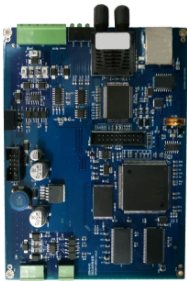
Technical analysis of SMT patch and THR through hole reflow welding
SMT reflow soldering is a welding method that forms solder joints by melting a pre-placed solder surface without adding any additional solder during the welding process. The advantages of this process are easy to control, oxidation can be prevented during welding, and production costs are relatively easy to control.
Reflow welding has become the mainstream process of surface mounting, it depends on the influence of hot gas flow on the solder joint, colloidal flux in a certain high temperature air flow for physical reaction, achieve SMD welding, the quality of PCBA solder joint completely depends on the performance of reflow welding equipment and the setting of temperature curve. The requirement for reflow welding cooling process is put forward, which also promotes the development of cooling zone of reflow welding equipment.
Due to the production and processing of reflow welding equipment, higher temperature control accuracy, temperature uniformity in temperature zone and transmission speed are required. Different welding systems have been developed from the initial three temperature zones, such as eight temperature zones and ten temperature zones, and the welding process and results are getting better and better.
1. Check whether the environmental impact assessment is qualifiedhttps://www.kingfordpcb.com/yuan.phphttps://www.kingfordpcb.com/yuan.php
Plants that do not meet environmental impact assessment requirements may be subject to random inspection, closure and rectification at any time.
3. Refer to raw material channel certificate
Ensure that all raw materials are sourced from official authentic sources to avoid mixing second-hand and defective materials into product production, which would bring great risk to end use.
4. Check the incoming inspection of IQC
Avoid batch composition errors, deviations, deformation or unqualified materials attached to the PCBA, which cannot be fully detected and covered in the test phase, bringing potential hidden dangers to the product, affecting stability, short service life and high after-effect sales pressure.
5. Look at ingredient storage
Effectively manage material storage to avoid transferring expired and invalid materials to the production line, which may lead to potential defects and risks in the product manufacturing process.
Static electricity may penetrate the components on the PCBA at any time, resulting in a large number of repairs, rapid shortening of product life and other potential defects; All electronic component racks and PCBA product racks must be connected using separate static wires; All employees must wear rope static ring and static alarm; Daily electrostatic spot check records must be maintained.
See independent three anti paint treatment
The external processing of three anti-paint is bound to cause the continuous transfer of PCBA, which is easy to cause collision, ESD electrostatic breakdown and other potential defects. PCBA factories need to be equipped with three anti-paint spraying production lines.Look at engineering skills
The PCBA factory must have the ability to analyze and resolve defective PCBA boards, ensuring that root causes are found, fast shipments are made and customer engineers are freed up, rather than leaving all problems to the customer engineers.
Look at the level of site management
The operation site can reflect the overall execution capacity and level of the plant.