Building 6, Zone 3, Yuekang Road,Bao'an District, Shenzhen, China
+86-13923401642Mon.-Sat.08:00-20:00
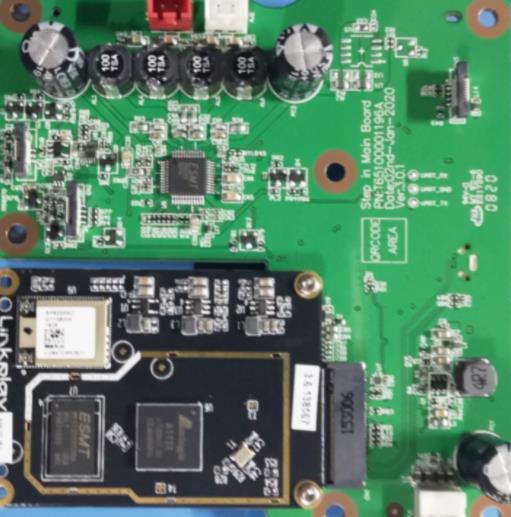
PCBA transport packaging and process control
After that, PCBA production has been completed and PCBA needs to be transported to customers by various pipelines During transportation, the following requirements shall be noted
1. Packaging materials
PCBA board is a relatively fragile and easily damaged product. Before transportation, it must be carefully packed with bubble bags, pearl cotton, electrostatic bags and vacuum bags.
2. Anti static packaging
Static electricity will penetrate the chips in the PCBA board. As static electricity is invisible, invisible and easy to produce, it is necessary to use anti-static packaging during packaging and transportation.
3. Moisture-proof packaging
Before packaging, the PCBA surface should be clean and dry, and sprayed with 3 anti paint.
4. Anti vibration packaging
Put the packed PCBA board into the anti-static packaging box. When placed vertically, no more than two layers shall be stacked, and spacers shall be placed in the middle to maintain its stability and prevent shaking.
This PCBA manufacturing process involves multiple links In order to produce good products, the quality of each link must be controlled General PCB board is composed of the following parts: PCB board manufacturing, component procurement and inspection, SMT chip processing, chip processing, program startup and a series of processes, tests, and aging
PCBA process control
1. PCB manufacturing
After receiving the PCBA command, analyze Gerber files, pay attention to the relationship between the PCB hole spacing and the board's carrying capacity, do not cause bending or damage, and whether key factors such as high-frequency signal interference and impedance are considered for wiring.
2. Procurement and inspection of components
The purchase of parts and components requires strict control of access, must be purchased from large traders and original manufacturers, and 100% avoid second-hand data and counterfeit data. In addition, a professional incoming material inspection post has been set up, and the following items have been strictly inspected to ensure that there is no failure of components.
PCB: reflow soldering furnace temperature test, no flying wire, through hole blockage or ink leakage, board surface bending, etc.
IC: Check whether the silk screen is completely consistent with the BOM and keep constant temperature and humidity
Other common data: check screen printing, appearance, power on measurement, etc. The inspection items shall be carried out according to the sampling method, and the proportion is generally 1-3%
3. SMT assembly and processing
Solder paste printing and reflow furnace temperature control are key, and it is very important to use laser dies with good quality and meeting process requirements. According to the requirements of PCB, it is necessary to enlarge or reduce some wire mesh holes, or use U-shaped holes to make wire mesh according to process requirements. The temperature and speed control of reflow soldering furnace is very important for solder paste penetration and welding reliability. It can be controlled according to normal SOP operation guidelines. In addition, AOI testing needs to be strictly implemented to minimize defects caused by human factors.
4. Piece processing
The mold design of wave soldering is a key point in the process of welding parts. How to use the mold to maximize the product quality after the furnace is a process that PE engineers must constantly practice and summarize experience.
5. Program startup
In the previous DFM report, customers can be suggested to set up some test Points (Test points) on the PCB to test the continuity of PCB and PCBA circuit after welding all components If you have conditions, you can ask the customer to provide a program, and burn the program into the main control IC through a burner (such as ST-LINK, J-LINK, etc.), so that you can test the effects of various touch actions more intuitively Function change to verify the functional integrity of the entire PCBA
After that, PCBA production has been completed and PCBA needs to be transported to customers by various pipelines During transportation, the following requirements shall be noted
1. Packaging materials
PCBA board is a relatively fragile and easily damaged product. Before transportation, it must be carefully packed with bubble bags, pearl cotton, electrostatic bags and vacuum bags.
2. Anti static packaging
Static electricity will penetrate the chips in the PCBA board. As static electricity is invisible, invisible and easy to produce, it is necessary to use anti-static packaging during packaging and transportation.
3. Moisture-proof packaging
Before packaging, the PCBA surface should be clean and dry, and sprayed with 3 anti paint.
4. Anti vibration packaging
Put the packed PCBA board into the anti-static packaging box. When placed vertically, no more than two layers shall be stacked, and spacers shall be placed in the middle to maintain its stability and prevent shaking.
This PCBA manufacturing process involves multiple links In order to produce good products, the quality of each link must be controlled General PCB board is composed of the following parts: PCB board manufacturing, component procurement and inspection, SMT chip processing, chip processing, program startup and a series of processes, tests, and aging
PCBA process control
1. PCB manufacturing
After receiving the PCBA command, analyze Gerber files, pay attention to the relationship between the PCB hole spacing and the board's carrying capacity, do not cause bending or damage, and whether key factors such as high-frequency signal interference and impedance are considered for wiring.
2. Procurement and inspection of components
The purchase of parts and components requires strict control of access, must be purchased from large traders and original manufacturers, and 100% avoid second-hand data and counterfeit data. In addition, a professional incoming material inspection post has been set up, and the following items have been strictly inspected to ensure that there is no failure of components.
PCB: reflow soldering furnace temperature test, no flying wire, through hole blockage or ink leakage, board surface bending, etc.
IC: Check whether the silk screen is completely consistent with the BOM and keep constant temperature and humidity
Other common data: check screen printing, appearance, power on measurement, etc. The inspection items shall be carried out according to the sampling method, and the proportion is generally 1-3%
3. SMT assembly and processing
Solder paste printing and reflow furnace temperature control are key, and it is very important to use laser dies with good quality and meeting process requirements. According to the requirements of PCB, it is necessary to enlarge or reduce some wire mesh holes, or use U-shaped holes to make wire mesh according to process requirements. The temperature and speed control of reflow soldering furnace is very important for solder paste penetration and welding reliability. It can be controlled according to normal SOP operation guidelines. In addition, AOI testing needs to be strictly implemented to minimize defects caused by human factors.
4. Piece processing
The mold design of wave soldering is a key point in the process of welding parts. How to use the mold to maximize the product quality after the furnace is a process that PE engineers must constantly practice and summarize experience.
5. Program startup
In the previous DFM report, customers can be suggested to set up some test Points (Test points) on the PCB to test the continuity of PCB and PCBA circuit after welding all components If you have conditions, you can ask the customer to provide a program, and burn the program into the main control IC through a burner (such as ST-LINK, J-LINK, etc.), so that you can test the effects of various touch actions more intuitively Function change to verify the functional integrity of the entire PCBA
Just upload Gerber files, BOM files and design files, and the KINGFORD team will provide a complete quotation within 24h.