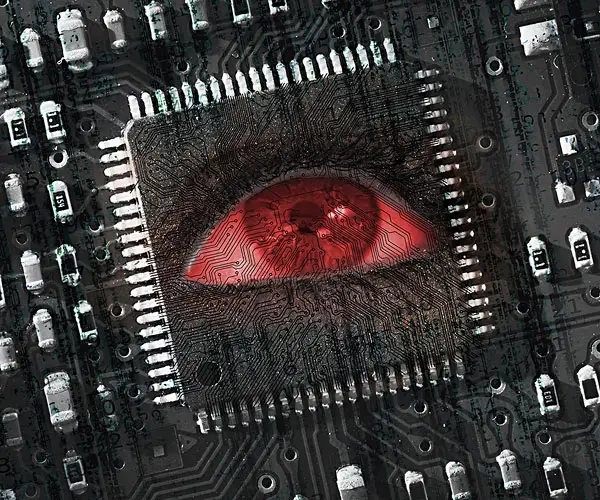
Market Background of Process Test Design in PCBA Assembly
PCBA processing is to connect various electronic components on PCB board through surface mount (SMT), plug-in (DIP) and other electronic assemblies. PCBA process flow mainly includes SMT, AOI, DIP, FCT testing and other processes. Due to the size difference of electronic components, there will be different processes and requirements in assembly and insertion. The assembly density of PCBA is relatively high, and the small size and light weight of electronic products also have certain changes and requirements in mounting. The reliability, seismic resistance and excellent weldability of the products have high requirements for the hardware and software facilities of PCBA processing.
As a relatively mature processing and manufacturing method, PCB manufacturers are entering the era of meager profits. The profit of PCBA processing is getting lower and lower, but the quality assurance requirements of PCBA processing are getting higher and higher. One of the companion requirements in PCBA assembly is consistency and correctness. The difference shall be controlled and variation is not allowed. In the process of assembly and manufacturing, there are three aspects of poor quality: design problems, material problems and assembly problems. The first two items need to take measures in advance to prevent their occurrence. Most of the problems in the assembly process, such as missing parts, damaged parts, wrong parts, offset, etc., can be visually inspected, but it is difficult to judge the welding quality by visual method, and sometimes there will be faults such as the blaster, plate bursting, and poor function delivered by PCBA to customers. According to the analysis and statistics of PCBA electrical assembly quality problems provided by the Reliability Research and Analysis Center of China Saibao Laboratory, the main assembly failure mode is poor welding, accounting for 57% of all poor assembly problems.
As the design of PCBA board tends to miniaturization, smaller devices, smaller problems, and more and more miniaturization (high density) of electronic assembly parts, PCBA solder joint defects, difficult detection and positioning, poor visibility and maintainability, and even irreparable, the potential failure risk also increases.
The traditional visual inspection control of PCBA assembly process can not completely eliminate the welding defects, but also requires automatic X-ray non-destructive testing, which has been widely applied in the Yangtze River Delta, Pearl River Delta, and military production, with very good results. However, the investment in adding equipment is relatively large. Many small and medium-sized circuit board manufacturers have complained about the increasing labor cost year after year. In addition, the continuous requirements of customers for processing quality make it impossible for weak circuit board manufacturers to add high cost detection methods,