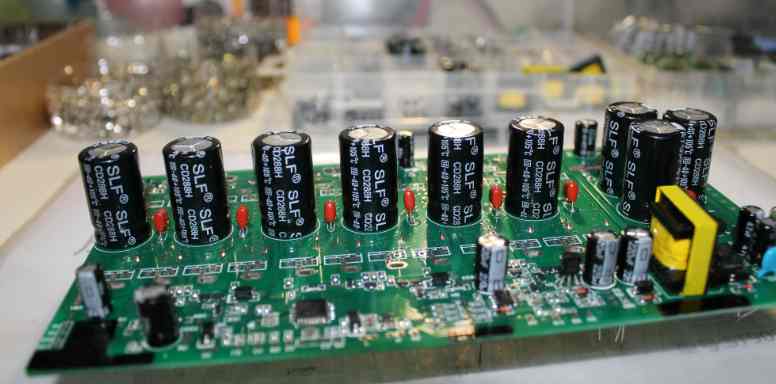
First, poor wetting
Poor wetting refers to the welding process of solder and substrate welding area, after wetting does not produce metal reaction, resulting in missed welding or less welding failure. Most of the reasons are polluted on the surface of the welding area, or stained with flux resistance, or caused by the formation of a metal compound layer on the surface of the joint, such as sulfide on the surface of silver, and oxide on the surface of tin. In addition, when the residual aluminum, zinc, cadmium, etc. in the solder exceeds 0.005%, the activity degree is reduced by the moisture absorption of the flux, and poor wetting can also occur. In wave soldering, if there is gas on the surface of the substrate, this fault is also prone to occur. Therefore, in addition to the implementation of appropriate welding techniques, anti-fouling measures should be taken on the surface of the substrate and the surface of the component, the appropriate solder should be selected, and a reasonable welding temperature and time should be set.
Two, bridge
Most of the causes of bridging are excessive solder or serious edge collapse after solder printing, or the size of the substrate welding area is out of line, SMD mounting offset, etc. In the stage of SOP and QFP circuitstending to micro-fine, bridging will cause electrical short circuit, affecting the use of products.
As corrective measures:
1, to prevent the welding paste printing when the edge is bad.
2, the size of the substrate welding area should meet the design requirements.
3. The installation position of SMD should be within the prescribed range.
4, substrate wiring gap, solder resistance coating accuracy, must meet the requirements.
5, formulate the appropriate welding process parameters to prevent the mechanical vibration of the welding machine conveyor belt.
Three, Cracks
When welded PCB is just out of the welding zone, due to the difference in thermal expansion of the solder and the part to be joined, under the action of quenching or heating, due to the influence of solidification stress or contraction stress, the SMD will basically produce micro-cracks, and the welded PCB must also reduce the impact stress on the SMD during punching and transportation. Bending stress.
In the design of surface mount products, it should take into account the reduction of the gap in thermal expansion, and correctly set heating and cooling conditions. Choose a good ductility solder.
Fourth, solder ball
The production of solder ball mostly occurs in the welding process of rapid heating and caused by the solder flying, in addition to the printing dislocation with the solder, the edge collapse. Pollution and so on are also involved.
Preventive measures:
1. Avoid excessive heating in welding, welding according to the set temperature process.
2. Solder printing edge, dislocation and other bad products should be removed.
3. The use of solder paste should meet the requirements without poor moisture absorption.
4. Implement the corresponding preheating process according to the welding type.
5. Suspension Bridge (Manhattan)
Bad suspension bridge refers to one end of the component leaves the welding area and leans upward or upright, the reason is that the heating speed is too fast, the heating direction is not balanced, the selection of welding paste, the preheating before welding, and the size of the welding area, the shape of the SMD itself, and the wettability.
Preventive measures:
1. The storage of SMD shall meet the requirements
2. The size of the substrate welding area length should be properly formulated.
3. Reduce the surface tension on the SMD end when the solder melts.
4. Solder printing thickness size should be set correctly.
Home -> News center
How is the quality of SMT processing managed
The quality of SMT processing is related to the performance, reliability, and production cost of electronic products. Therefore, how to make SMT machining and welding to achieve high quality and low consumption has always been the concern and research topic of the electronics industry. In today's increasingly fierce competition in electronic products, improving the quality of SMT chip processing has become one of the most critical factors. SMT chip processing quality level is not only a sign of enterprise technology and management level, but also closely related to the survival and development of enterprises.
When it comes to SMT processing and welding, people immediately think of only printing, paste, welding equipment production lines, and lack of adequate awareness of the management system that can promote the realization of high-quality and low-consumption welding quality. As everyone knows, this is often one of the main reasons why it is difficult to effectively grasp the welding quality of SMT processing.
Pre-welding quality inspection also includes: PCB electronic assembly design audit/or review; Audit/or review of welding process plans and procedures; Identification of outsourced units such as printed boards, components, welding process materials, and acceptance of warehousing; SMT production line equipment/fixture and instrumentation/equipment verification.
The quality control of welding also includes: key parameters of welding process materials; Process parameter inspection of each equipment; Quality control of work in each process (e.g. printing, pasting, welding, rework/repair, cleaning, etc.).
SMT welding quality management should be a systematic project. According to its content, it should generally include all personnel quality training, pre-welding quality inspection, welding quality prosecution, post-welding quality inspection and storage management.