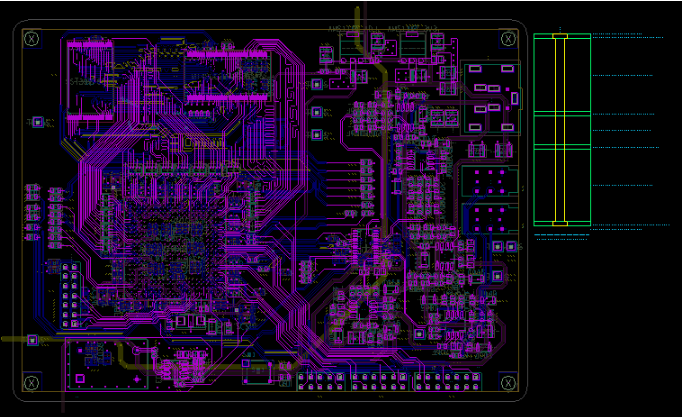
1、 It is mainly used for making high-density and small microporous circuit boards, aiming to save circuit space and reduce PCB volume, such as mobile phone boards,
2、 Classification:
1) . Laser drilling,
1. Reasons for laser drilling:
A. The customer data requires laser drilling;
B Because the blind hole aperture is very small<=6MIL, it can only be drilled with laser
C. Special blind holes, such as L1 to L2 with blind holes and L2 to L3 with buried holes, must be drilled with laser
2. Principle of laser drilling:
Laser drilling is to use the plate to absorb laser heat to vaporize or dissolve the plate into holes. Therefore, the plate must have light absorption. Therefore, general RCC materials do not reflect light because there is no glass fiber cloth in RCC
3. Introduction to RCC materials:
RCC material resin coated copper foil:
It is formed by coating a layer of resin with unique performance on the rough surface of electrolytic copper foil
Three commonly used suppliers: Shengyi, Mitsui and LG
Material: resin thickness 50 65 70 75 80 (um), etc
Copper foil thickness 12 18 (um), etc
RCC materials include high TG and low TG materials, and the dielectric constant is smaller than the normal FR4. For example, the dielectric constant of S6018 of Guangdong Shengyi Company is 3.8, so pay attention when PCB impedance is controlled
Other specific reference materials can be referred to PE and RD departments
4. Requirements for making laser drilling tools:
A) It is difficult for the laser to burn through the copper sheet, so before laser drilling, it is necessary to etch out and complete Cu Clearance with the same aperture at the blind hole
B). The positioning mark of laser drilling shall be added to L2/LN-1 layer, which shall be indicated on the modification page of MI film.
C) The film for blind hole etching must be made with LDI, and the size of LDI plate shall be used for blanking.
Blind buried orifice plate
5. Features of blind orifice production process:
A). When the total number of layers of the line is N, the L2-Ln-1 layers shall be made according to the normal board process,
B). After pressing the board and gong, the process is changed to:
--->Drilling LDI locating hole --->dry film --->etching blind hole spot --->laser drilling --->drilling through hole
--->Copper sinking ---- (normal process).
6. Other precautions for blind hole plate production:
A) As all RCC materials have not passed UL certification, such plates are not marked with UL for the time being
B) With respect to the layout structure on the MI, in order to avoid using this kind of RCC containing material layout as a pseudo laminate layout (because the film room is different from the normal one), we should pay attention to the separation of RCC material from L2 or Ln-1 when drawing the layout structure, such as SR2711/01:
C) . IPC-6016 is the HDI board standard:
Laser blind hole wall copper thickness: 0.4 mil (min)
Requirements for solder ring: tangency is allowed
If the PAD size is less than 5mil larger than the aperture, it is recommended to add TEARDROP
D) . Plate edge>=0.8 "
2) . Mechanical drilling blind/buried hole:
1. Scope of application:
Mechanical drilling can be considered when the drill bit size is>=0.20mm;
2. Electroplating method for blind hole (refer to RD bulletin TSFMRD-113):
A) Under normal conditions, the copper surface of any layer of circuit can only be plated for one time+one time for pattern plating;
B). Under normal conditions, after the full pressing plate process is completed, the plate thickness is>=80MIL, and the through hole requires a plate
Electroplating+pattern electroplating, therefore, the outer PCB surface cannot be plated when the blind hole is plated
C) After meeting the above two conditions, the electroplating of blind holes shall be carried out as follows:
1) When the width of the outer line is greater than 6 MIL and the thickness of the through-hole plate is less than 80 MIL
The outer board surface can be completely plated
2) When the line width of the outer layer is greater than 6 MIL, but the thickness of the through hole plate is greater than 80 MIL, the outer layer plate surface needs to be coated to protect the plate surface during blind hole electroplating;
3) When the line width of the outer layer is less than 6 MIL and the through hole plate thickness is>=80 MIL,
In blind hole electroplating, the outer plate surface shall be coated to protect the plate surface;
3. Film pasting method:
1) Blind hole aspect ratio<=0.8 (L/D)
When the outer layer is pasted with dry film, the whole plate is exposed, and the inner layer is plated with blind hole,
2) When the aspect ratio of the blind hole is>0.8 (L/D), the outer plate surface shall be pasted with dry film and the blind hole shall be exposed. Electroplated exposure point film or LDI shall be made for exposure, and the inner blind hole plate surface shall be electroplated
4. Method of blind hole exposure:
1) When the blind hole<=0.4MM (16MIL), use LDI to expose the blind hole,
2) When the blind hole is>0.4MM (16MIL), expose the blind hole with film,
5. Film pasting method of embedded hole:
1) When the line width of the buried hole surface is<=4 MIL, the surface of the buried hole plate needs to be covered with film and exposed,
2) When the line width of the buried hole surface is>4MIL, the buried hole plate surface is directly plated,
6. Precautions:
1) L/D in aspect ratio: L=medium thickness+copper thickness, D=blind hole/buried hole diameter
2) Blind hole/buried hole electroplated film: * Diameter of exposure point D=D-6 (MIL)
*The coordinates of the exposure point film alignment point are consistent with the peripheral reference hole
3) The blind hole to be coated usually uses pulse current (AC) during electroplating
3、 Some special requirements for blind buried orifice plate:
1. Resin plug blind hole: when the size of the embedded hole is large and the number of holes is large, when pressing plate, it requires a lot of resin to fill the embedded hole. In order to prevent it from affecting the thickness of the pressing plate, if required by R&D, the embedded hole can be pre plugged with resin in front of the pressing plate, and the hole plugging method should refer to the green oil plug hole
2. When there are blind holes in the outer layer,
a. As adhesive will flow out of the outer layer when pressing plate, a glue removal process is required after pressing plate;
b. As the surface of the outer layer will be cleaned before the dry film, there is a plate grinding process. The chemical copper deposition is very thin, only 0.05MIL to 0.1MI, so it is easy to be worn off during plate grinding, so we will add a plate electroplating process to thicken the copper
The relevant processes are as follows: pressing plate - glue removal - drilling - copper deposition - plate electroplating - dry film - pattern electroplating
3. In addition, PIN-LAM pressing plate may be used when making blind hole plates with high layers, but it should be noted that only when the thickness of CORE is less than 30 MIL, our machine can punch PIN-LAM holes, for example, PR4726010, we use ordinary pressing plate
4. As for the edge of blind hole board, it is considered that there are multiple pressing plates and there are many PCB process holes, so the board edge should be kept above 0.8 "as far as possible
5. When writing the LOT card, for the sub process, the layout structure of a single sub process should be written, and the layout structure of the main process should also be written in the special requirements to facilitate the following processes