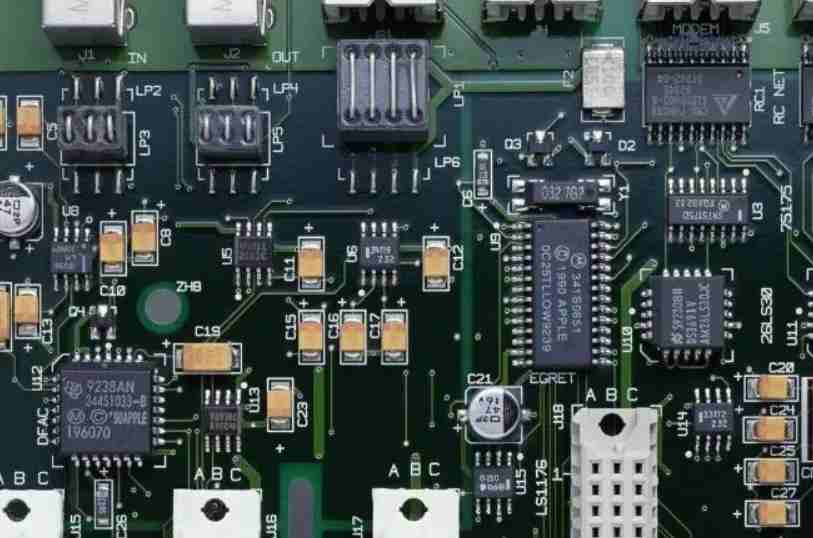
1. The telecommunications engineer of the substrate has selected the specified dielectric constant, dielectric thickness and copper foil thickness according to the needs of the actual impedance during the design. Therefore, when accepting the order, it is necessary to check carefully and meet the design requirements.
2 transmission line production accuracy requirements of high frequency signal transmission, the printed wire impedance requirements are very strict, that is, the production accuracy of the transmission line is generally ±0.02mm (±0.01mm precision transmission line is also very common), the edge of the transmission line to be very neat, small burr, gap are not allowed to produce.
3. The coating requires that the characteristic impedance of high-frequency microwave board transmission line directly affects the transmission quality of microwave signals. And the size of the characteristic impedance has a certain relationship with the thickness of copper foil, especially for the hole metallized microwave plate, the coating thickness not only affects the total thickness of copper foil, but also affects the precision of the wire after etching. Therefore, the size and uniformity of the coating thickness should be strictly controlled.
4. Mechanical processing requirements first of all, high frequency microwave board materials and circuit board epoxy glass cloth materials in machining aspects are very different, followed by high frequency microwave board processing accuracy than printed board requirements are much higher, the general contour tolerance is ±0.1mm (high precision is generally ±0.05mm or 0~-0.1mm).
5. The requirements of characteristic impedance have already talked about the content of characteristic impedance, it is the most basic requirements of high frequency microwave plate, can not meet the requirements of characteristic impedance, everything is in vain.
Problems to be paid attention to in high frequency microwave plate production
1. Processing of engineering data: When CAM processing of customer documents, we must grasp the content of two aspects, one is to carefully understand the production accuracy requirements of transmission line, the other is to make appropriate process compensation according to the accuracy requirements and combined with the manufacturing ability of our factory.
2. Blanking: usually printed board blanking are using shearing machine or automatic cutting machine, but for microwave medium materials can not be generalized, according to the characteristics of different media, and choose different blanking methods, mainly to milling, cutting, so as not to affect the flatness of materials and the quality of the surface.
3. Drilling: For different medium materials, not only the parameters of drilling are different, but also the top Angle, blade length, spiral Angle of the drill have its special requirements, for aluminum, copper based microwave medium materials, drilling processing method is also different, to avoid the generation of burr.
4. Through hole grounding: Under normal circumstances, the conduction hole is grounded by the method of chemical copper sedimentation, chemical copper sedimentation is usually processed by chemical method or plasma method. From the perspective of safety, we use the plasma method, the effect is very good, and for aluminum based microwave dielectric materials, if the use of the usual chemical copper sedimentation, there is considerable difficulty. Generally, it is recommended to use metal conductive material to ground holes, but the hole resistance is generally less than 20.
5. Graphics transfer: This process is an important process to ensure the accuracy of graphics. In the selection of photoresist, wet film, dry film and other sensitive materials, must meet the requirements of graphic accuracy, at the same time, the photolithographic machine or exposure machine light source must also meet the needs of the process.
6. Etching: This process should strictly control the process parameters of etching, such as: the content of each component of etching liquid, the temperature of etching liquid, etching speed, etc. Ensure that wire edges are neat, no burrs, notches, and wire accuracy is within the range of tolerance requirements. To really do this, we need to work hard and it is very necessary.
7. Coating: The final coating on the wire of high frequency microwave board generally includes tin lead alloy, tin indium alloy, tin strontium alloy, silver, gold, etc. But electroplated pure gold is more common.
8. Forming: high frequency microwave plate forming and printed circuit board, CNC milling mainly. But the method of milling is very different for different materials. The milling of metal-based microwave plates requires the use of neutral coolant for cooling, and the milling parameters vary considerably