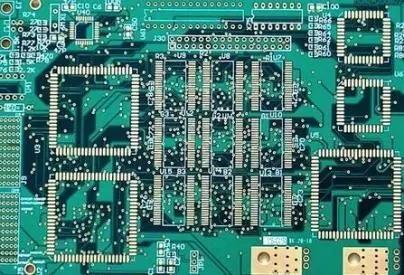
Explanation of the steps of drawing a circuit board
1、 Preliminary work of circuit board design
1. Use schematic design tools to draw schematic diagrams and generate corresponding network tables. Of course, in some special cases, such as the circuit board is relatively simple and there is a network table, you can also enter the PCB design system directly without schematic design. In the PCB design system, you can directly take parts for packaging and manually generate the network table.
2. Manually change the network table to define pads that are not on the schematic diagrams such as fixed pins of some components to the network connected to it. Pads that are not physically connected can be defined to the ground or protected ground. Change the device pin names in some schematic diagrams and PCB packaging library that are inconsistent with the pin names to be consistent with those in PCB packaging library, especially diode and triode.
2、 It is recommended to put the components you have drawn into a PCB library special design file you have created.
3、 Setting the PCB design environment and drawing the frame of the printed circuit, including the hollowing in the middle
The first step after entering the PCB system is to set the PCB design environment, including grid size and type, cursor type, plate layer parameters, wiring parameters, etc. Most parameters can use the system default values, and these parameters, after being set, conform to personal habits and do not need to be modified in the future. 2. Planning the circuit board is mainly to determine the border of the circuit board, including the size of the circuit board, etc. Place a pad of appropriate size where the fixing hole needs to be placed. For 3mm screws, the pads with 6.5~8mm outer diameter and 3.2~3.5mm inner diameter can be used. For standard boards, they can be transferred from other boards or PCB izard.Note: Before drawing the floor frame of the circuit board, be sure to set the current layer as the Keep Out layer, that is, the routing layer is prohibited.
4、 After opening all the PCB library files to be used, it is a very important step to call in the network table file and modify the part packaging. The network table is the soul of PCB automatic wiring, and is also the interface between schematic design and impression circuit board design. Only after the network table is loaded can the circuit board be wired. In the process of schematic design, ERC inspection will not involve the encapsulation of parts. Therefore, the packaging of parts may be forgotten during schematic design, and the packaging of parts can be modified or supplemented according to the design situation when introducing network tables. Of course, you can manually generate the network table directly in the PCB, and specify part packaging.
5、 The location of part package, also known as part layout Protel99, can be arranged automatically or manually. For automatic layout, run "Auto Place" under "Tools". You need to be patient with this command. The key of routing is layout, and most designers adopt the form of manual layout. Select a component with the mouse, press and hold the left mouse button, drag the component to the destination, and release the left button to fix the component. Protel99 has added some new skills in layout. New interactive layout options include automatic selection and automatic alignment. Using the automatic selection method, you can quickly collect components with similar packages, then rotate, expand and organize them into groups, and then move them to the desired position on the board. When the simple layout is completed, use auto alignment to neatly expand or shrink a group of encapsulated similar components.
Tip: During automatic selection, use Shift+X or Y and Ctrl+X or Y to expand and shrink the X and Y directions of the selected components.
Note: The layout of parts shall be comprehensively considered from the aspects of heat dissipation of mechanical structure, electromagnetic interference, convenience of future wiring, etc. First, arrange the devices related to mechanical dimensions, and lock these devices, then the large occupying devices and the core components of the circuit, and then the small peripheral components.
6、 Make appropriate adjustment according to the situation and lock all components
If the space on the board allows, some wiring areas similar to the experimental board can be placed on the board. For large plates, additional fixing screw holes shall be added in the middle. Fixed screw holes shall also be added on the side of stressed components such as heavy components or large connectors on the board. If necessary, some test pads can be placed at appropriate locations, preferably in the schematic diagram. Enlarge the vias of pads that are too small, and define the network of all pads with fixed screw holes to the ground or protective ground.
After placing it, use the VIEW3D function to check the actual effect and save it.
7、 Routing Rules Setting Routing rules is to set various specifications for routing (such as the use layer, line width of each group, via spacing, topology structure of routing, and other rules, which can be exported from other boards through the Menu of Design Rules, and then imported into this board). This step does not need to be set every time. It can be set once according to personal habits. To select Design Rules, you need to reset the following points:
1. Safety clearance (Clearance Constraint of Routing label)
It specifies the distance that must be kept between wiring pad vias of different networks on the board. General boards can be set as 0.254mm, empty boards can be set as 0.3mm, and dense patch boards can be set as 0.2-0.22mm. The production capacity of a few printing plate processing manufacturers is 0.1-0.15mm. If you can get their consent, you can set this value. Below 0.1mm is absolutely prohibited.
2. Routing Layer and Direction (Routing Layers of Routing Label)
Here you can set the used routing layer and the main routing direction of each layer. Please note that the single panel of the patch only uses the top layer, and the straight plug single panel only uses the bottom layer. However, the power layer of the multilayer board is not set here (you can click the top layer or bottom layer in the Design Layer Stack Manager, add it with Add Plane, double-click it with the left mouse button, and delete it with Delete), The mechanical layer is not set here (you can select the mechanical layer to be used in the Design Mechanical Layer, and select whether it is visible and whether it is displayed in the single-layer display mode at the same time). Mechanical layer 1 is generally used to draw the frame of the board; The mechanical layer 3 is generally used to draw the mechanical structural parts such as the bars on the board; Mechanical layer 4 is generally used to draw scales and notes. You can export a board with PCAT structure from the PCB Wizard
3. Through hole shape (Routing Via Style of Routing label)
It specifies the inner and outer diameters of vias automatically generated during manual and automatic wiring, which are divided into minimum, maximum and preferred values, of which the preferred value is the most important, the same below.
4. Width Constraint of Routing Label
It specifies the width of wiring in manual and automatic wiring. The preferences of the whole board range are generally 0.2-0.6mm. In addition, add some line width settings of the network or network class, such as ground wire,+5V power line, AC power input line, power output line, and power pack. The network group can be defined in the Design Netlist Manager in advance. The ground wire can be 1mm wide in general, and various power lines can be 0.5-1mm wide in general. The relationship between the line width of the printed board and the current is about 1 ampere of current per mm of line width. For details, please refer to the relevant information. When the preferred value of wire diameter is too large for the SMD pad to be routed automatically, it will automatically reduce to a section of routing between the minimum width and the width of the pad when it enters the SMD pad. Board is the line width constraint of the whole Board, and its priority is the lowest. That is, it first meets the line width constraints of networks and network groups when routing. The following figure is an example
5. Setting of copper coated connection shape (Polygon Connect Style of Manufacturing label)
It is recommended that the conductor width of the Reliaf Connect mode should be 0.3-0.5mm, and four conductors should be 45 or 90 degrees. Other items can generally use their original default values, while items such as the topology of cabling, the spacing of power layers, and the network length matching the connection shape can be set as required. Select Tools Preferences. In the Interactive Routing section of the Options bar, select the Push Obstacle mode (push other routes when encountering routes of different networks, Ignore Obstacle is through, and Avoid Obstacle is blocking) and select Automatically Remove. The Track and Via in the Defaults column can also be changed. It is generally unnecessary to move them. Place FILL filling layer in the area where no wiring is expected, such as the wiring layer under the radiator and horizontal bipod crystal oscillator, and place FILL at the corresponding position of the top or bottom Solder where tin is required. Routing rule setting is also one of the keys to PCB design, which requires rich practical experience.