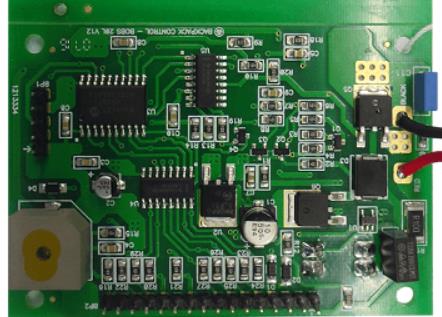
Cause and solution of data loss in polychlorinated biphenyl production
The factors in SMT data loss can be comprehensively analyzed by PCBA factory personnel. Machines, data and links are as follows:
A. Human factors
1. When installing the data, the scientific and technical operators related to SMT chip processing tear the tape too long and press too much, resulting in data loss;
Solution: PCBA manufacturers provide professional technical operation training for SMT technical personnel. When SMT technicians load, two to three spaces shall be reserved. In the pressing window, you can see that the material is normal, and check the feeder gear position and roll tension.
2. Impurities on the table after the feeder is installed cause the positioning is not in place and cannot be taken out when shaking;
Solution: PCBA manufacturers provide professional technical training to SMT technicians. SMT technicians check whether there are any impurities on the machine tool workbench and feeder base when installing the feeder, and clean the machine tool workbench when pulling.
3. The tray of SMT equipment is not installed on the feeder, which causes the disk and the feeder belt to float and throw high;
Solution: PCBA manufacturers need to strictly require SMT technicians to load the data tray onto the feeder when changing data.
4. Failure to unload the coiling belt in time, resulting in tension change, no coiling, poor feeding, floating and throwing of the feeding belt;
Solution: PCBA manufacturer strictly requires the operator to clean the roll when changing information
5. Loss caused by placement of backboard, springboard, wiper board, etc.
Solution: SMT chip processing factory strictly requires SMT technology operators to operate according to the operating instructions, indicating the position of the puzzle, the direction of entering the circuit board and precautions.
6. Check the wrong material station or P/N, which causes the error;
Solution: PCBA processing plant needs to train SMT technology operators to check material P/N, machine alarm display and unloading table position.
7. The data quantity is incorrect, there are too many PCBAs, and the data tray for misuse is lost;
Solution: ask the material team to check the production quantity and storage quantity of all materials, PCBA and PCBA in the production line.
8. Incorrect package parameters are set in the edited program, and the used feeding quantity does not match the package spacing, resulting in throwing;
Solution: Modify packaging data according to material packaging.
9. Before SMT chip processing operation, errors may be caused by incorrect installation position and station settings in the program edited by SMT technology operators.
Solution: Check the BOM and drawings when running the program, and extend the first check panel to reconfirm the BOM and drawings.
10. The throwing technical personnel did not follow up the throwing due to the feeder, nozzle and materials, and the data led to a large number of throwing during the processing and production of PCBA.
Solution: The patch processing and online scientific and technical personnel are required to monitor the running state of the machine immediately, and conduct on-site processing and observation when the machine alarms. The hourly throwing report must be signed by SMT technical personnel to confirm and prepare improvement measures. If there is a signature to confirm the report that has not been processed for two hours, it must be resolved and reported to the assistant engineer for processing.
11. Feeder cover not fastened correctly, feeder not checked
Solution: Smt film factory requires Smt technology operators to work according to WI requirements, check the feeder before and after installation, and scientific and technical personnel and management personnel check and confirm.
12. The feeder overlaps at will, causing deformation, and the feeder stops are dismantled and placed at will;
Solution: SMT technicians must be required to place all feeders in the feeder car. It is not allowed to overlap, randomly place and disassemble feeder accessories in the following lines.
13. The defective feeder is not sent for repair and reuse in time, resulting in throwing;
Solution: PCB factory requires SMT technology operators to clearly identify all damaged feeders and send them to feeder repair station for repair and correction.
Polychlorinated biphenyls
B. Machine factors
1. Nozzle deformation, blockage, damage, low vacuum pressure, air leakage, resulting in material not being sucked out, incorrect reclaiming, identification failure, and material being thrown out.
