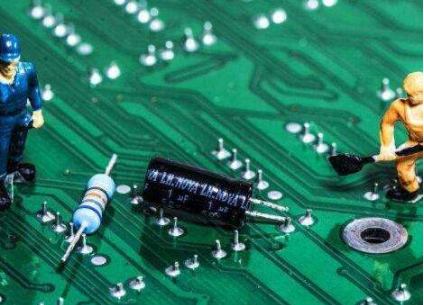
The welding quality of PCB component solder joints is a key factor that directly affects the quality of printed circuit assembly (PWA) and even the whole machine. It is affected by many parameters, such as solder paste, substrate, solderability of components, silk screen, mounting accuracy and welding process. In the process of SMT process research and production, we know that reasonable surface assembly technology plays a vital role in controlling and improving SMT production quality. This paper analyzes the mechanism of several typical welding defects encountered, and puts forward corresponding solutions.
2. Several Typical PCB Welding Defects and Solutions
2.1 Solder balls in wave soldering and reflow soldering
The existence of solder balls indicates that the PCB process is not completely correct, and there is a risk of short circuit in electronic products, so it needs to be eliminated. The internationally recognized standard for the existence of solder balls is that no more than 5 solder balls can appear in the 600 range of printed circuit components. There are many reasons for tin balls, and the root of the problem needs to be found.
2.1.1 Solder balls in wave soldering
Solder balls often appear in wave soldering for two main reasons. First, when soldering a printed circuit board, the moisture near the through-hole on the printed circuit board becomes steam due to heating. If the metal coating on the hole wall is thin or has gaps, water vapor will be discharged through the hole wall. If there is solder in the hole, when the solder solidifies, water vapor will create gaps (pinholes) in the solder, or extrude solder to produce solder balls on the front of the printed board. Second, the solder balls generated on the reverse side of the PCB (i.e. the side contacting the wave crest) are caused by improper setting of some process parameters during wave soldering. If the flux coating amount is increased or the preheating temperature is set too low, the evaporation of the components in the flux may be affected. When the PCB enters the wave peak, the excess flux will be vaporized at high temperature, splashed out from the tin bath, and produce irregular solder balls on the PCB surface. For the above two reasons, we take the following corresponding solutions: First, it is critical to have a proper thickness of metal coating in the through-hole. The minimum copper coating on the hole wall should be 25um, and there should be no gaps. Second, use spray or foam type coating flux. In the foaming mode, when adjusting the air content of the flux, the smallest bubbles should be generated as far as possible, and the contact surface between foam and PCB should be relatively reduced. Third, the preheating zone temperature of the wave soldering machine shall be set so that the top surface temperature of the circuit board reaches at least 100 ° C. Proper preheating temperature can not only eliminate solder balls, but also avoid PCB deformation due to thermal shock.
2.1.2 Solder balls in reflow soldering
2.1.2.1 Mechanism of solder ball formation in reflow soldering
Solder balls from reflow soldering are often hidden on the side between two ends of rectangular chip components or between thin pitch pins. In the component mounting process, the solder paste is placed between the pin and the pad of the chip component. As the printed circuit board passes through the reflow soldering furnace, the solder paste melts into liquid. If it is not well wetted with the pad and the device pin, the liquid solder will cause insufficient weld filling due to shrinkage, and all solder particles cannot converge into a solder joint. Some liquid solder will flow out of the weld to form solder balls. Therefore, the poor wettability of solder with solder pads and device pins is the fundamental reason for the formation of solder balls.
2.1.2.2 Cause analysis and control methods
There are many reasons for poor wettability of soldering tin. The following mainly analyzes the reasons related to relevant processes and solutions:
a) The reflux temperature curve is set improperly. The reflow of solder paste is a function of temperature and time. If the temperature or time is not enough, the solder paste will not reflow. The temperature in the preheating zone rises too fast and the time to reach the flat top temperature is too short, so that the moisture and solvent in the solder paste are not completely volatilized. When reaching the reflow temperature zone, the moisture and solvent will boil and the solder ball will be splashed. The practice has proved that it is ideal to control the rising speed of preheating zone temperature at 1~4 ° C/s.
