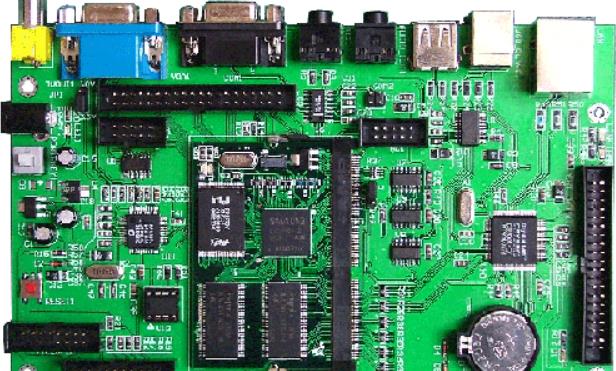
SMT chip processing measures to improve data loss
Data loss in the process SMT chip production and processing has always been one of the key controls of the production manager, which is also a problem that needs continuous improvement Although this industry has developed for decades, there are still many aspects to be improved and controlled Especially in today's increasingly fierce competition, it is particularly important to control data loss
SMT chip processing measures to improve data loss
The control and management of SMT wafer processing data loss are mainly divided into two aspects:
Data management and control:
Whether it is provided to customers or purchased by themselves, good management is required. This is an important principle to ensure material safety and normal production.
1. The feeding amount is incorrect.
Improvement method: In addition to complete packaging, all unopened materials and all other incoming materials shall be checked in detail, and the inventory point shall be used to ensure the accuracy of incoming material data.
2. Quality requirements, unreasonable purchase packaging, different data sizes, poor appearance, different pins.
Improvement method: IQC checks all data before storage to ensure the quality. The storage must be good and the packaging must meet the requirements.
3. Material confusion, customer composition, household goods and customer material confusion.
Improvement method: separate warehouse management, formulate and improve warehouse management process, classify and store all materials, and clearly identify them.
4. The data is stored for longer than the service life of the data, becoming stagnant data and reporting waste.
Improvement method: strictly follow the principle of "first in, first out" to distribute and use all data, and control the early warning mechanism of data cycle.
5. The humidity in the warehouse is very high, and the materials will absorb moisture in the air, resulting in poor material recovery.
Improvement method: use electronic thermometer and hygrometer to immediately monitor whether the temperature and humidity of the warehouse meet the requirements, check twice a day, and add air conditioning and ventilation equipment.
6. The inventory data is inconsistent with the actual data due to operation errors.
Improvement method: warehouse data can be controlled by intelligent warehouse management systems (such as ERP and MES) to ensure the consistency of "subject" and "object";
7. Repair consumables and report waste loss.
Improvement method: develop and maintain data, notify the waste management mechanism, lead the recall process, use old data and reduce losses.
In the process of patch processing, the above management is the basis for reducing data loss, and is also an indispensable requirement for data control. If it is not done well, we should strengthen the control of material loss.
Process control:
SMT chip production process through file specification, operation training, process management, data use control, so as to reduce the loss of data in the production process.
1. The paper feeder has defects, such as dirty paper, deformed cover, and stuck gear, resulting in material loss.
Improvement method: Maintain the paper feeder regularly and provide maintenance files. The maintenance personnel shall comply with the archive requirements one by one, and require maintenance records and confirmation to ensure the correct use of online feeders.
2. The nozzle has defects, such as warping, blocking, damage, vacuum leakage, poor data recovery, poor image recognition and casting.
Improvement method: regularly maintain the cigarette holder, require scientific and technical personnel to check the equipment every day, test the nozzle center, and regularly maintain the equipment as planned.
3. The operator received the goods irregularly. For example, the data is incorrectly installed, thrown and distorted.
Improvement method: create operation standard files, graphic display, operator induction training, and regularly check the work effect of operators.
4. The receiving port is bad. When you connect the machine to the receiving port, the receiving port will always drop.
Reinforcement method: use adhesive tape or copper tape.
5. Material loss. The order has been offline, resulting in material loss.
Improvement method: train operators to protect materials before feeder and after removing materials. You can use masking tape to paste materials.
6. The vacuum pressure is insufficient and the vacuum degree is poor (there is oil stain on the pipe).
Improvement method: develop checkpoint mechanism. Every day, there are special personnel to check as required, and some people will check.
7. The operator did not carefully turn over the circuit board.
Improvement method: The file requires the engineer to make the marking point simple by making a printer/installer, and check it by searching IPQC.
8. The production of fork plate causes the loss of fork plate data.
Improvement method: the engineer skips the fork plate program, and another engineer helps to check, and paste one or two at the same time to confirm whether the fork plate has data.
9. If the data is wrong, the data is wrong when replacing the product.
Improvement method: two operators check all data, IPQC checks data, produces cardboard, and produces the first functional part.
10. The operator does not care about the wrong material or the wrong material in the operation process when receiving the wrong material.
Improvement method: formulate refueling program, make refueling records, check IPQC data, and measure values.
11. More expensive production lines, such as PCB, IC chips, structural parts and molded parts.
Improvement method: all valuable materials shall be delivered to the production line at a ratio of 1:1, and delivered to the white night shift, and distribution and delivery records shall be recorded.
12. Unqualified products such as uneven materials and rusty pins will lead to poor identification.
Improvement method: Echo IQC shall communicate with the supplier, replace the data and compensate for the loss.
13. The film is too sticky, and the information will stick to the tape when it is rolled up. The film is wider than the slit, and the paper feeding is poor.
Improvement method: replace data, echo process engineers use temporary solutions, echo IQC communicates with suppliers, replace data, and make up for losses.
14. The patch plan is wrong. It should be released in a certain location, but it should be released in location B or BOM update.
Improvement method: when writing the program, ask the programmer to check the bill of materials and drawings, generate the measured value of the carton, and paste the first function.
15. ECN is not running correctly, information cannot be transmitted correctly.
Improvement method: ECN shall be reviewed and confirmed by production, engineering and quality departments.
16. Incorrect use of alternate data.
Improvement method: a detailed list of alternative relations or alternative data relations shall be listed in the bill of materials. The alternative data shall be used separately and supervised by the quality department.
17. Bulk materials are not used in time, which leads to bulk materials piling up and failure to distinguish customers, products, work orders, etc.
Improvement method: This file requires that all "daily closed" bulk data have release data records, bulk data use records and IPQC confirmation.
18. Missing plastic sheet.
Improvement method: The plastic plate patch does not include valuable data. Except for the resistance part, other data are used as bulk data.
19. Problems in other integrated equipment categories, such as damaged air valves, worn seals, and skid cables.
Improvement method: establish equipment maintenance specification files, and regularly maintain equipment as required.
20. The 5S workshop is not good, the dust prevention facilities are poor, there is too much dust, the machine is easy to get dirty, and the site environment is not good.
Solution: Develop 5S standards, do 5S work every day, and someone will implement and check. It is forbidden to use air gun to purge electrical equipment and data, and the dust removal capacity of carpet shall be increased. Workshop door.
21. The ESD anti-static protection measures of SMT factory are not good, resulting in the electrostatic decomposition of IC chips.
Improvement method: all equipment must be well grounded and regularly inspected and tested.
22. The control of temperature and humidity is not good and the implementation is not in place, which causes the material to be affected with moisture.
Improvement method: formulate the control specification file of humidity control elements, make the humidity sensor control card, and supervise the implementation.
SMT data management and production process control can effectively reduce data loss and control material cost during SMT chip processing This also means that in terms of cost control, it will virtually generate revenue for the company