Solution: PCBA processing plant requires Shenzhen SMT technical personnel to inspect SMT equipment, test nozzle center, clean nozzle, and maintain SMT equipment regularly according to the plan.
2. Insufficient spring tension, inconsistent nozzle and support, resulting in poor feeding;
Solution: Maintain SMT equipment regularly according to the schedule, check and replace fragile parts.
3. The support/shaft or piston is deformed, the nozzle is bent, and the nozzle is worn and shortened, resulting in poor feeding;
Solution: PCBA manufacturer's SMT workshop equipment shall be regularly maintained as planned, and vulnerable parts shall be inspected and replaced.
4. The data is not in the data center, and the data height is incorrect (usually 0.05MM is the lowest pressure after encountering the part), resulting in offset, incorrect and offset. During identification, the identification system discards it as invalid data because it does not match the corresponding data parameters.
Solution: PCBA manufacturer regularly maintains SMT equipment as planned, checks and replaces fragile parts, and corrects the source of the machine.
5. The vacuum valve, dirty vacuum filter element, and foreign matters blocking the vacuum gas pipe channel are not smooth, and the vacuum is insufficient during suction, which causes the SMT equipment to run at the speed leading to poor feeding;
Solution: PCBA manufacturer requires SMT technicians to clean the nozzle every day and maintain SMT equipment regularly as planned.
6. Excessive vibration caused by the non leveling positioning of the machine and the resonance between the machine and the feeder, resulting in poor feeding;
Solution: Smt workshop shall regularly maintain the equipment as planned, and check the level fixing support nuts of the equipment.
7. Looseness and wear of screw and bearing will cause vibration, stroke change and poor data selection during operation.
Solution: It is strictly prohibited to use the air gun inside the blower to prevent dust, impurities and parts from adhering to the screw. Smt workshop shall regularly maintain Smt equipment, and inspect and replace vulnerable parts as planned.
8. Motor bearing wear, card reader and amplifier aging lead to machine origin change, inaccurate operation data and poor data collection;
Solution: PCBA manufacturer regularly maintains SMT equipment as planned, checks and replaces fragile parts, and corrects the source of the machine.
9. The vision, laser lens and nozzle reflector are not clean, and impurities interfere with camera identification, resulting in poor handling;
Solution: SMT technicians need to check the SMT equipment every day, test the nozzle center, clean the nozzle, and regularly maintain the SMT equipment according to the schedule.
10. Improper selection of light source, aging of light intensity of lamps and insufficient gray level lead to poor treatment.
Solution: Shenzhen SMT PCBA manufacturer regularly maintains SMT equipment, tests the brightness of cameras and lamps, and checks and replaces fragile parts.
11. Poor treatment due to aging, carbon deposition, abrasion and scratch of reflecting prism;
Solution: PCBA manufacturers regularly maintain SMT equipment, check and replace fragile parts.
12. Insufficient air pressure, vacuum leakage causes insufficient air pressure, which cannot be picked up or dropped during pasting.
Solution: PCBA manufacturers regularly maintain SMT equipment, check and replace fragile parts.
13. The deformation of the feeder cover and insufficient spring tension cause that the belt will not be stuck on the main shaft gear of the feeder, nor will it roll or throw.
Solution: SMT processing plant requires SMT technology operators to clearly identify all damaged feeders and send them to feeder maintenance station for maintenance, correction, inspection and replacement of vulnerable parts.
14. Poor discrimination due to camera looseness and aging;
Solution: PCBA Shiyan SMT Factory regularly maintains SMT equipment as planned, checks and replaces vulnerable parts.
15. The spiral gear, driving claw and locating claw of the feeder are worn, the power is poor, and the motor of the feeder is poor, resulting in the feeder can not be taken out or thrown away.
Solution: Shenzhen SMT Chip Processing Factory requires SMT technicians to clearly identify all defective feeders and send them to the feeder maintenance station for maintenance, correction, inspection and replacement of vulnerable parts
16. The feeding platform of SMT process equipment is worn, resulting in loose feeding after installation and poor feeding;
Solution: Maintain SMT equipment regularly according to the schedule, check and replace fragile parts.
