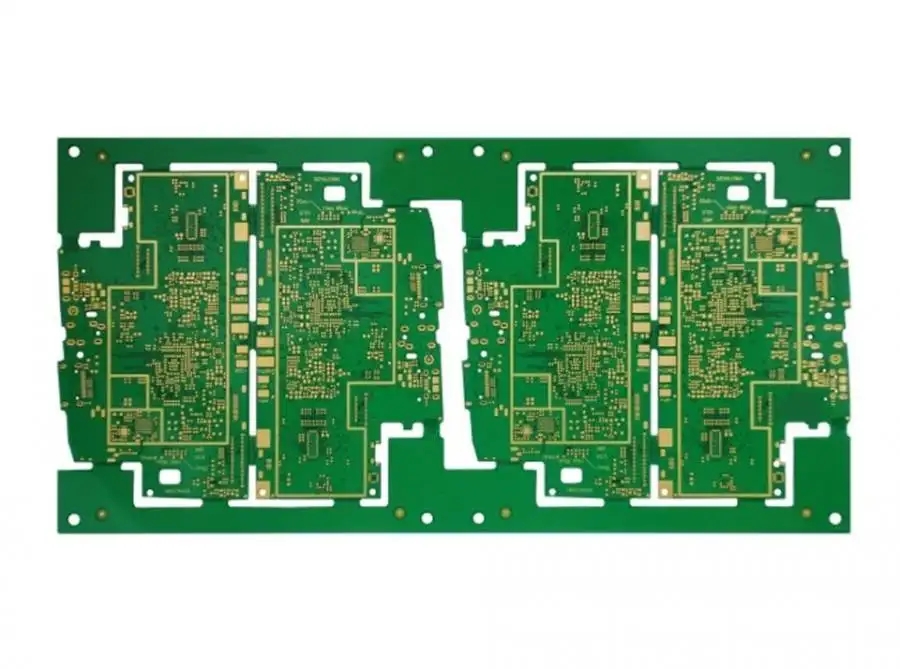
Detailed explanation of several common quality problems of circuit boards
Circuit board manufacturers, circuit board designers and PCBA manufacturers explain several common quality problems of circuit boards in detail
The problems of circuit board quality generally include short circuit, open circuit, green oil bubbling, green oil falling off, red text, substrate delamination, board warping, pad falling off, poor tin coating, and open circuit of the circuit board after aging. The root cause of these common circuit board quality problems lies in the following aspects: poor production process, backward production equipment, poor selection of raw materials, and chaotic management of the circuit board factory.
Reason 1: PCB raw materials are cheap and inferior. The quality of raw materials is the cornerstone of the quality of the circuit board. If the material itself is not up to the standard, the circuit will be blistered, delaminated, cracked, warped and uneven in thickness. What is more hidden now is that some circuit board factories use mixed materials, some of which are genuine and some of which are leftovers, in order to dilute costs. The hidden danger of this is that we do not know which batch will have problems. Due to the different use characteristics of circuit boards, some circuit boards do not have high requirements, so some leftover materials do not show obvious problems when used in this situation, which makes many circuit board manufacturers muddle through such practices, and at the same time, they win the preference of customers because of the low price. It encourages circuit board factories to continue taking such risks. In the long run, if the substrate problem leads to the quality problem of finished products, it is often a huge loss, and sometimes it is impossible to restore the reputation and brand of the enterprise. This is also the reason why more formal circuit board manufacturers will not do so.
Reason 2: backward PCB production equipment. The fundamental way to improve the quality of circuit boards is to ensure the quality of the equipment from the hardware, increase the investment in the equipment, and make the equipment efficient and stable. With the progress of science and technology, the circuit equipment is being updated more and more quickly, and the equipment is becoming more and more advanced. Of course, the price is getting more and more expensive. This has led to the inability of some small circuit board factories to add more expensive equipment, thus increasing the dependence on employees. The current labor cost is inherently high. Once the dependence on skilled employees is formed, the management difficulty of the circuit board factory will be greatly increased. Once personnel turnover occurs, the quality of the circuit board will fluctuate.
Reason 3: PCB production process is not up to standard. Circuit board production is an industry with high scientific and technological content, involving a series of cross disciplines such as electroplating, chemical industry, machinery, etc. Each process of circuit board production must be carried out according to strict production process, and each process must be equipped with corresponding detection and laboratory equipment. These process parameters and equipment can ensure the stability of circuit board quality. It is undeniable that the circuit board industry is also a polluting industry. Many practitioners and even bosses who enter this industry are quite novices, so many small circuit board factories only care about the price, as long as they can lower the cost, they do not care about the production process and circuit board quality at all. The concentration of liquid medicine in the electroplating process is a parameter that varies from time to time. The current size and time of the electroplating process are also different for different types of circuit boards. These parameters together affect the quality of circuit boards. Only strict production process guidance, production according to process parameters, and continuous laboratory inspection can ensure that the quality of the produced circuit board is always stable. If the production is organized based on experience, quality problems occur, and liquid medicine is added according to the feeling, which directly leads to the constant fluctuation of the quality of the circuit board. The customer will have a high repair rate and a low yield rate when using this circuit board, and it seems that the purchase cost of the circuit board is reduced. In fact, the maintenance cost of repair and repair is greatly increased, while the customer brand is affected, which is not cost-effective in the long run.
Reason 4: Management is confused. The circuit board factory has many production processes and long cycle. How to achieve scientific and orderly management and reduce management costs is a difficult problem. It is well managed, manageable and cheap, which requires the long-term accumulation of circuit board manufacturers. With the progress of science and technology, especially the development of network, it is possible to manage the traditional PCB factory by means of network informatization. Only breakthroughs in this field can form the core competitiveness. In a poorly managed factory, the quality of its circuit boards will naturally fluctuate, and various problems will emerge one after another.
To sum up: The quality of circuit boards is a very serious problem. It is also the result of long-term efforts of circuit board factories in management, integrity, investment and absorption of new technical means.
PCB manufacturers, PCB designers and PCBA manufacturers will explain several common quality problems of PCB in detail.