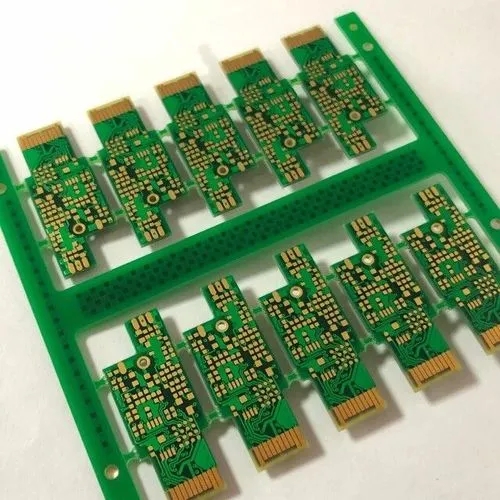
Detailed explanation of the principle of PCB solder
PCB welding is to use molten solder (filler metal) to wet the joint surface and form a metallurgical bond between two metal parts. For solder with higher melting point, welding technology is classified as hard welding technology, which is different from general solder welding in definition. Welding is an important interconnection technology of electronic parts, including the assembly of different levels in various electronic industries.
The human use of welding technology has a history of more than 1000 years, but due to the gradual understanding of metallurgy in modern times, there is a more in-depth understanding. The behavior mode of PCB welding can be roughly divided into three stages: (1) diffusion distribution, (2) base metal melting, and (3) formation of dielectric layer.
Of course, there will be subsequent changes in the state of the metal after welding. During the circuit board welding operation, the flux or gas are kept in the fluid state. The so-called base metal refers to the conductive connecting metal loaded on the substrate, including the metal layer of its surface treatment, such as gold, tin, silver, etc.
To weld the circuit board, the solder must be heated to the molten state first. The molten solder will start wetting the metal surface of the substrate, which is similar to the phenomenon of most liquid wetting substances. Wetting behavior involves the mutual force balance of liquids, which can be analyzed according to the interface tension balance.
When the contact angle is reduced to a small value, the two groups of vectors will reach equilibrium and present a balanced and stable state on the metal solid surface. In electronic welding applications, the so-called good solder joint can reduce the stress concentration and generate a small solder diffusion value of 0.
Small contact angle represents better wetting. It is easier for fluid diffusion distribution to be determined by the balance of interfacial tension. However, the actual welding time is short. If the viscosity of molten solder is high, the solder flow range will be affected, and the actual balance may not be reached. Among the factors that affect viscosity, temperature is an important factor besides the characteristics of the material itself, which is why temperature is considered when discussing viscosity.
In addition, to increase the interfacial tension between solder and flux, it is necessary to reduce the surface tension of flux. Because there are the following interrelationships based on the theoretical deduction of experts:
B=L (surface tension of liquid solder) - Ff (surface tension of flux)
It can be seen from the formula that if the value of FtF is increased, the surface tension Ff of the flux must be reduced. Therefore, the use of low surface tension flux can not only help diffusion but also increase the flow of liquid solder.
The diffusion distribution of melted solder on the metal is not enough to form a good metal bond. To form a good bond, the solder and metal must have appropriate interaction at the interface. Usually, the base metal will be melted into the solder to complete the bond to produce the bonding force.
'For the technology used in electronic welding, it is often limited by the relatively low allowable operating temperature of the materials involved, such as 220 ° C. Moreover, the heating time is relatively short, often not more than a few seconds or minutes, which is of course due to material limitations and capacity considerations. For these reasons, the mutual melting of base metal must occur easily and quickly, which is more conducive to welding.
The circuit board manufacturer and circuit board designer will explain the principle of circuit board solder in detail.