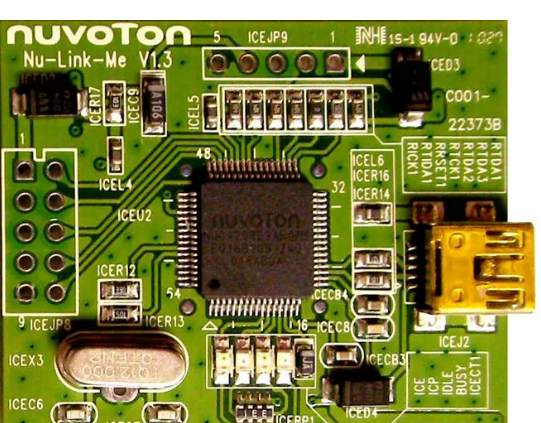
1. What is impedance?
In a circuit with resistors, inductors, and capacitors, the resistance to alternating current is called impedance. Impedance is generally represented by z, which is a complex number. The real part is called resistance and the imaginary part is called reactance. The blocking action of circuit capacitance to AC power is called capacitive reactance, the blocking action of circuit inductance to AC power is called inductive reactance, and the blocking action of circuit capacitance and inductance to AC power is called reactance. The unit of impedance is ohm.
2.(1) Characteristic impedance In computer, wireless communication and other electronic information products, PCB board circuit transmission energy is a square wave signal composed of voltage and time, encountered resistance is called characteristic impedance.
(2) The differential impedance driver inputs two identical signal waveforms of opposite polarity, which are respectively transmitted by two differential lines. The two differential signals are subtracted at the receiving end. Differential impedance is the impedance Zdiff between two wires.
(3) odd-mode impedance The impedance zoo of one of the two lines to the ground. The impedance values of both lines are the same.
(4) even-mode impedance Input two identical signal waveforms with the same polarity to the driving end, and the impedance Zcom when the two lines are connected.
(5) common-mode impedance One of the two lines has the impedance to the ground Zoe, and the impedance value of the two lines is the same, usually greater than the odd-mode impedance.
3. Why must PCB board be impedance?
The impedance of a PCB refers to the resistance and reactance parameters that impede the AC current. Impedance processing is essential in PCB production. The reasons are as follows :(1) The bottom of the PCB circuit board should consider the connection and installation of electronic components, as well as the electrical conductivity and signal transmission performance after connection, so the lower the impedance, the better.
(2) PCB circuit board in the production process, to go through copper plating, tin plating (or chemical tin plating or hot spray tin), connector solder and other processes, the materials used in these processes must ensure low resistivity, to ensure that the overall impedance of the circuit board to meet the product quality requirements, can work normally.
(3) Tin plating of PCB circuit board is the most prone to problems in the whole circuit board manufacturing, and it is a key link affecting the impedance. The biggest defects of electroless tin plating are easy discoloration (easy oxidation or delix) and poor solderability, which can lead to difficulty in soldering the circuit board, and poor or unstable conductivity of the entire circuit board due to high impedance.
(4) There will be a variety of signal transmission in the circuit board conductor, in order to improve its transmission rate, it must improve its frequency. If the circuit itself is different due to etching, stack thickness, line width and other factors, it will cause changes in the impedance value, so that the signal distortion, resulting in the performance of the circuit board, so it is necessary to control the impedance value at a certain level
4. For the electronic industry, according to the industry survey, the most fatal weakness of the chemical tin plating layer is easy to change color (easy oxidation or moisture), poor weldability leads to welding difficulties, high impedance leads to poor electrical conductivity or unstable performance of the entire circuit board, easy to make PCB circuit short circuit or even burn or fire. Many products and their users' electronics (bottom board or whole electronics) have poor performance, and this poor performance is mainly due to impedance problems, because when unqualified electroless tin plating is used, the PCB board is coated not with true pure tin (or pure metal element), but with compound tin (i.e. not metal element at all, It is a metallic compound, oxide or halide, or, more directly, a non-metallic substance), or a mixture of tin compounds and tin group elements, which is difficult to detect with the naked eye. Because the main circuit PCB board copper foil, soldering tin layer, electronic components through solder paste (solder wire) solder tin layer, in fact, solder paste in the molten state of the electronic components and solder layer solder metal tin (that is, good conductivity of the metal), so it can be simply pointed out that the electronic components are connected to the copper foil at the bottom of the tinned PCB board, therefore, The purity and impedance of tinning layer are the key factors. In addition, when we measure impedance directly with the instrument before attaching the electronic component, the ends of the instrument probe (or stylus) are also connected to the current by touching the tin coating on the surface of the copper foil on the bottom of the PCB and then connecting to the copper foil on the bottom of the PCB. Therefore, tin plating is the key, which affects the impedance and performance of the whole PCB, and is also the key which is easy to be ignored. Compounds other than simple metals are known to conduct electricity poorly or not at all (which is also key to the presence of power distribution or transmission capacity in the line). Thus, when this conducting but non-conducting tin compound or mixture is present in the tin coating, the resistivity readily available due to future oxidation and moisture or after electrolytic reaction and the corresponding impedance are quite high (sufficient to affect the level or signal transmission in the digital circuit), and the characteristic impedance is also out of phase. Therefore, it will affect the performance of the circuit board and its complete machine. Therefore, as far as the current social production phenomenon is concerned, the material and performance of PCB bottom coating is the most important and direct reason affecting the characteristic impedance of the entire printed circuit board. However, as the coating ages and changes in water electrolysis, the worrisome effects of its impedance become more insidious and variable. The main reasons are: one is not visible to the naked eye (including its changes), two is not continuous measurement, because it changes with time and ambient humidity. Within the range.