b) If the solder balls always appear in the same position, it is necessary to check the sheet metal design structure. The corrosion accuracy of the opening size of the template does not meet the requirements, and the size of the bonding pad is too large, and the surface material is soft (such as copper template), which causes the outline of the solder paste that is missed to print is not clear and bridging with each other. This often occurs when the bonding pad of the device with fine spacing is missed to print, and a large number of solder beads between the pins will inevitably be produced after reflow soldering. Therefore, according to the different shapes and center distances of pad graphics, appropriate template materials and template manufacturing processes should be selected to ensure the quality of solder paste printing.
c) If the time from the patch to reflow soldering is too long, the solder paste will not reflow and the solder ball will be produced due to the oxidation of solder particles in the solder paste, the deterioration of the flux and the reduction of its activity. Choosing a solder paste with a longer working life (we think at least 4 hours) will reduce this effect.
d) In addition, the printed board with solder paste misprinted is not cleaned sufficiently, so that solder paste remains on the surface of the printed board and in the through-hole. Before reflow soldering, the components to be pasted shall be re aligned and pasted to deform the solder paste. This is also the cause of the solder ball.
Therefore, it is necessary to strengthen the sense of responsibility of operators and process personnel in the production process, strictly follow the process requirements and operating procedures, and strengthen the quality control of the process.
2.2 Standing problem (Manhattan phenomenon)
One end of the rectangular chip component is welded to the pad, while the other end is tilted. This phenomenon is called Manhattan phenomenon. The main reason for this phenomenon is that the two ends of the element are heated unevenly and the solder paste melts successively. The following conditions may cause uneven heat at both ends of the element:
a) Defective element arrangement direction design. We imagine that there is a reflow welding limit line across the width of the furnace in the reflow welding furnace. Once the solder paste passes through it, it will melt immediately. One end of the rectangular chip element first passes through the limit wire and then flow soldering, the PCB solder paste melts first, completely soaks the metal surface of the element, and has liquid surface tension; The other end does not reach the liquid phase temperature of 183 ° C, the solder paste is not melted, and only the bonding force of the flux is, which is far less than the surface tension of reflow solder paste, so that the element end at the unmelted end is upright. Therefore, keep both ends of the component in the reflow welding limit line at the same time, so that the solder paste on the pads at both ends can be melted at the same time to form a balanced liquid surface tension, so as to keep the component position unchanged.
b) Insufficient preheating of printed circuit components during vapor phase welding. Vapor phase welding uses inert liquid vapor to condense on component pins and PCB pads, releasing heat to melt solder paste. Vapor phase welding is divided into equilibrium area and saturated steam area. The welding temperature in the saturated steam area is as high as 217 ° C. During production, we found that if the components to be welded are not preheated sufficiently and undergo a temperature difference of more than 100 degrees, the vaporization force of vapor phase welding is easy to float the chip components with a package size less than 1206, resulting in the phenomenon of vertical pieces. By preheating the components to be welded in the high-low box at 145 ° C-150 ° C for 1-2 minutes, then preheating them in the equilibrium zone of vapor phase welding for about 1 minute, and finally slowly entering the saturated steam zone for welding, we finally eliminated the vertical sheet phenomenon.
c) The influence of pad design quality. If the size of a pair of pads of chip components is different or asymmetrical, the amount of solder paste that is missed will also be inconsistent. Small pads respond quickly to temperature, and the solder paste on them is easy to melt, while large pads are on the contrary. Therefore, when the solder paste on small pads melts, the components will be straightened and erected under the effect of the surface tension of the solder paste. If the width or gap of the pad is too large, it may also be vertical. The pad design in strict accordance with the standards and specifications is the prerequisite to solve this defect.
2.3 Fine pitch pin bridging problem
The main factors leading to the bridging defects of the pins of fine pitch components are: a) the solder paste with missing printing is not well formed; b) Fabrication of defective fine pitch leads on the printed board; c) Inappropriate reflow temperature curve setting, etc. Therefore, we should start from the quality control of the key processes such as template making, silk screen printing process, reflow welding process, and try to avoid the hidden danger of bridging.
