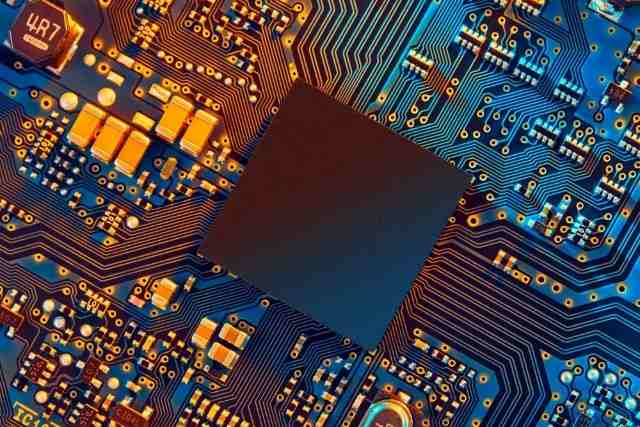
Copper electroplating is the most widely used in order to improve the adhesion of coating and a precoating, copper coating is an important protective decorative coating copper/nickel/chromium system components, flexible and low porosity copper coating, to improve the adhesion and corrosion resistance between the coating plays an important role. Copper plating is also used for local carburizing, metallization of printed board holes, and as a surface layer of printing rollers. Chemically treated layers of colored copper, coated with organic film, can also be used for decoration. In this paper, we will introduce the common problems encountered in PCB process of copper plating technology and their solutions.
First, copper acid plating common problems
Copper sulfate plating plays an extremely important role in PCB plating. The quality of copper plating directly affects the quality and related mechanical properties of copper plating, and has certain influence on the subsequent processing. Therefore, how to control the quality of copper plating is an important link in PCB plating, and also one of the difficult processes in many large factories. Copper acid electroplating common problems, mainly have the following: 1. Rough plating; 2. Electroplating copper granules; 3. Plating pits; 4. The panel is white or uneven in color. In view of the above problems, some summary, and some brief analysis of solutions and preventive measures.
1. Rough plating
Generally rough plate Angle, most is caused by electroplating current is too large, you can lower the current and check whether the current display is abnormal; The whole board is rough, generally will not appear, but the author has met once in the customer, later found out when the winter temperature is low, the content of light agent is insufficient; There are sometimes some rework film board surface treatment is not clean will also appear in a similar situation.
2, plating plate surface copper particle
There are many factors that cause the copper particles to be produced on the surface of the plate. It is possible to electroplate copper itself from the whole process of copper sedimentation, graphic transfer. I have met in a state - owned large factory, caused by copper plate surface copper particles.
Surface copper particles caused by the copper-sinking process may be caused by any of the copper-sinking processes. Alkaline oil removal in the water hardness is higher, more drilling dust (especially the double panel without removal of rubber slag) poor filtration, will not only cause the rough surface, but also cause the rough hole; But generally will only cause the hole rough, the surface of the slight spot dirt micro-erosion can also be removed; There are mainly several cases of microcorrosion: the quality of the used microcorrosion agent hydrogen peroxide or sulfuric acid is too poor or ammonium persulfate (sodium) contains too much impurities, the general recommendation should be at least CP grade, industrial grade in addition to cause other quality failures; The copper content in the micro-etching groove is too high or the temperature is too low, resulting in the slow precipitation of copper sulfate crystal. The tank is cloudy and polluted. Activation liquid is mostly caused by pollution or improper maintenance, such as filter pump leakage, tank liquid proportion is low, copper content is high (activation cylinder use time is too long, more than 3 years), this will produce granular suspension or impurity colloid in the tank, adsorption on the surface or hole wall, at this time will be accompanied by the production of rough hole. Degluing or acceleration: the use of tank liquid for too long turbidity, because now most of the degluing liquid is prepared with fluoroboric acid, so it will attack the glass fiber in FR-4, resulting in the rise of silicate in the tank, calcium salt, in addition to the increase of copper content and tin content in the tank will cause the production of copper particles on the surface. The copper sink itself is mainly caused by the strong activity of the tank liquid, the dust stirred by the air, the small particles suspended in the tank, etc., which can be effectively solved by adjusting the process parameters, increasing or replacing the air filter element, the whole tank filtration, etc. After copper sedimentation, the dilute acid tank of copper plate is temporarily stored. The tank liquid should be kept clean, and the tank liquid should be replaced in time when it is cloudy. The storage time of the copper plate should not be too long, otherwise the surface is easy to oxidize, even in the acidic solution will be oxidized, and the oxide film is more difficult to deal with after oxidation, so the surface will produce copper particles. The above mentioned copper sinking process of the plate surface copper particles, in addition to the board surface oxidation caused by the general distribution on the board surface is more uniform, strong regularity, and the pollution produced here whether conductive or not, will cause the generation of copper plating plate surface copper particles, processing can be used in some small test plate step by step treatment control judgment, for the site fault plate can be solved with a soft brush light brush; Graphic transfer process: development of excess glue (extremely thin residual film plating can also be plated and coated), or after the development cleaning is not clean, or the plate in the graphic transfer after placing time is too long, resulting in different degrees of oxidation of the board, especially the board cleaning poor condition or storage workshop air pollution is heavy. The solution is to strengthen water washing, strengthen the schedule, strengthen the acid oil removal intensity, etc.
