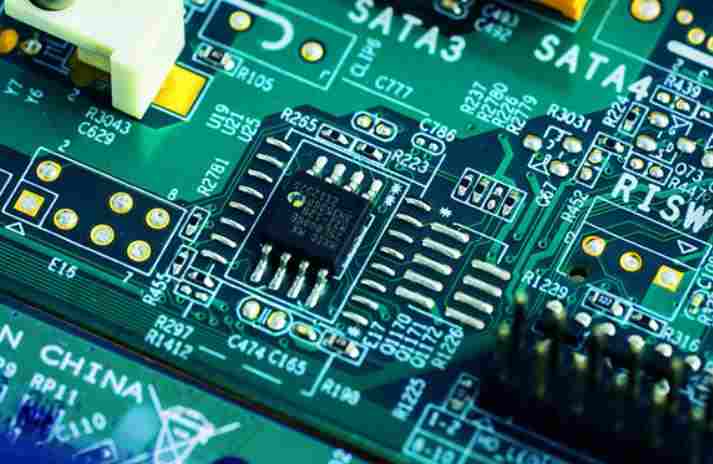
Analysis of reflow soldering furnace for SMT wafer processing
SMT wafer processing reflow soldering furnace is a kind of equipment used for welding surface mount components SMT patch processing reflow soldering furnace mainly includes infrared furnace, hot blast furnace, infrared heating blast furnace, steam welding furnace, etc At present, the most popular is the forced full hot blast furnace This section mainly introduces the forced full hot blast stove
1. Classification of reflow soldering furnaces for SMT wafer processing
There are many types of SMT wafer processing reflow furnaces According to the heating area of wafer processing and reflow soldering, it can be divided into two categories: heating the SMT circuit board as a whole, and refusing to heat the SMT circuit board
For the overall heating of SMT chip, there are box type and flow type reflow furnace, hot plate, infrared,
Circuit board
Full hot air, gas phase SMT patch processing reflow soldering furnace, box type reflow soldering furnace is suitable for laboratory and small batch production Flow type SMT patch processing reflow furnace is suitable for mass production
2. Full hot air reflow soldering furnace
Hot air reflow soldering furnace is the most widely used reflow soldering furnace at present. The main body consists of furnace body, upper and lower heat sources, SMT chip transfer device, air loop decoration, cooling device, exhaust device, temperature control device, nitrogen device, and waste gas recovery device and computer control system.
1. Air flow design
There are many manufacturers at home and abroad producing SMT chip reflow soldering equipment. The airflow design of each manufacturer is different, such as vertical airflow, horizontal airflow, large return air and small return air. No matter which method is used, high convection efficiency is required, including velocity, flow, mobility and permeability. The air flow should have good coverage. If the air flow is too large or too small, it is not good.
Air flow. Air or nitrogen enters the furnace from the fan inlet. After being heated by the heater, the forced hot air generator at the top transfers the heat of the hot air to the SMT chip assembly plate. The cooled hot air flows through the channel and is ejected from the outlet. Hot air patch processing and reflow soldering refer to the process in which hot air circulates continuously in the designed airflow direction and exchanges heat with the heated parts.
2. Heat source design
The heating efficiency of the re current curing furnace for SMT chip is related to the heat capacity of the heat source The high heat capacity heat source with large heat generator has good temperature stability and can control the temperature and air flow at the same time The heat distribution in the furnace is relatively uniform, but the thermal response is slow and the cooling speed is slow; Low heat capacity heat source with thin heating body has low cost Fast thermal response, but poor temperature stability, heat distribution, furnace temperature and air flow are difficult to control