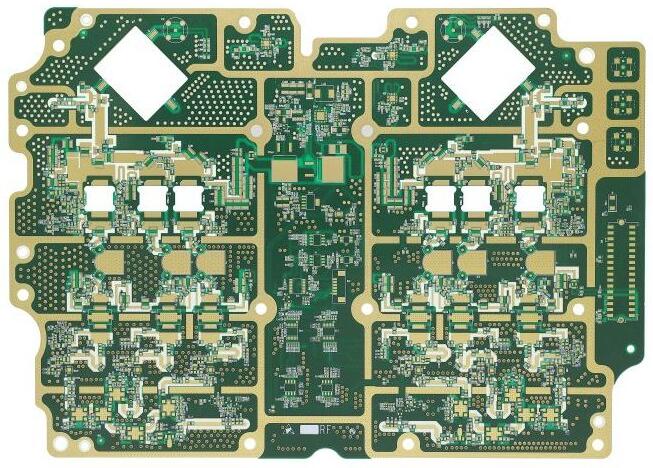
Surface treatment and wet process for PCB manufacturing
1. Abrasive
Abrasives are materials used to grind and brush copper surfaces before cleaning PCB surfaces, such as polymer nonwovens or nonwovens containing diamond sand, various free materials of its sand and pumice slurry. However, when the brush material is mixed with the sand material, its powder is often implanted on the copper surface, resulting in the adhesion problem between the subsequent photoresist layer or electroplated coating and solder.
2. Air knife
At the outlet of devices on various process lines, a high-temperature and high-pressure air knife is often installed to blow out the air knife. The air knife can dry the board quickly, which is convenient to carry and reduces the opportunity of oxidation.
3. Defoamer
In the process of washing printed circuit board processes such as dry film imaging solution, due to the dissolution of a large amount of organic film data and air mixing during the selection and spraying process, a large amount of foam will be generated, which is very inconvenient for the process. Chemicals that reduce surface tension, such as octanol or silica gel, must be added to the fluid to reduce the trouble of on-site operation. However, silicon resins containing silica cationic interface activators are not suitable for metal surface treatment. Because once it touches the copper surface, it is not easy to clean, resulting in poor adhesion or solderability of subsequent coatings.
4. Cohesiveness
Next layer: refers to the surface to be bonded (or followed), which must be kept clean to achieve and maintain good bonding strength, which is called "bonding".
5. Bank Agent
An important condition for fine etching is to add organic additives to the etching solution. As a kind of skin film, it is attached to both sides of the line. The current will wash away the weak current, so as to weaken the ability to be attacked by water drops and reduce the degree of Cmdercut. The agent is mainly confidential to suppliers.
6. Large inclination
This is a slight bite on the metal surface to make it look smoother and brighter, which is called wet treatment of the bath solution.
PCB process
7. Chemical grinding
Metal materials are processed by chemical wet fluid under different degrees of corrosion (such as surface coarsening). The stamping operation, also known as chemical blanking or photochemical processing (PCM) technology, which replaces some processing methods by deep etching or the application of precise special inhibitors, selective etching, etc., can not only save expensive mold costs and preparation time, but also eliminate the problem of residual stress in products.
8. Coating
This is often referred to as the processing layer outside the board. Usually any surface treatment layer.
9. Conversion film
It refers to simply immersing certain metal surfaces in specific grooves to form a protective layer of compound on the surface. For example, phosphating of iron surface, chromate treatment of zinc surface or zinc plating of aluminum surface can be used as "punching" of subsequent surface treatment layer, and improve adhesion and corrosion resistance.
10. Degrease
Traditionally, metal objects must be cleaned of excess oil left by machining before electroplating. Steam degreasing, organic solvent or immersion in emulsion solution are usually used for degreasing. However, degreasing is not required in the PCB process because there is almost no contact with oil in all processes, which is different from metal electroplating. Only the pretreatment of the sheet still requires a "cleaning" treatment, which is conceptually different from degreasing.
11. Etching coefficient
In addition to etching copper face down, the etchant also attacks the unprotected copper surface on both sides of the line, called undercut, resulting in mushroom shaped etching defects. The etching factor is the quota of etching quality.
Water droplets. Papua New Guinea
12. Etchant
In the printed circuit board industry, it refers to the chemical fluid used for etching copper layers. At present, most internal or single panels use acidic copper chloride, which has the advantage of keeping the panel clean and easy to automate management (single panels also use acidic ferric chloride as an etchant). Because tin and lead are used as corrosion resistance resistors, the outer layer quality of double-layer or multilayer panels can also be greatly improved.
13. Etch indicator
This is a special wedge pattern that emphasizes whether etching is excessive or insufficient. This specific pointer can be placed on the edge of the plate to be etched, or several etching templates can be intentionally added to the operation batch to improve the etching process.
