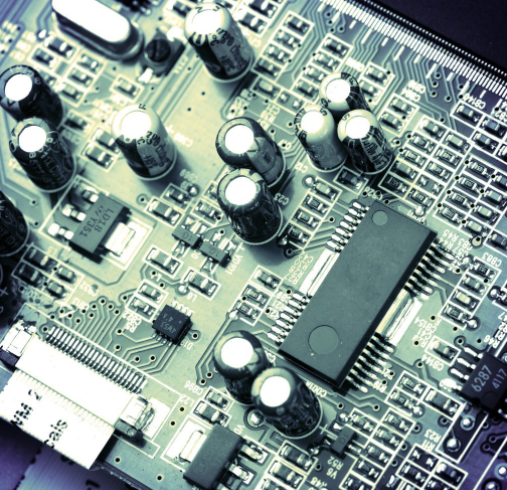
About the Best Aerospace PCB Connector
Gazing at the clear sky at night can be fascinating, even therapeutic. From the perspective of Earth's security, space seems to be quiet and safe. However, for spacecraft, orbits and interplanetary space, the opposite is true. Space environment will cause many hazards to mechanical and electrical systems. These include radiation, extreme temperatures and significant vibrations during flight.
Electronic systems and polychlorinated biphenyls are generally protected from the external effects of spacecraft to some extent, but they are not immune For example, some radiation particles can actually penetrate any data and pose a threat to the circuit board, mainly to prevent the use of radiation electrons These hazards have expanded from single circuit boards and components to larger electronic systems, which means that the selection of aerospace PCB connectors is critical to system performance and reliability
Let's take a look at the challenges of spacecraft circuit board interconnection and how to make the best choice for PCBA design for aviation
Challenges of Spatial PCB Connection
Before discussing the specific challenges of aerospace PCB connectors, it is helpful to understand the working environment of spacecraft. Space includes all heights above or beyond the Earth.
Polychlorinated biphenyls
The earth's atmosphere consists of five layers With the exception of the mid level extending from 50 km (31 mi) to 85 km (53 mi) Each has specific environmental conditions, some of which are dangerous
Harm of PCB connector in space environment
When operating in space, platforms and electronic systems have three main hazards, namely, circuit boards and connectors. These are vibrations and shocks, extreme temperatures and radiation.
1. Vibration hazard
Vibration is the most concerned problem of all spacecraft. Electric shock occurs during emission. The most destructive effects are fracture or data deformation (possibly transient) and data fatigue, which may cause long-term effects.
2. Temperature hazard
For board connectors, the risk of extreme temperature is usually more internal than external. For example, during launch, temperatures higher than 3000 ° C (or close to 6000 ° F) may occur near the rocket engine. These exceed PCBA temperature limits and apply to most data used in avionics systems. In this case, isolation and thermal control system is the key to airborne spacecraft.
3. Radiation hazard
The most dangerous danger in space may be high-energy ionizing radiation, which may appear in any atmosphere outside the Earth. Some radiation particles can penetrate almost any data and lead to charge accumulation on conductive elements or atomic dislocation, thus affecting the function of equipment. Similar to vibration and shock, single event effects (see) or problems may occur.
Once you understand the hazards of aerospace PCB connectors, a set of guidelines will help you make the best choice.
There are many PCBA connectors available, and choosing the best type for your application is not a simple recommendation. Connector selection cannot be performed in isolation. In order to optimize signal transmission/reception and power transmission, it is necessary to know the connector type of PCBA or electronic equipment that the circuit board must be connected to. There are also some physical issues, such as housing clearances and wiring, and alignment of cable or connector holes.
In addition, since the connector is a circuit board assembly, it must comply with the aviation and aerospace industry standards made by PCBA. This compliance includes ensuring that the test requirements for adequate space class connectors are met. Recall that selecting the best pipe of aerospace connector for your design requires you to combine all of the following:
Precautions for selecting aerospace PCB connector
1. Regulatory Requirements
Connectors used on aerospace platforms must meet the data requirements specified in EIA/ECA-364-18B and standard EIA-364-13E below. As mentioned above, connectors are used for fitting and non fitting, continuity during mechanical shock EIA-364-27C and other test programs based on the installation environment.
2. External environmental conditions
For external cables and connectors, temperature range and radiation exposure are the main considerations.
3. Internal environmental conditions
Internal environmental problems include temperature range, humidity, environmental electromagnetic interference and external radiation that may penetrate the interior of spacecraft.
4. Operational requirements
For most spacecraft, electronic systems, including connectors, cannot be repaired or replaced. Therefore, clear service life operation requirements must be formulated and used when selecting the best connector.
Working in space can be dangerous; The strict regulations formulated by the aviation and aerospace industry must be observed. The main considerations affecting connector decisions include evaluating the internal and external environment of the spacecraft and whether the PCBA is part of a mission critical system.
In addition to the above considerations, parts supply chain management may also be a major issue.
In Beat Automation, we cooperate with the most reliable supplier in the industry, and use the digital data supply chain to track and monitor the supplier's components and the entire construction process. This reliable supply chain can ensure the availability and security of components, and comply with aviation regulations and QMS tracking requirements.
To help you start building the best path for the circuit board, we provide you with information about DFM checking, and allow you to easily view and download DRC files. If you are a user of Altium Designer or Cadence Allegro, you only need to add these files to the PCB design software. For Mentor Pad or other design packages, we provide DRC information in different CAD formats and Excel.
If you are ready for manufacturing design, please try our quotation tool to upload your CAD and BOM files If you want to know more about the selection of aerospace PCB connectors for your design, contact us