.5 Large area copper foil is required to be connected with bonding pad with insulating tape
In order to ensure good tin penetration, the bonding pad of components on a large area of copper foil is required to be connected to the bonding pad with a heat barrier. For the bonding pad that needs to pass a high current of more than 5A, the thermal insulation bonding pad cannot be used, as shown in the figure:
5.2.6 Thermal symmetry of bonding pads at both ends of 0805 and below wafer components with over reflow soldering
In order to avoid the phenomenon of offset and monument after reflow soldering of devices, the bonding pads at both ends of 0805 and below chip components of ground reflow soldering should ensure the symmetry of heat dissipation, and the width of the connection between the bonding pad and the printed wire should not be greater than 0.3mm (for asymmetric bonding pads), as shown in Figure 1.
5.2.7 Installation method of high heat components and whether radiator is considered
It is determined that the installation mode of high heat components is easy to operate and weld. In principle, when the heat density of components exceeds 0.4W/cm3, the lead leg of components and components alone cannot sufficiently dissipate heat. Measures such as heat dissipation network and bus bar should be taken to improve the over-current capacity. The legs of bus bar should be connected at multiple points. Riveting and then wave soldering or direct wave soldering should be used as far as possible to facilitate assembly and welding; For the use of longer bus bars, the PCB deformation caused by the mismatch between the heated bus bars and the PCB thermal expansion coefficient when passing the wave crest shall be considered.
In order to ensure easy operation of tin coating, the width of tin bead shall not be greater than or equal to 2.0mm, and the distance between tin bead edges shall be greater than 1.5mm. Standardize PCB process design, specify relevant parameters of PCB process design, and make PCB design meet producibility. PCB manufacturers explain PCB design specifications for you.