14. Resist
An anti etching skin layer made on the copper surface is used to protect parts of the copper conductor that are not intended to be etched, such as the resistance of image transmission. Dry film. The ink pattern or tin lead coating is anti-corrosion.
15. Hard anodizing
Also known as "hard anodizing", it refers to placing pure aluminum or some aluminum alloys in low-temperature anodizing solution (15% sulfuric acid, 5% oxalic acid, lower than 10 ℃, lead plate for cold electrode, and anode current density of 15 ASF). After a long electrolysis process for more than one hour, 1-2 mil thick high hardness anodic oxide film (i.e. crystalline A12O3) can be obtained, and then dyed and sealed. This is a good aluminum anti-corrosion and decoration treatment.
16. Hard chrome plating
It refers to the thick chromium plating layer used for wear-resistant and anti-skid industrial purposes. Ordinary decorative chromium plating can only be applied on bright nickel surface for about 5 minutes, otherwise the cracks will last too long. Hard chrome can be used for several hours. The traditional electroplating solution consists of CrO3250g/1+H2SO410%, but when heated to 60 ℃, the cathodic efficiency is only 10%. In this case, other electric power generates a large amount of hydrogen, a large amount of harmful fog composed of chromic acid and sulfuric acid, and a large amount of yellow brown serious washing wastewater pollution. Although the wastewater needs to be treated strictly to increase the cost, the hard chromium coating is the wear-resistant coating on many axles or rollers and cannot be completely removed.
17. Mass finishing
For many small metal products, edges and corners must be carefully removed before electroplating. Scratches and polished surfaces must be removed to achieve the best substrate. After electroplating, the best appearance and anti-corrosion effect can be obtained. Usually, this pre plated substrate polishing can be done manually with a cloth wheel. However, a large number of small pieces depend on the processing of automatic equipment. Generally, the small pieces are mixed with grinding media specially designed for various shapes of ceramics and injected with various anti-corrosion solutions to finish polishing and finishing all parts of the surface in tens of minutes for inclined, slowly rotating and mutually grinding pipes. After dumping and separation, the coating can be rolled back into the barrel.
18. Micro etch
It is a station in the wet process of printed circuit board, which is used to remove foreign matters on the copper surface. Generally, the copper layer below 100 in shall be removed by biting m, which is called micro etching. The common micro solvent is "sodium persulfate" (SPS) or dilute sulfuric acid plus hydrogen peroxide. In addition, when microsilicon is used for microscopic observation, the polished metal section is also micro etched to view the structure of each metal layer at high magnification. This term is sometimes referred to as softening or micro peeling.
19. Rat bite
An irregular gap at the edge of an etched line, such as a rodent bitten by a mouse.
20. Overflow
The liquid level in the tank rises to the upper edge of the tank wall and flows out, which is called "overflow". In each cleaning station of the wet printed circuit board process, the tank is usually divided into several parts and cleaned with the dirtiest water overflow. It can be soaked for many times to save water.
21. Panel process
In the subtracting process of PCB, this is a direct etching process to obtain the outer layer. The process flow is as follows: PTH whole plate is coated with thick copper, the hole wall is covered with 1 mil positive dry film, and the hole is etched to remove the film to obtain the outer bare copper wire. This positioning process is very short. It does not require secondary copper, lead tin plating or lead stripping. It's really much easier. However, thin lines are not easy to do, and the etching process is difficult to control.
22. Passivation
A term used in metal surface treatment to refer to a stainless steel object immersed in a mixture of nitric acid and chromic acid to force the formation of a thin oxide film to further protect the substrate. In addition, an insulating layer can be created on the surface of the transistor, which enables electronic and chemical insulation on the surface of the transistor to improve its efficiency. This formation of surface cuticle is also called passivation.
23. Pattern processing
Another method of manufacturing PCB by reducing the shrinkage process is: PTH ->once copper plating ->negative image transmission ->twice copper plating ->tin lead ->etching ->tin lead removal ->obtaining bare outer copper sheet. This patterning process of secondary copper plating and tin lead plating is still the mainstream of various PCB processes. The reason for this is that it is safer and less likely to cause problems. For longer processes, additional issues such as tin lead and tin stripping are considered secondary considerations.
24. Water pit effect
When the plate is horizontally transported and sprayed upward or downward to form a water film, etching solution is deposited on the upper side of the plate, which hinders the effect of the fresh etching solution sprayed downward subsequently, and hinders the help of oxygen in the air, resulting in insufficient etching effect. The etching speed is lower than the speed of spraying on the lower side. This is the negative effect of water film. This is called the puddle effect.
25. Countercurrent cleaning
It is an anode, which suspends metal workpiece in cleaning solution and uses stainless steel plate as cathode. It uses the oxygen generated in the electrolysis process to dissolve (oxidize) the metal workpiece in the bath solution and clean the workpiece surface. This process can also be called "anode cleaning" anode electrolytic cleaning. This is a common metal surface treatment technology.
