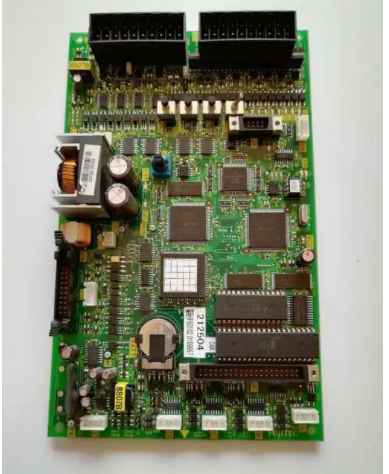
When we are designing PCB, we need to choose a laminated scheme for our board, a good laminated scheme can make our signal quality better, the performance of the board will be more stable, etc., we may have more or less contact with multi-layer board, that is, two layers up the board, so when we do six-layer board, have heard of "false eight layers", What does "false eight floors" mean? Is he six stories or eight? Before we can figure this out, we need to understand the following two points.
First, PCB stacking knowledgeOur PCB board is usually composed of core board, copper foil, semi-cured sheet (also known as PP sheet) and solder resistance oil.
Core board: composed of copper foil, solid resin material and glass fiber, the basic material for making PCB, has a certain hardness and thickness, and both surface layers have copper foil.
Semi-cured sheet (PP sheet) : mainly composed of resin and reinforcement material, reinforcement material is divided into glass fiber cloth, paper base, composite material and other types, and the production of multi-layer printed board used in the semi-cured sheet (bond sheet) is mostly made of glass fiber cloth as reinforcement material.
Second, the basic knowledge of PCB impedance
After we briefly understand the composition of our board, we also need to understand a knowledge point, that is, "impedance". With the rapid improvement of signal transmission speed and the wide application of high frequency circuit, the printed circuit board is also put forward higher requirements. The circuit performance provided by the printed circuit board must be able to make the signal not reflect in the transmission process, the signal remains intact, reduce the transmission loss, and play the role of matching the impedance, so as to obtain a complete, reliable, accurate, non-interference, noise transmission signal. Impedance matching is very important in high frequency design, and the quality of the signal is related to the impedance matching. The purpose of impedance matching is that all high-frequency microwave signals on the transmission line can reach the load point, and there will be no signal reflection back to the source point.
Usually the factors that affect our impedance are mainly plate, dielectric constant, copper thickness, solder resistance oil, line width, etc. If it is a difference line, then the distance between the difference lines will also affect the impedance. Generally, the thickness of the medium, the distance between the difference lines and the impedance are proportional, the copper thickness, the line width and the impedance are inversely proportional, and the general welding resistance oil brush will also reduce our impedance value.
Third, after we know this knowledge, we can enter the theme, what is the "false eight layers" :
The figure above shows a lamination of six layers of 1.6mm board thickness with two core boards inside. The thickness of the pp sheet of the first and fifth layers is 6.68mil, the core thickness is 9.84mil, and there are three pp sheets between the core board and the core board, so the thickness reaches 20.92mil. We use this lamination to design PCB. If there are many impedance lines on the board, we will find through calculation that the bottom of the table needs to control 50om single-end situation, the line width is 11mil, the line width of 100om difference is 8.5mil/9mil, and the line width of the inner 50om single-end reaches 12.50mil. The difference line width is 6.8mil/8mil.
The width of this line undoubtedly increases the difficulty of our design, and it may even be impossible to design it. Therefore, we can reduce the line width and meet the impedance requirements by changing the method of stacking. From the impedance knowledge introduced above, we know that the dielectric thickness is proportional to the impedance value. Therefore, if we want to reduce the line width of the surface layer, we can reduce the thickness of the medium by reducing the number of pp sheets between the surface layer and the second layer and choosing thinner pp sheet types. When the thickness of the medium decreases, the impedance value will also be small, and then the line width can be reduced to achieve our target impedance value.
The third layer refers to the second layer and the fifth layer, among which the third layer is closer to the second layer GND plane, and the fifth layer is further away from the third layer. We mainly refer to the second layer GND plane, which is more influenced by the second layer. Therefore, we can reduce the core value by changing the type of core board, and the thickness of the medium is reduced. In the case of the same line width of the third layer, the smaller the impedance value, then we have to achieve the target impedance value is the same to reduce the line width, so that the inner layer also reduces the line width and meets the requirements of the impedance, the fourth layer is the same, but at this time we will find that the pp sheet between the first two layers and five or six layers is thinner, and the core plate is thinner. At this time, to achieve the target plate thickness, we can only increase the thickness between the core plate and the core plate. We can increase the number of pp sheets to achieve the purpose of thickening, but we can not increase the number of pp sheets all the time. Generally, only three pp sheets can be used. We have already introduced the composition of the core board and pp sheet, which contain resin and glass fiber, but there is a copper foil on both sides of the core board. We can add a "core board" between the core board and the core board to meet our plate thickness requirements, but we remove the copper foil on both sides of this "core board". The new layer is shown in the figure below. At this time, we find that the 50om single terminal line width at the bottom of the table is 5.7mil, the 100om differential line width is 4.1mil/8.2mil, and the inner 50om impedance single terminal line width is 5.3mil, and the 100om differential distance is 4.1mil/8.2mil.
This line width is generally satisfied for the conventional design, then we can compare the two layers, you will find that the difference between them is that the core is thinner, and then the pp sheet of one or two layers and five or six layers is also thinner, and there is a core board without copper foil on both sides between the core board and the core board, then generally this layer we call "false eight layers".
After understanding the differences between them, we can also summarize their advantages and disadvantages:
1, in the case of impedance, we use a false eight-layer design can reduce our design line width, so as to meet our design requirements.
2, in the case of the third layer and the fourth layer of the six-layer layer, the use of the false eight-layer design can reduce the crosstalk between the third layer and the fourth layer, because the third layer and the fourth layer are adjacent layers, if the two layers are too thin, crosstalk will be generated, affecting the signal quality, so we increase the distance between the two layers of the false eight-layer design. Crosstalk will be relatively small, but we also need to note that in the case of adjacent wiring layers, we need to use "vertical wiring", that is, one layer of the line goes horizontal, the other layer goes vertical. 3, due to the increase in materials resulting in our cost will also increase accordingly, false eight layers is more expensive than six layers, but cheaper than eight layers.