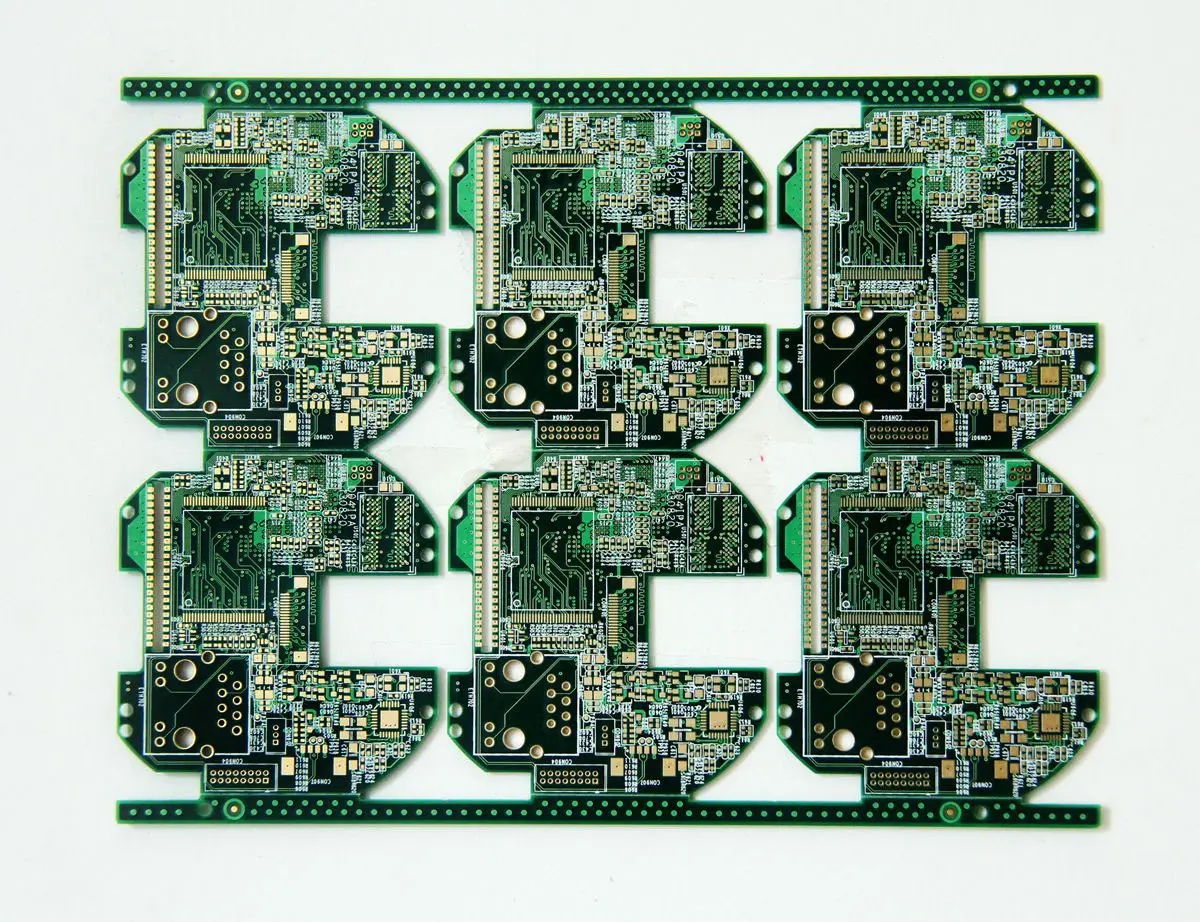
Precautions for manual welding of components in PCB manufacturing
Circuit board manufacturing, circuit board design and PCBA processing manufacturers will explain the manual welding precautions for components manufactured by circuit board
Manual welding points for mounting components
1、 Required equipment:
A hot air gun, an antistatic electric soldering iron, a mobile phone board, a pair of tweezers, an appropriate amount of low melting point solder wire, rosin flux (flux), tin absorbing wire, and plate washing water
Specific steps:
1 Turn on the hot air gun, adjust the air volume and temperature to 230 degrees, 4 speeds: feel the air volume and temperature of the air duct with your hands; Observe whether the air duct has unstable air volume and temperature.