2.3.1 Selection of formwork materials
70% of the SMT process quality problems come from the printing process, and the template is an essential key tool, which directly affects the printing quality. The template materials we usually use are copper plate and stainless steel plate. Compared with copper plate, stainless steel plate has smaller friction coefficient and higher elasticity, so it is more conducive to solder paste demoulding and solder paste molding under certain other conditions. According to the statistics of the assembly test of QFP208 devices with 0.5mm pin center distance, the number of defects caused by the unqualified omission of copper templates accounts for about 20% of the total number of solder joints (208) of devices; Under certain other conditions, the average defect rate caused by using the stainless steel template to miss printing is 3%. Therefore, for the printing of fine pitch components with pin center distance less than 0.635mm, it is required that stainless steel plates must be used, and the thickness is preferably 0.15mm~0.2mm.
2.3.2 Process control of silk screen printing
Before reflow soldering, if the solder paste collapses, the edge of the formed solder paste pattern is not clear. When placing components or entering the reflow preheating area, pin bridging will be caused due to the softening of the flux in the solder paste. The collapse of solder paste is caused by unsuitable solder paste materials and unsuitable environmental conditions. For example, higher room temperature will cause the collapse of solder paste. In the silk screen process, we carefully control the rheological properties of the solder paste by adjusting the following processes to reduce collapse.
a) The thin template is usually used for silk screen fine pitch leads. To avoid less solder paste missing printing, the required solder paste viscosity should be low, so that the solder paste has good fluidity and is easy to miss printing, and it is not easy to take away the solder paste when the template and PCB are demoulded, so as to ensure the amount of solder paste coating. But at the same time, in order to maintain the ideal shape of solder paste printing graphics, a higher solder paste viscosity is required. Our solution to this contradiction is to use 45-75um smaller particle size and spherical particle solder paste. In addition, the appropriate ambient temperature shall be maintained during silk screen printing. The relationship between solder paste viscosity and ambient temperature is as follows:
logu=A/T+B--(1)
Where: u - viscosity coefficient;
A. B-constant;
T - Absolute temperature.
It can be seen from the above formula that the higher the temperature, the smaller the viscosity. Therefore, in order to obtain higher viscosity, we control the ambient temperature at 20+3 ° C.
b) The speed and pressure of the scraper also affect the rheological properties of the solder paste, because they determine the shear rate and shear force of the solder paste. The relationship between solder paste viscosity and shear rate is shown in Figure 2. When the type of solder paste and the ambient temperature are appropriate, and the pressure of the scraper is constant, slow down the printing speed to keep the viscosity of the solder paste basically unchanged, so that the supply time of the solder paste is longer, the amount of solder paste will increase, and good molding will be achieved. In addition, controlling the slow demoulding rate and the minimum gap between the template and PCB will also play a good role in reducing the fine pitch pin bridge. According to the SP200 screen printing machine we use, we think that the ideal process parameters for printing fine pitch lines are: the printing speed is kept at 10mm/s-25mm/s; The demoulding rate shall be controlled at about 2s; The minimum clearance between the template and PCB is less than or equal to 0.2mm.
2.3.3 Process control of reflux process
The spacing between fine pitch leads is small, the pad area is small, and the amount of solder paste missing is small. During welding, if the temperature of the preheating area of infrared reflow soldering is high and the time is long, more activators will be exhausted before reaching the peak temperature area of reflow soldering. However, only when there is enough activator in the peak area to release the oxidized solder particles, so that the solder particles can melt rapidly, thus wetting the metal pin surface, can a good solder joint be formed. Clean free solder paste has a lower activation than the solder paste to be cleaned. Therefore, if the preheating temperature and time are set slightly improperly, there will be bridging between the thin welding leads. We control the volatilization of the activator in the solder paste by reducing the thermal temperature and preheating time, ensuring the fluidity of the cleaning free solder paste in the welding temperature area and the wettability of the metal lead surface, and reducing the bridging defects of fine pitch lines. For fine pitch devices and RC devices, we adopt the reflow temperature welding curve
With the application of surface mount technology in various fields more widely and deeply, SMT welding quality has attracted great attention. SMT welding quality is closely related to each link of the entire assembly process. In order to reduce or avoid the occurrence of the above welding defects, it is necessary not only to improve the ability of technicians to judge and solve these problems, but also to focus on improving process quality control technology, improving process management, and developing effective control methods. Only in this way can we improve the SMT welding quality and ensure the final quality of PCB products.