Copper acid plating tank itself, at this time its pre-treatment, generally will not cause the surface of the copper particle, because the non-conductive particles caused by the most plate plating or pits. The causes of copper particles on the surface of the copper cylinder can be summarized into several aspects: tank parameter maintenance, production operation, material and process maintenance. In terms of tank parameter maintenance, the content of sulfuric acid is too high, the content of copper is too low, and the temperature of the tank is too low or too high. Especially in the factory without temperature control cooling system, the current density of the tank will decrease. According to normal production process operation, copper powder may be produced in the tank and mixed into the tank.
In the production operation, the current is too large, the splint is bad, the empty pinch point, and the plate in the groove is dissolved by the anode. It will also cause the current of some plates to be too large, resulting in copper powder, falling into the groove, and gradually producing copper particle failure; In terms of materials, the main problems are the content of phosphorus and the uniformity of phosphorus distribution. Production and maintenance is mainly large processing, copper Angle is added into the slot, mainly in large processing, anode cleaning and anode bag cleaning, many factories are not handled well, there are some hidden dangers. The surface of the copper ball should be cleaned and the fresh copper surface should be eroded with hydrogen peroxide. The anode bag should be soaked with hydrogen peroxide sulfate and alkaline solution and cleaned, especially the anode bag should be cleaned with 5-10 micron gap PP filter bag.
3. Plating pits
This defect also causes many processes, from copper plating, graphic transfer, to pre-plating, copper plating and tin plating. The main cause of copper sinking is that the copper sinking hanging basket is poorly cleaned for a long time. In the micro-corrosion, the polluted liquid containing palladium copper will drop from the hanging basket on the surface of the plate, forming pollution. After the copper plate sinking, the spot-like leakage plating is also called pits. Graphics transfer process is mainly caused by equipment maintenance and development cleaning poor, there are many reasons: brush roller suction stick pollution glue stains, blow-dry drying section of wind knife fan viscera, oil dust, etc., the surface of the board film or improper dust removal before printing, development machine development is not clean, poor washing after development, anti-foaming agent containing silicon surface pollution. Electroplating pretreatment, because whether it is acid degreasing agent, micro corrosion, preleaching, the main components of the tank are sulfuric acid, so the water hardness is higher, there will be turbidity, pollution board; Other parts of the company hanging glue is bad, long time will find the glue in the tank at night dissolution and diffusion, pollution tank; These non-conductive particles adsorbed on the surface of the plate may cause different degrees of plating pits for subsequent plating.
4. The PCB board is white or uneven in color
Copper acid plating tank itself may be the following aspects: the air blast tube deviates from the original position, the air stirring is uneven; Filter pump leakage or liquid inlet near the air blast pipe suction air, produce broken air bubble, adsorption on the surface or line, especially transverse line, line Angle; In addition, there may be another point that poor quality cotton core is used, which is not thoroughly treated. The anti-static treatment agent used in the manufacturing process of cotton core contaminates the tank liquid, resulting in plating leakage. In this case, air can be increased, and the liquid surface foam can be cleaned up in time. It is mainly a problem of polish or maintenance, and sometimes it may be a problem of acid cleaning after oil removal, micro-erosion. Copper cylinder polishing agent imbalance, serious organic pollution, tank temperature is too high may cause. Acid oil removal generally will not have cleaning problems, but if the PH value of the water is acidic and more organic matter, especially recycling water, it may cause poor cleaning, uneven corrosion phenomenon; Micro-corrosion mainly consider the content of micro-corrosion agent is too low, the copper content of micro-corrosion liquid is high, and the temperature of the tank is low, which will also cause uneven micro-corrosion on the surface of the plate; In addition, the quality of the cleaning water is poor, the washing time is a little longer or the preleaching acid pollution, the surface may be slightly oxidized after treatment, in the copper tank electroplating, because it is acidic oxidation and the plate is charged into the tank, the oxide is difficult to remove, will also cause the uneven color of the board; In addition, plate contact with the anode bag, uneven anode conduction, anode passivation and other conditions will also cause such defects.