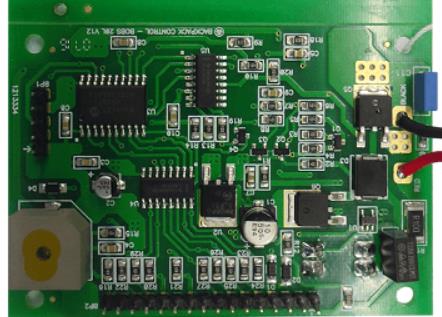
Poor placement of equipment and failure of placement machine
The placement accuracy of SMT equipment is the result of multiple factors In addition to the equipment itself, poor equipment recording will also have a great impact on it, mainly as follows:
A. The pitch error of the perforations is relatively large.
B. The shape of the equipment is not good.
C. The shape of the square hole of the braid is irregular or too large, which causes the equipment to hang or overturn laterally.
D. The adhesive force between the paper tape and the plastic hot pressing tape is too large to peel normally, or the device is stuck to the bottom tape.
E. There is oil stain at the bottom of the equipment.
6、 Common faults of chip mounter
1. In case of failure, it is recommended to solve it according to the following ideas:
A. The working order of the equipment and the logical relationship between them are analyzed in detail.
B. Understand the location, contact and extent of the fault and whether there is abnormal sound.
Circuit board
C. Understand the operation process before the failure occurs.
D. Whether it occurs on a specific placement head or nozzle.
E. Whether it occurs on a specific device.
F. Whether it occurs in a specific batch.
G. Does it happen at a particular time?
2. Common fault analysis
A. The component placement offset mainly refers to the position offset in the X-Y direction after the component is installed on the PCB. The reasons are as follows:
(1) Reasons for PCB board a: PCB warpage exceeds the allowable range of the equipment. The maximum upturn is 1.2 mm and the maximum drop is 0.5 mm b: The height of the support pin is inconsistent, resulting in uneven support of the printed board c: The flatness of the workbench support platform is poor d: The wiring accuracy of the circuit board is low and the consistency is poor, especially the huge difference between batches
(2) The suction pressure of the nozzle placed is too low, and the picking and placing should be higher than 400mmHG.
(3) The blowing pressure is abnormal during placement.
(4) The amount of adhesive and solder paste is abnormal or deviated. When the position drifts, this can lead to component placement or welding. When the worktable moves at high speed after being placed, too few components will cause the components to deviate from the original position, the coating position is inaccurate, and the corresponding deviation will occur due to its tension.
(5) The program data device is incorrect.
(6) The base plate is poorly positioned.
(7) The installation nozzle moves unevenly and slowly when it rises.
(8) The coupling between the power part and the transmission part of the X-Y worktable is loose.
(9) The nozzle of placement head is poorly installed.
(10) The purging sequence does not match the descending sequence of the placement head.
(11) The nozzle center data of the optical identification system and the initial data of the camera are set poorly.
B. The installation angle deviation of the device mainly refers to the angular rotation deviation during installation. The main reasons are as follows:
(1) Reasons for PCBA : the warpage of PCB exceeds the allowable range of device b: the height of support pins is inconsistent, resulting in uneven support of PCB. C: The flatness of the workbench support platform is poor. d: The wiring accuracy of the circuit board is low and the consistency is poor, especially the difference between batches is large.
(2) The suction pressure of the nozzle placed is too low, and the picking and placing should be higher than 400mmHG.
(3) During placing, the blowing pressure is abnormal.
(4) The amount of adhesive and solder paste is abnormal or deviated.
(5) The program data device is incorrect.
(6) The end of the suction nozzle is worn, blocked or stuck by foreign matters.
(7) The lifting or rotation of the installation nozzle is uneven and slow.
(8) The parallelism between the nozzle device and the X-Y meter is poor, or the nozzle origin detection is poor.
(9) The optical camera is improperly installed or the data equipment is improperly installed.
(10) The purging sequence does not match the descending sequence of the placement head.
C. Component loss: mainly refers to component loss between suction position and placement position.
The main reasons are as follows:
(1) Program data device error
(2) The pressure for installing the nozzle is too low. During disassembly and placement, the pressure should be greater than 400MMHG.
(3) The purging sequence does not match the placing sequence
(4) The pose detection sensor is bad
(5) Clean and maintain reflectors and optical identification cameras.
D. Abnormal pickup:
(1) The tape specification does not match the feeder specification.
(2) The vacuum pump does not work or the suction pressure of the suction nozzle is too low or too low.
(3) The plastic hot pressing tape woven at the picking position did not peel off, and the plastic hot pressing tape did not pull up normally.
(4) The vertical movement system of the suction nozzle is slow.
(5) The placement speed of placement head is selected incorrectly.
(6) The feeder is not firmly installed, the feeder bushing is not moving smoothly, and the quick switch and tape pressing are not good.
(7) The paper-cut machine cannot cut the woven fabric normally.
(8) The braid cannot follow the normal rotation of the gear, or the feeder does not operate continuously.
(9) The suction nozzle is not at the low point of the suction position, and the lowering height is not in place or does not move.
(10) In the pickup position, the central axis of the suction nozzle does not coincide with the central axis of the feeder, and there is a deviation.
(11) The falling time of the suction nozzle is not synchronized with the suction time.
(12) Feed part vibration
(13) The component thickness data device is incorrect.
(14) The initial value of suction piece height is wrong.
E. Random nonadhesion mainly means that the suction nozzle is not attached to the low point of the patch and there is missing attachment.
The main reasons are as follows:
(1) The PCB board warpage exceeds the allowable range of the equipment, the maximum warpage is 1.2mm, and the maximum warpage is 0.4mm.
(2) The height of the support pin is inconsistent or the flatness of the workbench support platform is poor.
(3) There is liquid on the nozzle or the nozzle is severely magnetized.
(4) The vertical motion system of the L nozzle runs slowly.
(5) The purging sequence does not match the descending sequence of the placement head.
(6) The glue on the printed board is insufficient, missing points or the machine pins are too long.
(7) The nozzle mounting height equipment is defective.
(8) The solenoid valve switch is poor, and the blowing pressure is too low.
(9) When NG occurs to a nozzle, the cylinder for placing the stopper of the device moves unevenly and is not reset in time
F. Poor film picking posture: mainly refers to films that stand or tilt.
The main reasons are as follows:
(1) The vacuum suction pressure is poorly adjusted.
(2) The vertical movement system of smt is slow to place the nozzle
(3) The falling time of the suction nozzle is not synchronized with the suction time.
(4) The initial values of suction piece height or component thickness are set incorrectly, and when the suction nozzle is at a low point, the distance between the suction nozzle and the feeding platform is incorrect.
(5) The packaging specification of the woven fabric is poor, and the components shake in the installation belt.
(6) The feeder thimble does not move smoothly
(7) The central axis of the feeder does not coincide with the vertical central axis of the suction nozzle, and the deviation is too large.