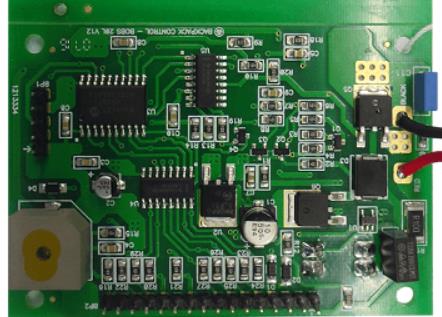
Typical implementation method of 5S in SMT factory
What is a typical 5S implementation method? SMT factory
-, establish a promotion organization
5S is not an activity that employees spontaneously clean up according to their own understanding. In order to carry out 5S thoroughly and continuously, it is necessary to promote the organization and management of 5S activities, and the promotion organization is responsible for promoting 5S activities. Formulate activity plans, formulate various standards and regulations, supervise and inspect, evaluate and compete. Create a climax for the activity and so on.
What is a typical 5S implementation method? SMT processing plant
2. Establish demonstration area
The implementation of 5S can start from the demonstration area. First, select an area as the demonstration area, focus on 5S improvement in this area, and then require other areas to carry out 5S work according to the demonstration area. Since the demonstration area is the object of learning in other fields, the improvement of the demonstration area must be thorough, so that the 5S level of the demonstration area can reach a higher level, so that employees can realize the importance of implementing 5S and themselves from the improvement results of the demonstration area. Workplace gaps.
Improvement is breaking the status quo. It needs to find the existing problems on the basis of accurately grasping the current situation. The purpose of 5S is to improve the workplace. Recognizing the problems in the current workplace is also a prerequisite for implementing 5S improvement and achieving good results. Some problems are easy to find, such as garbage on the ground, dust on the table and disorderly stacking. After the initial sorting, rectification and cleaning, and after the obvious problems have been solved, how to further do 5S work often confuses employees, which requires them to cultivate problem awareness.
First of all, focus on improving the demonstration area, which not only allows employees to see the improvement results as soon as possible, unify their understanding, and eliminate doubts, but also is an effective means to educate employees and improve their awareness of problems. This face-to-face approach is an effective method adopted by many companies that successfully implement 5S.
Circuit board
3. Problems found during patrol
Under the arrangement of the promotion organization, the employee representatives of each department or the company leaders of the promotion organization leaders inspected the whole company, pointed out the existing problems, and required improvement within a time limit. When employees are not aware of problems at the early stage of 5S implementation, this method of finding problems through inspection can play a very positive role in the promotion of activities and should be used frequently.
Work to be done during inspection to find problems:
-Point out the existing problems;
Provide guidance on improvement methods;
– On site coordination on solving cross departmental problems;
Improvement of supervision problems.
During the inspection, the problems and improvement requirements pointed out shall be recorded to make them traceable, so as to supervise the improvement of the problems pointed out.
4、 Fixed point photos
The so-called fixed point photography refers to taking pictures and comparing the situation before and after the improvement of the problem points.
When shooting fixed point photography, please pay attention to the following points:
(1) The photographer stands in the same position back and forth;
(2) Face the same direction;
(3) If the camera is a zoom lens, use the same focal length;
(4) It's better to print the date on the photo.
The difference between the two photos taken before and after the improvement should only be the situation before and after the improvement reflected in the photos and the date of taking the photos.
After printing two photos, paste them together and provide necessary text description of the situation before and after improvement. You can put these photos on the 5S bulletin board. This can not only enhance the pride of the employees who implement the improvement, but also intuitively tell other employees what is good and what is bad, which is helpful to cultivate employees' awareness of problems.
What is a typical 5S implementation method? SMT patch factory
5. Question list activity (red card fight)
The questionnaire is a reminder about the size of playing cards. The practice of the problem ticket activity is to post the problem ticket on the problem point and urge the person in charge to make improvement. Sometimes, to make the problem notice more alert, it is printed in red. This is also called red card operation.
The above is the explanation given by the editor of pcb circuit board company.
If you want to know more about PCBA, you can go to our company's home page to learn about it.
In addition, our company also sells various circuit boards,
High frequency circuit board and SMT chip are waiting for your presence again.