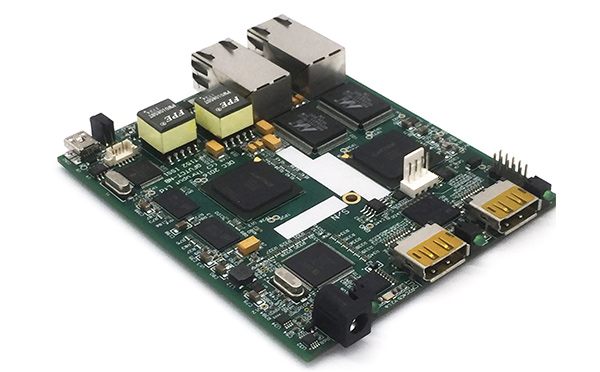
Misconception 1: believe that differential signals do not need ground plane as a backflow path, or think that differential routes provide backflow paths for each other. The reason for this misunderstanding is that the surface phenomenon is confused, or the mechanism of high-speed signal transmission is not deep enough. As can be seen from the structure of the receiving end of FIG. 1-8-15, the emitter currents of transistors Q3 and Q4 are equivalent and opposite, and their currents at the junction exactly cancel each other out (I1=0), so the differential circuit is insensitive to similar bombs and other noise signals that may exist on the power supply and ground plane. Partial backflow cancellation in the ground plane does not mean that the differential circuit does not take the reference plane as the signal return path. In fact, in the analysis of signal backflow, the mechanism of differential routing is the same as that of ordinary single-ended routing, that is, high-frequency signals always backflow along the loop with the smallest inductance. The biggest difference is that the difference lines are coupled to the ground as well as to each other. Whichever coupling is strong becomes the main backflow path.
In PCB circuit design, the coupling between differential routing is generally small, often accounting for only 10~20% of the coupling degree, more or the coupling to the ground, so the main return path of differential routing still exists in the ground plane. When discontinuity occurs in the ground plane, the coupling between differential routes provides the main backflow path in the absence of a reference plane. Although the impact of the discontinuity of the reference plane on the differential routing is not as serious as that on the ordinary single-ended routing, it will still reduce the quality of the differential signal and increase EMI, which should be avoided as far as possible. Some designers believe that the reference plane of the differential line can be removed to suppress part of the common-mode signal in the differential transmission, but this is not desirable theoretically. How to control the impedance? Not providing ground impedance circuit for common-mode signal will inevitably cause EMI radiation, which does more harm than good.
Myth 2: Maintaining equal spacing is more important than matching line length. In the actual PCB routing, the requirements of differential design can not be met at the same time. Due to the presence of pin distribution, hole crossing, wire space and other factors, it is necessary to achieve the purpose of line length matching through appropriate winding, but the result must be that part of the difference pair cannot be parallel. At this time, how should we choose?
The effect of unequal spacing is negligible, whereas the effect of line length mismatch on timing is much greater. From the perspective of theoretical analysis, although the spacing inconsistency will lead to changes in differential impedance, the coupling between difference pairs is not significant, so the range of impedance variation is also small, usually within 10%, which is only equivalent to the reflection caused by a hole, which will not cause significant impact on signal transmission. Once the line length is not matched, in addition to the time sequence deviation, it also introduces common mode components into the differential signal, reducing the quality of the signal and increasing EMI.
It can be said that the most important rule in the design of differential wiring of PCB board is to match the length of the line, and other rules can be flexibly processed according to the design requirements and practical applications.
Mistake three: Think the difference line must be very close. The purpose of having differential lines close together is to enhance their coupling, both to improve immunity to noise and to take full advantage of the opposing polarity of the magnetic field to counteract electromagnetic interference. Although this approach is very favorable in most cases, but not absolute, if we can ensure that they are fully shielded from external interference, then we do not need to achieve the purpose of anti-interference and EMI suppression through the strong coupling of each other. How to ensure that differential routing has good isolation and shielding? It is one of the most basic ways to increase the distance between the lines and other signals. The energy of electromagnetic field decreases with the square relationship between the distance. Generally, when the distance between the lines is more than 4 times the width of the lines, the interference between them will be extremely weak and basically can be ignored. In addition, isolation through the ground plane can also play a good shielding role, this structure is often used in high frequency (10G above) IC packaging PCB design, known as CPW structure, can ensure strict differential impedance control (2Z0).