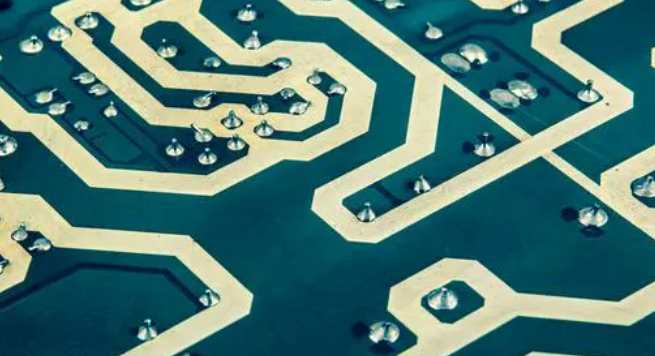
Plastic film generally has good chemical stability, the lack of active groups on the surface, so it is usually difficult to chemical reaction with aluminum layer, chemical bond generation, aluminum plating layer and plastic film is usually produced by intermolecular interaction, so in discussing the bonding fastness between aluminum plating layer and the base film, we need to start from the understanding of the intermolecular action. As we all know, there are van der Waals forces and hydrogen bonds between molecules. The dispersion energy of small molecules is generally 0.8X103-8.4X103J/mol. Hydrogen bond is a weak chemical bond between molecules formed by the functional group AH containing hydrogen in the molecule and the atom B in the adjacent molecule. Its bond energy is 2.ix104-4.x104j /mol. The energy of hydrogen bond is smaller than that of chemical bond, but it is much larger than ordinary van der Waals force.
The main factor affecting the quality of aluminum plating on plastic film is the vacuum degree of evaporation chamber. High level of equipment is the basis of obtaining high barrier aluminized film, without high level of coating equipment, it is impossible to produce high quality aluminized type barrier film. Generally speaking, the higher the vacuum degree, the better the evaporation effect of aluminized film, the higher the density of the coating layer, and the better the barrier property. Therefore, when choosing the forging film equipment, special attention should be paid to the vacuum degree of aluminized vacuum chamber.
In order to improve the bonding fastness between plastic film and aluminum plating layer, the polarity of the surface of plastic film and aluminum plating layer should be enhanced as much as possible, and the ratio of orientation force in their interaction should be increased. The combination between plastic film (especially non-polar plastic film) and aluminum layer lacks strong orientation force, but mainly relies on relatively weak induction force and dispersion force, so the adhesion fastness between them is quite low. The surface molecules have strong polarity and even have functional groups containing hydrogen, so that the surface of the plastic film and the aluminum plating layer may be bonded through large orientation force and hydrogen bonding, which will greatly improve the bonding fastness of the aluminum plating layer.
High quality aluminized film, aluminized layer on the surface of the film, must be firmly attached, so to improve the aluminized film effect, it is required to enhance the adhesion fastness between the aluminized layer and the film surface. The adhesion mechanism, surface properties and influencing factors of BOPET films are briefly introduced here.
In addition to the intermolecular interaction, the mechanical interaction between the aluminized layer and the plastic surface (mechanical anchoring) is also an important factor in the bonding between the aluminized layer and the plastic film. Smooth plastic film surface and aluminum coating adhesion fastness is not good, because the contact area between them is relatively small, and the lack of necessary mechanical anchorage. If the film surface is properly treated, so that it has a certain roughness, so as to obviously enhance the bonding fastness between the aluminum plating layer and the plastic film, of course, the plastic surface roughness needs to be kept within a moderate range, if not properly treated, the surface of the plastic film is too rough, often lead to the shortcomings of aluminum plating can not be completely filled with microholes, but cause adhesion defects. The adhesion of the aluminum coating on the surface of the plastic film is reduced.
3. Control PCB pressing process. After PCB has been pressed and baked, the Tg values of the samples can be measured twice by the same method and the same machine. If the △Tg of Tg2-Tg1 exceeds 2 ~ 3°C (Hardening including polymerization and cross-linking), the hardening reaction (including cross-linking) of the hardening process is not in the hardening position. These unseasoned slabs are prone to water absorption and rupture.
4. Measure the Tg value of the problem board according to TM-650 test manual Section 2.4.24.1 TMA method, and compare with the specification value of the supplier. If the measured value is more than 5°C below the specification value, it indicates that the problem plate has water absorption lesions. The moisture in the resin acts as a plasticizer, which will not only lower Tg, but also make the rubber state arrive earlier.
5. Multi-layer PCBS stored for more than three months may show stress concentration (from pressing) and water absorption (which will increase Z expansion). Explosion-proof baking (105°C+24 hours) before welding is required, or 50 cell phone plates are pressed and baked in nitrogen gas at 185°C+70PSI for 2 hours using a leveler. The client side of the plate more than three months to bake before welding will reduce the plate explosion, baking not only increases the cost and adverse to OSP. When baking, it is necessary to separate a single piece of baking, so as to fully discharge the water.