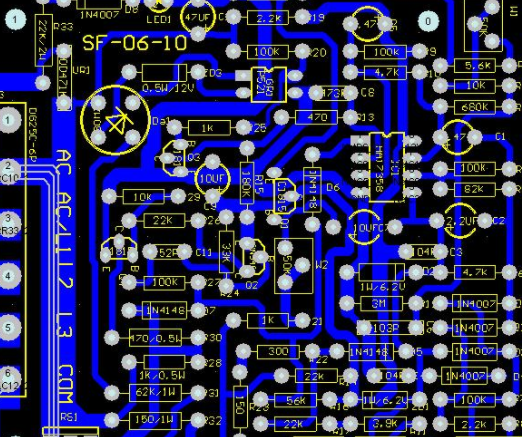
Production failures and solutions of rigid circuit boards and flexible circuit boards
During the execution of PCB pattern electroplating, PCB and FPC terminal surface treatment, such as gold immersion, electrogold plating, electrotin plating, tin and other process treatment, we often find that the finished board has leakage at the edge of dry film and wet film or the edge of solder mask Electroplating, or the appearance of most circuit boards, or the appearance of some parts of circuit boards, regardless of the situation, will bring unnecessary waste products or defects, which will bring unnecessary trouble to the post-processing, even the final waste products Heartbreak! Investigate the reason, everyone usually thinks about the parameters of dry film and wet film, and the efficiency of data; Solder resist such as hard board ink, protective film of soft board, or problems in printing, urgent, curing, etc, It is true that every place may cause this problem. Then, we are also confused that after inspection, the above parts have no problems, or the problem has been solved, but there is still leakage. What is the reason? Haven't found it yet?
Printed circuit board
After the dry film or wet film treatment of the line section, side etching and back etching will occur when etching the line, resulting in insufficient line width or uneven lines The reason is that improper selection of dry and wet film data, improper exposure parameters, poor performance of the exposure machine, unreasonable adjustment of nozzles for development and etching, improper adjustment of relevant parameters, improper concentration range of chemical solution, improper transmission speed and other series may lead to problems However, we often find that after checking the above parameters and the performance of related equipment, no abnormality is found, but when manufacturing the circuit board, excessive corrosion and pitting of the circuit still occur Why?
The circuit board will be tinned before shipment Of course, the customer will solder the parts during use It may occur in two stages, or immersion tin or solder mask blistering may occur in one stage When peeling the substrate, even the peeling strength of the ink on the tape is tested. When the tensile machine tests the peeling strength of the soft board covering film, serious peeling of the ink or insufficient or uneven peeling strength of the covering film will occur This is especially true for customers Precise surface mounting is absolutely unacceptable to customers In the welding process, once the solder mask bubbles and peels off, it will lead to inaccurate installation of the original parts, loss of a large number of components, and missed work by the customer The circuit board factory will also face huge losses such as deduction, replenishment and even loss of customers So when we usually encounter such problems, what would you start with? We usually go to analyze where it is the problem of solder mask (ink, cover film) materials; Is there a problem with the screen printing, laminating and curing stage; Is there a problem with the plating solution? Wait a minute. In retrospect, we usually ask engineers to find out the causes from these chapters one by one and make improvements We also consider whether it is the weather? The weather has been relatively wet recently Does the board absorb water? (Both the base material and the solder mask are easy to avoid mobility) After some hard work? The possible problems were checked and improved What else hasn't been noticed?
In view of the above common puzzles and problems in the PCB and FPC industries, we conducted a lot of experiments and research, and finally found that the important reasons for the poor wiring problem are infiltration, delamination, blistering, and pretreatment, which are insufficient peel strength Part, including dry film and wet film pretreatment, solder mask pretreatment, electroplating pretreatment and other multi-stage pretreatment parts Speaking of this, maybe many insiders can't help laughing Pretreatment is the simplest Pickling, degreasing, and micro etching, in which pretreatment agents, performances, parameters, and even number formulas are well known by many scientific and technological personnel in the industry
The circuit board production process involves a large number of complex surface treatment solutions, such as copper electroplating, gold electroplating, tin electroplating, outsourcing service providers, etching, etc In most cases, process engineers will choose to delve into these more complex processes Analyze and strive to master these technologies and take them as a breakthrough to improve their scientific and technological capabilities At the same time, most factories also regard this as the salary standard and performance appraisal standard of engineers In general, there are few engineers in the field of pretreatment Carefully study, or directly purchase the finished degreasing micro etchant from the supplier, and use dilute sulfuric acid as the acid pickling solution for acid pickling. Many factories even produce micro electrolysis themselves, or they are equipped with the persodium, permannium system (formulation As we all know), purchase hydrogen peroxide stabilizer and use it together with the hydrogen peroxide sulfuric acid system. Degreasing is done by purchasing the finished degreasing agent from the supplier or purchasing degreasing powder for dilution
According to the investigation and research, many manufacturers have not fundamentally understood the subtle or key effects of liquid chemicals in the pretreatment process, and only focus on the appearance of the surface, such as the degreasing part, Fingerprints can be removed If it is invisible to the naked eye, it can be degreased For circuit boards, the degreasing process is not only to peel off the oil deeply bonded to the copper surface, but also to peel off more important chemical liquids The oil molecules are decomposed, so that the plate surface will not form secondary pollution At present, the degreasing agents and degreasing powders on the market usually only contain degreasing and rust removing ingredients, while other ingredients such as preservatives, surfactants, emulsifiers, and other important components have not been added at all to reduce costs; Even many suppliers buy their recipes from other places. They do not understand the role of each component, let alone study or combine actual circuit boards This process requires mixing and adding effective ingredients, so in fact, the degreaser used in many circuit board factories is not a special degreaser suitable for the circuit board industry, but the traditional degreaser is usually used in the hardware and mineral processing industries How can such products achieve good degreasing effect? The degreasing effect of the board can be seen with the naked eye Actually? Through high power microscope or oil film test, it can be found that a large number of fine oil molecules adhere to the surface of the plate How can such treatment effect ensure good adhesion, peel strength, and solderability in the subsequent anti-corrosion coating production process, solder mask, and terminal surface treatment? The influence and stability of necessary efficiency, such as property, are particularly important in our understanding of micro etching The micro-etching process of the circuit board industry actually has:
Remove the rust layer, oxide layer, and other foreign matter on the copper surface;
The copper surface is uniformly roughened to form a microscopical convey and deposit
The starting copper surface shall be resistant to gas and liquid corrosion for a short time to ensure the operability of subsequent surface treatment,
The content of peroxide and sulfuric acid is low, preventing the collision of chemical solution and the formation of polymer organic residues on the surface
The above is the explanation given by the editor of pcb circuit board company.
If you want to know more about PCBA, you can go to our company's home page to learn about it.
In addition, our company also sells various circuit boards,
High frequency circuit board and SMT chip are waiting for your presence again.