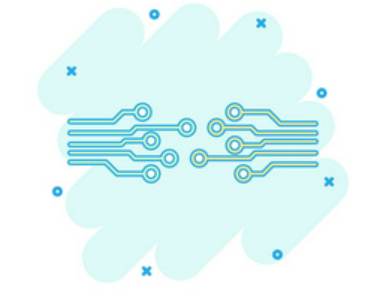
SMT patch processing needs to pay attention to several standard issues must be understood here:
First: Joint standard for the development of electrostatic discharge control procedures. Including electrostatic discharge control program necessary design, establishment, implementation and maintenance. According to the historical experience of some military organizations and commercial organizations, it provides guidance for the treatment and protection of electrostatic discharge during the sensitive period.
Second: Welding technique evaluation manual. Includes 45 articles on all aspects of welding technology, covering general welding, welding materials, manual welding, batch welding, wave soldering, reflux welding, gas phase welding, and infrared welding.
Third: semi-water cleaning manual after welding. Including all aspects of semi-aqueous cleaning, including chemical, production residues, equipment, process, process control, and environmental and safety considerations. Dongguan Xinmon smt machine manufacturer 13 years focus on SMT machine processing, providing Samsung SMT machine processing, Yamaha SMT machine processing, multifunctional SMT machine, SMT machine processing, Panasonic used SMT machine sales.
Fourth: Through hole welding point evaluation desktop reference manual. Detailed description of components, hole wall and weld surface covering as per standard requirements, in addition to computer generated 3D graphics. It covers tin filling, contact Angle, tin dipping, vertical filling, pad covering, and a large number of weld spot defects.
Fifth: Template design guide. Provides guidelines for the design and manufacture of solder paste and surface mount binder coated formforms.I Also discusses the design of formwork using surface mount techniques and describes? Kunhe technology, including overprint, double print and stage template design.
Sixth: water cleaning manual after welding. Description of manufacturing residues, types and properties of hydrogenic cleaners, hydrogenic cleaning processes, equipment and processes, quality control, environmental control, and determination and costs of employee safety and cleanliness.
Cause of PCB circuit boardappearing open circuit and improvement method
1. Open circuit composed of exposed substrate:
1. There is a scratch scene before the copper clad plate enters the library;
2. The copper clad plate is scratched in the process of opening;
3. The copper clad plate is scratched when drilling;
4. The copper clad plate is scratched in the transfer process;
5. When copper is deposited, the appearance of copper foil is injured due to improper operation;
6. The copper foil on the surface of the production plate is scratched in the horizontal machine.
Improvement measures:
1, copper clad plate in the warehouse before IQC must carry out spot inspection, check the surface is not scratched substrate scene, if there should be timely contact with the supplier, according to the actual situation, make appropriate treatment.
2. Copper clad plate is scratched in the process of opening, the primary reason is that there are hard objects on the surface of the opening machine. When opening, copper clad plate and objects friction to form copper foil scratches to form the scene of exposing the substrate, so it is necessary to carefully clean the table before opening, to ensure that the table lubrication without hard objects.
3, the copper clad plate is scratched when drilling, the primary reason is that the main shaft clip is worn, or there is no cleaning and cleaning in the clip, grasp the drill is not strong, the drill does not go to the top, slightly longer than the length of the drill, the height of drilling is not lifted, the machine tool moves when the drill tip scratches the copper foil formation of the substrate scene.
a. The clip can be replaced by the number of times recorded by the grasping knife or according to the wear degree of the clip;
b. Clean the clip regularly according to the working rules to ensure that there is no debris in the clip.
4. The plate is scratched in the transfer process:
a, transfer personnel once lifted the amount of the board is too much, the component is too large, the board is not lifted when transferring, but dragged up along the trend, constitute the board Angle and the board surface conflict and scratch the board surface;
b, put down the plate because of not put regular, in order to rearrange and force to push the plate, constitute the conflict between the plate and the plate and scratch the surface.
5, after copper sinking, the whole plate after electroplating when the accumulation of plates due to improper operation is scratched:
After sinking copper, the whole plate after plating storage plate, because the plate is stacked together, there is a certain number of, the component is not small, and then put down, the Angle of the board down and plus a gravitational acceleration, constitute a strong impact impact on the board surface, the board surface scratches the substrate.
6, the production plate is scratched in the horizontal machine:
a. The baffle plate of the grinding machine sometimes contacts the surface of the plate. The edge of the baffle plate is generally uneven and the beneficial objects are raised, and the surface of the plate is scratched when passing the plate;
b, stainless steel drive shaft, due to damage into a pointed object, when the plate scratches the copper surface and exposed substrate.
To sum up, about the future of the scratch in the copper substrate scene, if on the line is open or line gap in the way to show, simple discrimination; If it is the scratch exposed substrate before sinking copper, and on the line, after sinking copper and sinking on a layer of copper, the thickness of the copper foil line is significantly reduced, behind the open, short circuit test is difficult to check out, so customers may be used because of too much current and constitute the line burned off, potential quality problems and the economic loss is quite large. Two, no hole open circuit:
1. No porosity of sunk copper;
2. The oil in the hole constitutes no porosity;
3. Excessive micro-erosion constitutes no porosity;
4. Poor electroplating constitutes no porosity;
5. Drilling and burning holes or dust plugging holes constitute no porosity.