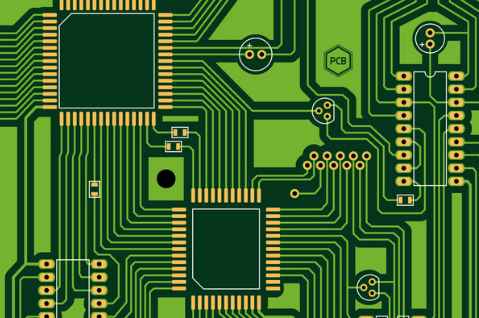
We are commonly known as machine operators, responsible for the production line daily loading. Look at the line. Lift the alarm, lift the fault, etc. Sometimes, of course, the production operation must carry out the maintenance of the line changing machine
Specifically:
Introduction to SMT process
Surface mounting technology, referred to as SMT, as a new generation of electronic mounting technology has penetrated into various fields, SMT products have the advantages of compact structure, small size, vibration resistance, impact resistance, high frequency characteristics, high production efficiency. SMT has taken a leading position in the circuit board mounting process.
A typical surface mount process is divided into three steps: application of solder paste ---- mount components ----- reflow welding
Step 1: Apply solder paste
The purpose is to apply an appropriate amount of solder paste evenly on the solder pad of the PCB to ensure that the patch components and the corresponding solder pad of the PCB achieve good electrical connection and have sufficient mechanical strength during reflow welding.
Solder paste is a paste made of alloy powder, paste flux and some additives, which has certain viscosity and good touching properties. At room temperature, because the solder paste has a certain viscosity, electronic components can be pasted on the PCB pad, in the case of tilt Angle is not too large, and there is no external force collision, the general component will not move, when the solder paste is heated to a certain temperature, the alloy powder in the solder paste melts and flows again, and the liquid solder wets the welding end of the component and the PCB pad. After cooling, the welding end of the component and the pad are interconnected by solder to form an electrical and mechanical connection solder joint.
Solder paste is applied to the pad by special equipment, the equipment is:
Automatic printing machine, semi-automatic printing machine, manual printing table, semi-automatic solder paste dispenser, etc.
The application of the method is good and weak
The machine printing batch is large, the supply cycle is tight, the funds are sufficient for mass production, the production efficiency is high, the use of complex processes, and the investment is large.
Manual printing small and medium-sized batch production, product development is simple, low cost, manual positioning, can not be mass production.
Research and development of manual drip coating ordinary circuit board, repair pad solder paste without auxiliary equipment, can be developed and produced only suitable for the pad spacing of 0.6mm or more
Step 2: Mount components
This process is to accurately mount the chip components to the corresponding position on the PCB surface with the solder paste or patch adhesive printed by the mounting machine or by hand.
There are two mounting methods, and the comparison is as follows:
The application of the method is good and weak
The machine mounting batch is large, the supply cycle is tight, suitable for mass production, the process is complex, and the investment is large.
Manual mounting small and medium-sized batch production, product development operation is simple, low cost Production efficiency depends on the proficiency of the operator
Manual mounting main tools: vacuum pen, tweezers, IC suction and release aligners, low ploid microscope or magnifying glass, etc.
Step 3: reflow welding
Reflow Soldring, a literal translation of the English term reflow soldring, is the soldering of mechanical and electrical connections between the solder ends or pins of surface-assembled components and the printed board pad by remelting the paste solder pre-allocated to the pad.
The principle of reflow welding is analyzed from SMT temperature characteristic curve (see figure). First of all, when the PCB enters the preheating temperature zone of 140 ° C ~ 160 ° C, the solvent and gas in the solder paste evaporate. At the same time, the flux in the solder paste moistens the solder pad, the component welding end and the pin, and the solder paste softens and collapses, covering the solder pad, and isolating the solder pad and the component pin from oxygen. When entering the welding zone, the temperature rises rapidly at the international standard temperature rate of 2-3℃ per second to make the solder paste reach a molten state, and the liquid solder on the PCB pad, component welding end and pin wetting, diffusion, diffusion and reflux mix on the welding interface to generate metal compounds, forming solder joints; Finally, the PCB enters the cooling zone to solidify the solder joint.
Introduction to reflow welding method:
Machine type Heating method advantages and disadvantages
Infrared reflow welding radiation conduction heat efficiency is high, the temperature gradient is large, easy to control the temperature curve, and the PCB temperature is easy to control when welding on both sides. There is a shadow effect, the temperature is not uniform, and it is easy to cause local burning of components or PCB.
Hot air reflow welding convection conduction temperature uniform, good welding quality. Temperature gradients are not easy to control
Forced hot air reflow welding Infrared hot air mixed heating combined with the advantages of infrared and hot blast furnace, in the product welding, can get excellent welding results
Forced hot air reflow welding, according to its production capacity is divided into two kinds:
Machine type Application Advantages and disadvantages
Temperature zone equipment mass production suitable for mass production of PCB board placed on the walkway, to sequence through a number of fixed temperature zones, temperature zone too little will exist temperature jump phenomenon, not suitable for high-density assembly board welding. And bulky, high power consumption.
In a fixed space, the temperature changes with time according to the set conditions, easy to operate, especially suitable for BGA QFP PLCC. Repairable defective surface mount components (especially large components) are not suitable for mass production
Because the reflow process has the characteristics of "reflow flow" and "self-positioning effect", the reflow process requires relatively loose mounting accuracy, and it is easier to realize the high automation and high speed of welding. At the same time, because of the characteristics of re-flow and self-positioning effect, reflow welding process has more stringent requirements for pad design, component standardization, component end and printed board quality, solder quality and process parameter setting.
Cleaning is the use of physical action, chemical reaction to remove the surface of the cleaning of pollutants, impurities process. Whether it is solvent cleaning or water cleaning, it is necessary to go through the surface wetting, dissolution, emulsification, saponification, etc., and by applying different ways of mechanical force to peel the dirt off the surface of the surface assembly board, and then rinsing or rinsing clean, and finally blow dry, dry dry or natural drying.
Reflow welding is a key process in SMT production, and reasonable temperature curve setting is the key to guarantee the quality of reflow welding. Improper temperature curves will cause PCB welding defects such as incomplete welding, virtual welding, component warping, and excessive solder balls, which will affect product quality.
SMT is a comprehensive system engineering technology, which covers the scope of substrate, design, equipment, components, assembly process, production accessories and management. SMT equipment and SMT process requirements for the operation site voltage to be stable, to prevent electromagnetic interference, to prevent static electricity, to have good lighting and exhaust gas emission facilities, temperature, humidity, air cleanliness of the operating environment have special requirements, operators should also go through professional technical training.