26. Flushing
In the wet process, in order to reduce the interference of chemicals in each tank, it is necessary to thoroughly clean the board at each intermediate stage to ensure the quality of various treatments, such as rinsing.
27. Sand blasting
The utility model is a surface cleaning method which uses high pressure to carry small particles sprayed onto the surface of an object at high speed. This method is very convenient for removing rust or scales difficult to tangle on metal. The sand to be sprayed is gold and steel sand. Glass sand. Nutcracker powder, etc. In the printed circuit board industry, pumice is mixed with water and sprayed on the surface of copper plate for cleaning.
28. Satin
It refers to the effect of various treatments on object surfaces, especially metal surfaces, to obtain luster. However, this process is not a full gloss mirror, it is only a semi gloss state.
29. Washer
It usually refers to the equipment that generates brush action on the board surface and can perform brush operation. Polishing. Cleaning and other work using different materials such as brushes or grinding wheels can also be carried out in fully automatic or semi-automatic pipes.
30. Sealing
After anodizing metal aluminum in dilute sulfuric acid, the cell layer of crystalline aluminum oxide on its surface has cell pores and is dyed with absorbable dyes. Then immerse it in hot water to make aluminum oxide absorb more crystal water, making the volume larger, thus forming smaller battery size and more durable color closure, which is called sealing.
31. Sputtering
In other words, cathodic sputtering, cathodic sputtering, or cathodic sputtering for short, refers to that under the conditions of high vacuum and high voltage, the metal surface atoms in the cathode will be squeezed out of the body, forming plasma in the form of ions in the environment, and then run to the object to be treated in the anode to accumulate a layer of skin film, which is uniformly adhered to the surface of crops, called cathodic sputtering coating. This is a metal surface treatment technology.
32. Stripper
It refers to the stripper used for metal coating, organic skin, etc., or used for strippers other than enamelled wire.
33. Surface tension
The inward attraction at the molecular level is part of the surface cohesion of the liquid. This surface tension (contraction) force tends to block the diffusion of liquid at the interface between liquid and solid. For the cleaning solution treated before the PCB wetting process, the surface tension (shrinkage) force should be reduced first, so that the board and hole wall can be easily wetted.
34. Surfactant
Chemicals added to various fluids used in the wetting process to reduce surface tension to help wet the hole wall through the hole are also called wetting agents.
35. Ultrasonic cleaning
The ultrasonic oscillation energy is applied to the cleaning solution to generate semi vacuum bubbles (cavitation), and the abrasive force of foam and the power of micro stirring are used to make the dead end of the articles to be cleaned have mechanical cleaning effect at the same time.
36. Undercut
The original meaning of this word refers to the early manual cutting. When the axe gradually cuts down trees from both sides of the root, up and down the slope, it is called cutting. In printed circuit boards, it is used in the etching process. When the planar conductor is etched under the protection of a blocking agent, theoretically, the etching solution will vertically erode downward or upward. However, due to the non directional effect of water, side etching will also occur, which will cause the conductor to appear in the cross section with water grooves on both sides, called undercut. However, it should be noted that only under the cover of ink or dry mask, the side etching produced by direct etching on the copper surface is the real undercut. In general, when the pattern is etched after twice copper and tin lead electroplating, and then the anti plating agent is removed, the secondary copper and tin lead may grow outward from both sides. Recall that the side etching part after etching can only be calculated for the upper line width of the negative, but the loss of its inward etching cannot be included in the outward widening part of the coating. In addition to the defects of copper etching in PCB process, similar side etching also exists in dry film imaging.
37. Water cut off
When the oil stain on the board is well cleaned, a uniform water film will be formed on the surface after immersion to maintain good adhesion to the board or copper surface (that is, the contact angle is very small). Generally, the water film remains intact in the vertical position for about 5-10 seconds. The clean copper surface can be kept flat for 10 to 30 seconds without cracking. As for dirty surfaces, even if they are flat, they will "burst" quickly and show discontinuous and separate "dehumidification". Because of the adhesion between the dirty surface and the water, it is not enough to offset the cohesion of the water itself. This simple method of checking panel cleanliness is called water hammer method.
38. Wet sand blasting
This is a physical cleaning method of metal surface driven by high-pressure gas, which forces wet and turbid abrasive (abrasive) to be sprayed on the surface to be cleaned to remove dirt. This is the type of wet pumice technology used in PCB technology.
39. Wet process
Printed circuit boards are manufactured by dry drilling Cohesiveness Exposure and other operations; But there are also electroplated holes that need to be immersed in water Copper plating, uniform imaging and film peeling in image transmission, wet method is initially called wet method