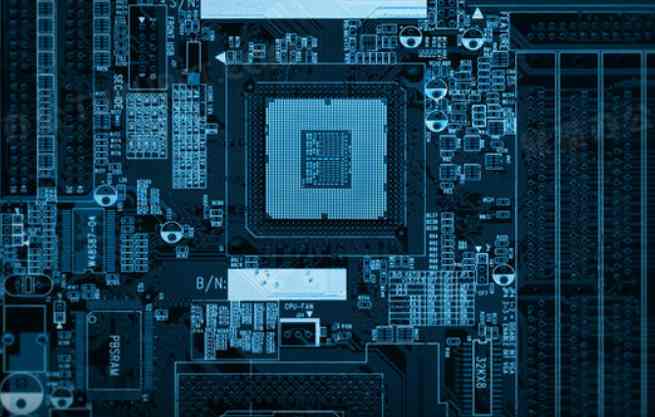
At present, most of the LED lights use LED aluminum substrate, aluminum substrate between the welding surface and the heat dissipation surface in order to solve the circuit and heat dissipation body insulation, voltage resistance, add a layer of epoxy resin insulation between them, although solve the problem of electrical performance, but directly lead to the increase of thermal resistance, but also from a certain extent of the impact of limited product life. For this reason, the emergence of ceramic film forming technology seems to have the momentum of large-scale application to replace aluminum substrate.
At present, most of the aluminum substrates used by LED lights, such as the insulation layer caused by epoxy resin, are not high in heat dissipation; The light decay rate is high, which results in the life less than the theoretical life. The stroboscopic situation is also common, and the color rendering index of many products on the market is below 80 stipulated by the national standard; Technical defects such as narrow voltage adaptability range.
At present, some enterprises have launched a new heat-conducting ceramic film LED lamp series to effectively solve the many shortcomings of traditional lamps and existing LED lamps, and achieve six revolutionary breakthroughs in the performance of the product, namely: light decay is smaller; Safer to use; Products are more environmentally friendly; Longer life and wider scope of application; Energy saving is better.
Industry experts also said that the introduction of ceramic film forming technology to the production of LED lamps, instead of aluminum substrate and aluminum shell, the middle of the epoxy resin and thermal glue link, in the heat dissipation performance is indeed better than aluminum substrate performance. However, as far as the current domestic ceramic film technology research and development level is concerned, the application process in LED lamps is not mature enough, and there is still a long way to go to achieve large-scale replacement of aluminum substrate intervention in LED lamps.
For the above described the future development trend of LED aluminum substrate, better let us know what kind of development status it will be in the future.
Characteristics, structure and function of LED aluminum substrate
The heat dissipation problem of LED is the most headache problem of LED manufacturers, but aluminum substrate can be used, because aluminum has a high thermal conductivity and good heat dissipation, which can effectively export the internal heat. Aluminum substrate is a kind of unique metal base copper clad plate, which has good thermal conductivity, electrical insulation and mechanical processing properties. The PCB should also be designed as close to the aluminum base as possible, thereby reducing the thermal resistance generated by the potting glue part. SMT steel mesh
First, the characteristics of aluminum substrate
1. Surface mount technology (smt);
2. Very effective treatment of thermal diffusion in circuit design;
3. Reduce product operating temperature, improve product power density and reliability, and extend product service life;
4. Reduce product volume, reduce hardware and assembly costs;
5. Replace the fragile ceramic substrate to obtain better mechanical durability.
Second, the structure of the aluminum substrate
Aluminum clad copper plate is a metal circuit board material, composed of copper foil, thermal insulation layer and metal substrate, its structure is divided into three layers:
Cireuitl.Layer Line layer: equivalent to ordinary PCB copper clad plate, line copper foil thickness loz to 10oz.
DiELcctricLayer: The insulation layer is a layer of low thermal resistance thermal insulation material.
baseLayer base: A metal substrate, usually aluminum or optionally copper. Aluminum based copper clad plate and traditional epoxy glass cloth laminate and so on.
The circuit layer (that is, copper foil) is usually etched to form a printed circuit, so that each part of the component is connected to each other, under normal circumstances, the circuit layer requires a large current carrying capacity, so that thicker copper foil should be used, the thickness is generally 35μm~280μm; The thermal insulation layer is the core technology of the aluminum substrate, which is generally composed of special polymers filled with special ceramics, small thermal resistance, excellent viscoelastic properties, thermal aging resistance, and ability to withstand mechanical and thermal stress.
The thermal insulation layer of high performance aluminum substrate uses this technology, so that it has excellent thermal conductivity and high strength electrical insulation performance; The metal base is the supporting member of the aluminum substrate, which requires high thermal conductivity, generally aluminum plate, copper plate can also be used (copper plate can provide better thermal conductivity), suitable for drilling, punching and cutting and other conventional mechanical processing. PCB materials have incomparable advantages compared with other materials. Suitable for power component surface mount SMT public art. Without heat sink, the volume is greatly reduced, the heat dissipation effect is excellent, good insulation and mechanical properties.
Third, the use of aluminum substrate:
Usage: Power Hybrid IC (HIC).
1. Audio equipment: input, output amplifier, balance amplifier, audio amplifier, preamplifier, power amplifier, etc.
2. Power equipment: switch regulator, DC/AC converter, SW regulator, etc.
3. Communication electronic equipment: high-frequency amplifier 'filter electrical' transmitting circuit.
4. Office automation equipment: motor drives, etc.
5. Automobile: electronic regulator, igniter, power controller, etc.
6. Computer: CPU board, floppy disk drive, power device, etc.
7. Power module: converter, solid relay, rectifier bridge, etc.