2 Observe that the inside of the air duct is slightly red. Prevent overheating in the air duct.
3 Observe the heat distribution with paper. Find the temperature center.
4. Application and precautions of air nozzle.
5 Blow a resistance with the lowest temperature, and remember the position of the lowest temperature knob that can blow the resistance most.
2) : White light digital display hot air gun:
1 Adjust the air volume knob so that the steel ball indicated by the air volume is in the middle.
2 Adjust the temperature control so that the temperature indication is about 380 ℃.
Note: When the hot air gun is not used for a short time, it should be put into the sleep state (if there is a sleep switch on the handle, press the switch once, if there is no switch on the handle, the air nozzle downward is working, and the air nozzle upward is sleeping). If the hot air gun is not working for more than 5 minutes, it should be turned off.
3) : White 936 digital display thermostatic antistatic soldering iron:
1. The temperature is generally set at 300 ℃. If it is used for welding small components, the temperature can be adjusted lower. If the components to be welded are large or welded on a large area of metal (such as a large area of copper foil for ground wire), the temperature can be appropriately adjusted higher.
2. The soldering head must be white and stained with tin. If it is gray, it must be treated with special sponge.
3. Do not press the solder joint with force during welding, otherwise the PCB board and soldering iron head will be damaged.
4. Turn off the power supply of the soldering iron if it is not used for a long time to avoid empty burning.
5. The electric soldering iron is generally used in the work of removing and welding small components, dealing with welding spots, dealing with short circuits, soldering and flying wires.
2、 Use the hot air gun to disassemble the flatpack IC:
1) : Steps for disassembling flatpack IC:
1 Before removing the components, the IC direction shall be clearly seen, and the components shall not be reversed during reassembly.
2 Observe whether there are heat resistant devices (such as liquid crystal, plastic components, BGA IC with sealant, etc.) beside the IC and on the front and back of the IC. If there are any, cover them with shielding covers and other objects.
3 Add appropriate rosin to the IC pin to be removed to make the PCB pad smooth after the component is removed, otherwise it will burr, and it is not easy to align when re welding.
4 adjusted hot air guns shall be uniformly preheated in an area about 20 square centimeters from the periphery of the components (the air nozzle is about 1cm away from the PCB board, moving at a fast speed at the preheating position, and the temperature on the PCB board shall not exceed 130-160 ℃)
1) In addition to moisture on PCB, avoid "blistering" during repair.
2) Avoid stress warping and deformation between PCB pads caused by excessive temperature difference between upper and lower parts due to sharp heating of one side (upper part) of PCB board.
3) Reduce the thermal shock of parts in the welding area due to heating above the PCB board.
4) Avoid desoldering and warping of nearby IC due to uneven heating
5) PCB and component heating: The distance between the nozzle of the hot air gun and the IC is about 1CM, and it moves slowly and evenly along the IC edge. Use tweezers to gently clamp the diagonal part of the IC.
6) If the solder joint has been heated to the melting point, the hand holding the tweezers will feel it at the first time. Be sure to wait until all the solder on the IC pin is melted, and then carefully lift the component vertically from the board through "zero force", which can avoid damage to the PCB or IC, and also avoid short circuit of solder left by the circuit board. Heating control is a key factor in repair, and the solder must be completely melted to avoid damaging the pad when removing components. At the same time, it is necessary to prevent excessive heating of the board, and the board should not be twisted due to heating. (If conditions permit, 140 ℃ - 160 ℃ can be selected for preheating and low-level heating. The whole process of IC removal shall not exceed 250 seconds)
7) After removing the IC, observe whether the solder joints on the PCB are short circuited. If there is a short circuit, use a hot air gun to reheat it. After the solder at the short circuit is melted, use tweezers to gently scratch along the short circuit, and the solder will naturally separate. Try not to use a soldering iron, because the soldering iron will take away the soldering tin on the circuit board, and the lack of soldering tin on the PCB will increase the possibility of faulty soldering. It is not easy to repair tin on small pin pads. PCB manufacturers, PCB designers and PCBA processors will explain the manual welding precautions for components manufactured by PCB.