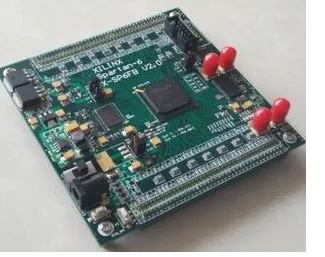
The quality of PCBA is affected by the reasonable setting of wave soldering process for plug-in devices in SMT patch processing
Adjustment elements of wave soldering process for SMT patch processing
1,Coating of flux
In THT wave soldering, the surface of PCB with SMC/SMD installed is uneven, which increases the difficulty of uniform coating of flux. Keeping the spray direction of the spray head perpendicular to the PCB surface is an effective means to overcome the spray shadow effect.
2, preheating temperature
In THT wave soldering, the preheating temperature should not only consider the activation temperature required by the flux, but also consider the preheating temperature required by SMC/SMD itself. Generally, the selection principle of preheating temperature is: the difference between the temperature of the SMA after the preheating zone and the temperature of the solder wave peak is less than 100℃.
3, solder, welding temperature and time
Because SMA is immersion wave soldering, the chance of contamination in the solder groove is much greater than that in THT wave soldering, so special attention should be paid to monitoring the impurity content of the solder in the solder groove. The maximum temperature and welding time used in THT wave soldering are selected according to the principle that in addition to providing heat to the weld, heat must also be provided to heat the component so that it reaches the welding temperature. When a higher preheating temperature is used, the temperature of the solder tank can be appropriately reduced, and the welding time can be extended as appropriate. For example, at 250 ° C, the maximum impregnation time of a single wave crest or the sum of the total impregnation time in a double wave crest is about 5S, but at 230 ° C, the maximum time can be extended to 7.5S.
4, PCB clip speed and Angle
In THT wave soldering, the better Angle is about 6° ~ 8°, and the crest welding surface of SMA is generally not as flat as the crest welding surface of THT, which is a potential factor leading to pinching, bridging, and missing welding. Therefore, the clamping Angle selection in THT wave soldering should be slightly larger, generally 6° ~ 8°. The clip speed must be selected so that the second wave peak has sufficient impregnation time, so that the larger components can absorb enough heat to achieve the desired welding effect.
5, immersion depth immersion depth refers to the depth of PCB immersion peak solder in THT wave soldering, the depth of the first wave peak is relatively deep, in order to obtain greater pressure to overcome the shadow effect, and the time through the nozzle is short, which is conducive to the remaining flux has enough dose to supply the second wave peak.
6, cooling in THT wave soldering, more than 2 minutes of slow cooling after welding, which is of great significance to reduce the stress caused by temperature upheaval and avoid damage to components (especially the fracture of components with ceramic as the basic or substrate).