C. Major causes
1. Unqualified products such as dirty and damaged parts, irregular incoming materials and oxidized pins lead to poor identification.
Solution: Echo IQC communicates with suppliers to replace data.
2. The component is magnetized, the package of the component is too tight, and the friction of the data frame is too large to absorb the component.
Solution: Echo IQC communicates with suppliers to replace data.
3. Various dimensions, spacing and orientation of components or packages may lead to poor data selection and identification.
Solution: Echo IQC communicates with suppliers to replace data. When feeding, the packaging and body shape of the same part number data must be checked.
4. Component magnetization and adhesive tape are too strong. When winding the tape, the information is attached to the tape.
Solution: The responsible person of PCBA factory responded to IQC and communicated with the supplier about the replacement data.
5. The suction surface of the filter element is too small, resulting in poor material extraction.
Solution: Echo IQC communicates with suppliers, changes data, and reduces machine speed.
6. The data aperture of the filling element is too large, and the element size does not match the packaging size, resulting in side up, overturning, wrong position and poor feeding.
7. The error between the feeding hole and the feeding hole of the belt is large, and the suction position changes after refueling.
8. The tension of the winding tape is different. If it is not wound, it is too soft to stretch. It's too brittle to pull out easily.
9. The feeding package is not standardized, and the machine cannot be installed in bulk.
Solution: Shiyan SMT Factory responded to IQC's communication with suppliers to replace data.
D. Operation method
1. The data cannot be retrieved due to the incorrect use of feeders, tape chutes and tape chutes of different packaging models;
Solution: Train SMT technology operators to identify data packaging and feeder selection.
2. The wrong feeder of different specifications is used. 0802 feeder is used for 0603 material, 0804 feeder is used for 0402 material, 1.3MM is used for 0603 material, 1.0MM is used for 0402 material, 1.0MM is used for 0805 material, and 1.0MM is used to adjust the feeder to make the material unavailable;
Solution: PCBA manufacturers train SMT technical personnel to determine the size, shape and feed cover selection of materials.
3. Smt technology operators of PCBA factory did not work according to the standard of operation instructions.
Solution: The manufacturer of PAC board strictly requires SMT technicians to work according to the standard operating instructions, regularly evaluate their operating skills, and manage supervision and evaluation.
4. Poor feeding, belt bending, belt tension too tight, holes in the belt, resulting in poor feeding of the upper gear;
Solution: PCB factory strictly requires SMT technical personnel to work according to standard operating instructions, train and evaluate operating skills, and manage supervision and evaluation.
5. The tension of the winding belt is insufficient, and the winding belt is not installed according to the standard, resulting in no winding belt;
Solution: SMt chip processing factory strictly requires SMt technology operators to work according to standard operation instructions, train and assess operation skills, manage, supervise and assess.
6. The data cannot be retrieved because there is space after installation.
Solution: SMT film factory strictly requires SMT scientific and technical personnel to work according to standard operating instructions, train inspection and operation skills, and manage supervision and evaluation.
E. Production environment
1. SMT workshop has high temperature and insufficient humidity, resulting in dust and static electricity when materials are dried.
Solution: PCBA monitors the temperature and humidity of the workshop in real time, and adds air conditioners and humidifiers.
2. The warehouse of workshop and SMT film factory has high humidity, and the data absorbs moisture from the air, resulting in poor data selection.
Solution: PCBA immediately monitors the temperature and humidity of workshops and warehouses, and adds air conditioning and ventilation equipment.
3. SMT workshop of PCB factory has poor sealing performance, poor dust prevention facilities, and excessive dust, which is easy to cause machine dirt and vacuum blockage.
Solution: It is strictly prohibited to use air gun hair dryer, electrical equipment and data in SMT workshop of SMT factory. Carpet dedusting was added at the entrance of the store.
4. The loading platform and feeder trucks are insufficient, resulting in irregular loading, feeder damage and deformation.
Solution: PCBA manufacturer in SMT workshop, add loading platform and feeder truck, and work in strict accordance with WI requirements