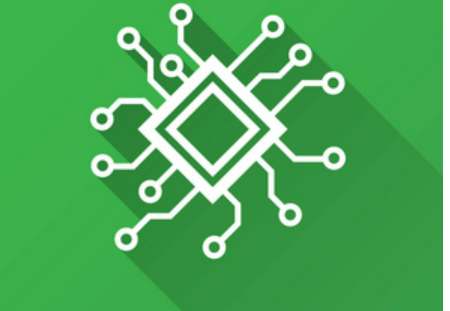
As we all know, industrial robots were first used in the automobile manufacturing industry. Robot technology has developed to now, and the application range is so wide that the automobile industry is still a relatively high density industry of industrial robots. Compared with welding, spraying, handling and other work in the process of automobile production, PCB industry requires higher accuracy of robots, and the work complexity is relatively high. Here are three examples of industrial robots used in PCB industry.
1.SCARA robot is used in circuit board coil detection process
At present, there is almost no complete set of detection equipment for multi-layer coil short circuit on the market, and most of this work still relies on manual completion. PCB board with large aperture is manually put the board on the detection equipment and then open the equipment for detection, while PCB board with small aperture needs manual equipment (probe) to detect each coil. The SCARA robot can be used to complete the loading and unloading and positioning of the detection equipment, and complete the detection of all the coils of the aperture plate at one time. For the small aperture board, SCARA device is used to fix the probe at the executive end. The use is determined to detect each coil with the probe. Our device also effectively avoids the omission caused by the small or large aperture of the coil during manual operation. Compared with manual operation, it can significantly improve the efficiency of detection and avoid quality problems caused by missing detection.
2.DELTA robot is used in the packing process of small circuit board products
At present, the FPC loading work is usually manually picked up one by one and put into the plastic tray. Because the FPC is soft and thin, it is very inconvenient to pick up the FPC. Even experienced workers have a low efficiency in completing this work. The effect is no less than manual. Its speed can reach 60 pieces /min, completely can replace manual sorting and loading, so as to save valuable labor resources, reduce the cost of enterprises.
3.6 Axis industrial robot is used in AOI inspection process
Traditional AOI scanning machines rely on artificial copy, copy and receive board, a worker to watch two scanning machines, repeat this monotonous work every day, and just made the circuit board will emit pungent smell to human body to bring certain harm, AOI scanning machine emit infrared light is also an invisible killer, All these have caused harm to the health of workers. Instead of manual labor, multi-joint robots are used to place, turn and collect two AOI boards. Each shift can complete the collection and release of more than 700 PCB hard boards, and the comprehensive efficiency can reach 1 piece /min(including the scanning time of AOI machine). In the future, if the loading and unloading transport line matched with the retracting machine can be further connected to the AGV for fixed line transport, the complete automatic production of the upper and lower processes can be realized.
With its advantages of high automation, industrial robots are being more and more applied in industrial production lines. With the continuous innovation of industrial robot technology, robots can also ensure high precision in the high-speed production process, which makes robots can make a difference in the PCB industry.
Solution: Parameterized constraints
At present PCB design software suppliers try to solve this problem by adding parameters to constraints. The most advanced aspect of this method is the ability to specify mechanical indicators that fully reflect various internal electrical characteristics. Once these are incorporated into the PCB design, the PCB design software can use this information to control the automatic layout tool.
When the subsequent production process changes, there is no need to re-design the PCB. The PCB designer can automatically change the relevant constraints by simply updating the process characteristic parameters. The PCB designer can then run the DRC(PCB Design Rule Check) to determine if the new process violates any other PCB design rules and to find out what aspects of the PCB design should be changed to correct all errors.
Constraints can be entered in the form of mathematical expressions, including constants, operators, vectors and other PCB design constraints, providing a parameterized rule-driven system for PCB designers. Constraints can even be entered in the form of lookup tables, stored in PCB design files of PCB or schematic diagrams. The PCB routing, copper foil placement and layout tools follow the constraints generated by these conditions, and the DRC verifies that the entire PCB design complies with these constraints, including line width, spacing, and spatial requirements (such as area and height restrictions).