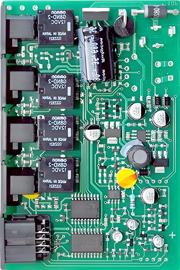
Electric vehicle universal battery management system solution
At present, it is not possible to design a battery management system witcircuit board
h good performance. Generally, there are two solutions in the specific work: first, design a universal simple protection Due to the secondary power battery sometimes there will be some safety accidents, so you can add a protective circuit board for the power battery, the same can be set for the working current, working temperature corresponding threshold, so as to ensure the safety of the battery pack.
2. Customizing complex solutions for specific batteries
Customizing battery management system functions according to power battery characteristics and requirements can be divided into the following steps.
1. Master the working characteristics of power batteries of relevant models according to the data provided by manufacturers and the records of battery sample evaluation in the early stage.
2. Determine the basic design scheme of the power battery management system, including:
a. Select an appropriate topology structure form;
b. Determine battery safety protection policies.
c. Supervised the power battery model and designed the residual power evaluation algorithm;
d. Determine the balance management policy and energy control policy.
3. Design the responsive software and hardware system according to the above scheme and carry out reliability verification. The technique of placing the parts on one side of the board and welding the pins on the other side is called plug-in packaging. Such parts take up a lot of space and require a hole to be drilled for each pin. So their joints actually take up space on both sides, and the solder joints are larger. Interfaces like wire sockets and things like that have to be pressure resistant, so they're usually THT packages.https://www.kingfordpcb.com/yuan.php?time=1685694568
Parts that use surface adhesive packaging are welded to the same side as the part. This technique does not weld holes in the PCB for each pin. SMT also has smaller parts than THT, and PCB boards using SMT technology are much more densely packed than PCB boards using THT parts. SMT packaging parts are also cheaper than THT's. So most of today's PCB is SMT, naturally not surprising.
Because the solder joints and parts are very small, it is very difficult to use manual welding. However, if you consider the current PCBA assembly is fully automatic, this problem will only occur when repairing parts.
The above is about "electric vehicle general battery management system solution" introduction, I hope to have some help to you, more PCBA information please pay attention to the content of the site updates! kinhford Electronic Technology Co., Ltd. is a professional PCBA processing enterprise, with fully automatic SMT production line and wave soldering, for you to open the whole production and quality testing process, find us, you belong to have your own electronic processing plant!