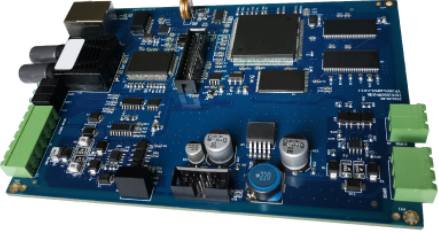
The reason and solution of PCBA welding joint pulling tip
First, the cause of solder joint tip
1. The production process of PCB board
In the manufacturing process of PCB board, copper foil is usually used as a conductive layer, and protective film is coated on the surface of copper foil for etching. If there are problems in the production process, such as incomplete or excessive etching, it will lead to the surface of copper foil is uneven, and the solder joint is pointed.https://www.kingfordpcb.com/yuan.php
2. The leading end of Component is connected with the PCB pad
The tip of the solder joint may also be related to the poor connection of the Component outlet to the PCB pad. If the connection is poor, it will lead to the internal solder joint is not tight enough, and when the solder joint experiences temperature changes or is subjected to external pressure, it is prone to problems such as pinching.
3, process and equipment selection
When processing solder joints, the use of organic green printing ink/chemical gold plating and other unsuitable technology and process will also lead to solder joint tip. Especially in the processing of high density PCB board, if the feeding is not accurate or the printing is not in place, it will cause the problem of pinching the solder joint.
4. Environmental issues
It is rare that the solder joint tip is pulled due to environmental problems. However, some ultra-quiet environments require the use of large air conditioning and dehumidification equipment, which makes the site comfortable and hygienic to achieve the best state, but at the same time leads to the impact of welding reflux and annealing equipment, which indirectly leads to the occurrence of solder joint tip.
Two, how to better solve the PCBA processing solder joint tip
1. Choose the right process and equipment
Choosing the right technology and equipment for welding is the key. Common processes are manual welding and machine welding. Machine welding speed, high degree of automation, suitable for mass production; And manual welding precision is high, suitable for small batch, repair and non-standard products. If you want to deal with high precision electronic products, machine welding is a more ideal choice.
2. Standardized operation process
In PCB board processing and welding, the operation process is also very important. To choose standardized operating process and standardized technology to avoid the occurrence of problems such as solder joint tip caused by improper operation.
3. Advanced welding technology
The use of advanced welding technology can also reduce the problem of solder joint tip. For example, the use of a flowing melting solder ensures that the solder joint is intact and uniform inside, while reducing the production of solder joint tips.
4. Balance strength and toughness
In order to solve the problem of solder joint tip, it can also be solved by balancing the strength and toughness of solder joint. For example, the use of thickened pad, increase the thickness of the inner copper, can ensure the strength of the solder joint while improving the toughness of the solder joint, effectively avoid the problem of the solder joint tip.
Three, PCBA processing solder joint pulling tip is a common problem in electronic production, but through the selection of appropriate technology and equipment, standardized operating process and advanced welding technology, can avoid the generation of solder joint pulling tip. In practice, mastering good technology, strengthening management and reducing the occurrence of such problems can effectively improve the quality of electronic products and prolong the service life of products.
1. First of all, you need a specialSMT machine for SMT SMT processing. Before you begin processing, you need to check the state of the patch machine and ensure that it is working properly. Checking the condition of the patch machine includes cleaning and inspecting all components of the equipment. If you find any damaged or worn parts, they must be replaced promptly. This ensures that your patch machine will run properly, thus increasing productivity.
2. Secondly, you need to prepare all the necessary materials and equipment before SMT patch processing. This includes patch components, circuit boards, solder paste and other auxiliary materials. You should choose good quality materials to ensure the quality and stability of the patch. In addition, you need to ensure that all materials are in sufficient quantities so that there are no shortages during production.
3. In addition to material and equipment preparation, another key preparation work is to set the parameters of the patch machine. These parameters include welding temperature, welding speed and SMT accuracy. Selecting the right parameters can ensure the stability and quality of the patch process. Here, you should set the parameters according to the different characteristics of the board you want as much as possible. The corresponding parameters can be calculated in advance to ensure production efficiency and patch quality.